H-37-2 Bourns Inc., H-37-2 Datasheet - Page 37
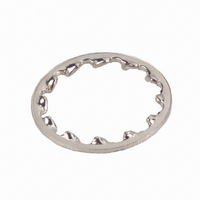
H-37-2
Manufacturer Part Number
H-37-2
Description
HDWR LOCKWASHER FOR ECW ENCODER
Manufacturer
Bourns Inc.
Specifications of H-37-2
Product
Lock Washer
Lead Free Status / RoHS Status
Lead free / RoHS Compliant
For Use With
ECW1DB24BC0024 - ENCODER DIGITAL CONT 24 CPRECW1JB24BC0024 - ENCODER DIGITAL CONT 24 CPR
Lead Free Status / Rohs Status
Lead free / RoHS Compliant
36
ENS Style Encoders
Radial Load Axial Load (lb)
Application Notes
Incremental encoders can also be used to drive
standard up/down counters. In such cases, we suggest
using interface ICs similar to the LS7083 and LS7084
Encoder to Counter Interface Chips manufactured by
US Digital. The diagram in Figure 21 shows a typical
circuit configuration for an encoder applied to drive
an up/down counter. For additional information and
specification sheet for these devices, visit US Digital’s
website at http://www.usdigital.com.
Figure 21: Up/Down Counter Driver Circuit
Notes:
10.0
1) Radial loads are assumed to be applied 1/2” from the front
2) The static load rating (C
3) If R=radial load, AP=axial push load and APL=axial pull load,
(lb)
1.0
0.5
3.0
1.5
2.5
5.0
mounting surface (FMS)
(1/8” shaft dia.) and 21 lbs. for ENS versions (1/4” shaft dia.).
recommended loading limits are as follows:
Push
1
0
3
0
0
0
0
2R + APL < C
R + AP <C
0
) is 10.7 lbs. for ENT and ENW styles
Pull
0
1
0
3
0
0
5
L
0
10
0
100 RPM
and,
8.3 x 10
8.3 x 10
5.5 x 10
5.5 x 10
1.2 x 10
1.4 x 10
2.4 x 10
Life (Hrs)
6
6
5
5
6
5
4
3,000 RPM
1.7 x 10
1.7 x 10
1.1 x 10
1.1 x 10
2.9 x 10
2.9 x 10
4.8 x 10
5
5
4
4
3
3
2
ENT and ENW Style Encoders
Radial Load Axial Load (lb)
Encoders
Application Information for EN Series Optical
Encoder
Bourns® optical encoder produces a 2-bit quadrature
signal that is suitable for digital systems where both
magnitude and direction of adjustment must be
provided. Utilizing solid-state electronics to create
the output signal, these encoders have no contacts
that will wear or create electrical noise. The optical
encoder is ideal as a digital panel control or a
position-sensing device in applications where long
life, reliability, accuracy, and high resolution are
critical.
Rotational Speed/Life
Most bushing mount encoders on the market are
limited to rotational speeds of 300 rpm and have a
rotational life of 10 x 10
operating speed and life specifications, ball bearing
shaft supports are added. For high speed and/or
extended life applications, Bourns offers shaft ball
bearings in either bushing or flange mount versions.
With ball bearings, the EN series is capable of
operating speeds of 3000+ rpm with a rotational life
of up to 5 x 10
Shaft Loading
To accurately predict the rotational life of an
encoder, the end (axial) and side (radial) loading
forces should be understood. The relationship
between shaft loading and rotational life for the EN
series is expressed in the tables below. Life is shown
here in operating hours (of continuous rotation) at
the speed indicated.
Note: Life rating estimates are based on metal fatigue
failure criteria. Retention of lubricants may be a
limiting factor in extended life applications.
10.0
(lb)
1.0
0.5
3.0
1.5
2.5
5.0
8
Push
revolutions.
1
0
3
0
0
0
0
6
Pull
revolutions. To increase
0
1
0
3
0
0
5
L
10
100 RPM
4.3 x 10
4.3 x 10
2.8 x 10
2.8 x 10
4.8 x 10
6.0 x 10
1.1 x 10
Life (Hrs)
6
6
5
5
5
4
4
3,000 RPM
8.5 x 10
8.5 x 10
5.6 x 10
5.6 x 10
9.6 x 10
1.2 x 10
2.2 x 10
4
4
3
3
3
3
2