RXM-900-HP3-PPO Linx Technologies Inc, RXM-900-HP3-PPO Datasheet - Page 9
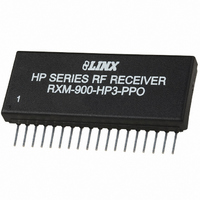
RXM-900-HP3-PPO
Manufacturer Part Number
RXM-900-HP3-PPO
Description
RECEIVER RF 900MHZ 8-CHANNEL
Manufacturer
Linx Technologies Inc
Series
HP3r
Datasheet
1.MDEV-900-HP3-PPS-RS232.pdf
(13 pages)
Specifications of RXM-900-HP3-PPO
Frequency
902MHz ~ 928MHz
Sensitivity
-100dBm
Data Rate - Maximum
56 kbps
Modulation Or Protocol
FM, FSK
Applications
Home / Industrial Automation, Remote Access, Security Alarms
Current - Receiving
18mA
Data Interface
PCB, Through Hole
Antenna Connector
Through Hole
Features
Multiple Channels, Analog and Digital Data
Voltage - Supply
2.8 V ~ 13 V
Operating Temperature
-30°C ~ 85°C
Package / Case
18-SIP
Lead Free Status / RoHS Status
Contains lead / RoHS non-compliant
Memory Size
-
Other names
RXM900HP3PPO
Available stocks
Company
Part Number
Manufacturer
Quantity
Price
Company:
Part Number:
RXM-900-HP3-PPO_
Manufacturer:
LNX
Quantity:
17
PAD LAYOUT
Figure 18: Recommended PCB Layout
PRODUCTION GUIDELINES
HAND ASSEMBLY
Page 16
0.060
Reflow Oven: +220°C Max. (See adjoining diagram)
The following pad layout diagram is designed to facilitate both hand and
automated assembly.
The modules are housed in a hybrid SMD package that supports hand or
automated assembly techniques. Since the modules contain discrete
components internally, the assembly procedures are critical to ensuring the
reliable function of the modules. The following procedures should be reviewed
with and practiced by all assembly personnel.
Pads located on the bottom of the
module are the primary mounting
surface. Since these pads are
inaccessible
castellations that run up the side of
the module have been provided to
facilitate solder wicking to the
module’s underside. This allows for
very quick hand soldering for
prototyping and small volume
production.
If the recommended pad guidelines have been followed, the pads will protrude
slightly past the edge of the module. Use a fine soldering tip to heat the board
pad and the castellation, then introduce solder to the pad at the module’s edge.
The solder will wick underneath the module, providing reliable attachment. Tack
one module corner first and then work around the device, taking care not to
exceed the times listed below.
Hand-Solder Temp. RX +225°C for 10 Seconds
Hand-Solder Temp. TX +225°C for 10 Seconds
Absolute Maximum Solder Times
Recommended Solder Melting Point +180°C
0.060
Pinned Receiver
0.030 Dia. Finished
during
0.100
mounting,
Figure 19: Soldering Technique
Solder
Soldering Iron
Tip
PCB Pads
0.090
Surface-Mount Receiver
Castellations
0.100
0.065
0.750
AUTOMATED ASSEMBLY
Figure 20: Maximum Reflow Profile
Reflow Temperature Profile
Shock During Reflow Transport
Washability
For high-volume assembly, most users will want to auto-place the modules. The
modules have been designed to maintain compatibility with reflow processing
techniques; however, due to the their hybrid nature, certain aspects of the
assembly process are far more critical than for other component types.
Following are brief discussions of the three primary areas where caution must be
observed.
The single most critical stage in the automated assembly process is the reflow
stage. The reflow profile below should not be exceeded, since excessive
temperatures or transport times during reflow will irreparably damage the
modules. Assembly personnel will need to pay careful attention to the oven’s
profile to ensure that it meets the requirements necessary to successfully reflow
all components while still remaining within the limits mandated by the modules.
The figure below shows the recommended reflow oven profile for the modules.
Since some internal module components may reflow along with the components
placed on the board being assembled, it is imperative that the modules not be
subjected to shock or vibration during the time solder is liquid. Should a shock
be applied, some internal components could be lifted from their pads, causing
the module to not function properly.
The modules are wash resistant, but are not hermetically sealed. Linx
recommends wash-free manufacturing; however, the modules can be subjected
to a wash cycle provided that a drying time is allowed prior to applying electrical
power to the modules. The drying time should be sufficient to allow any moisture
that may have migrated into the module to evaporate, thus eliminating the
potential for shorting damage during power-up or testing. If the wash contains
contaminants, the performance may be adversely affected, even after drying.
300
250
200
150
100
50
0
255°C
235°C
217°C
185°C
180°C
125°C
30
Recommended RoHS Profile
Max RoHS Profile
60
90
120
150
Time (Seconds)
180
Recommended Non-RoHS Profile
210
240
270
300
330
Page 17
Page 17
360