13949 AIM - American Iron and Metal, 13949 Datasheet
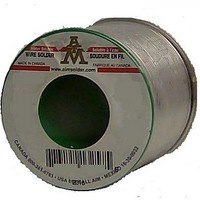
13949
Manufacturer Part Number
13949
Description
Solder, Fluxes & Accessories SAC305 WS482 3% .032 DIA 1 lb.
Manufacturer
AIM - American Iron and Metal
Datasheet
1.13949.pdf
(1 pages)
Specifications of 13949
Description/function
Lead Free Water Soluble
Alloy
SAC305
Diameter
0.032 in
Weight
1 lb
Core Size
3%
Lead Free Status / RoHS Status
Lead free / RoHS Compliant
Available stocks
Company
Part Number
Manufacturer
Quantity
Price
Company:
Part Number:
1394918-3
Manufacturer:
TE
Quantity:
35 000
Features:
- Halide-Free
- High Activity Level
Description:
WS482 is a water soluble, halide-free flux cored wire that is highly active and compatible with water soluble solder paste
chemistries. WS482 offers improved thermal stability, allowing it to be processed with standard or high temperature alloys.
WS482 offers residues that are non-corrosive and therefore may be used without cleaning for applications where
conductivity will not cause a problem (such as soldering wires). Post-process residues are safe to remain on many
assemblies for up to two to three days. WS482 produces excellent tarnish and oxide removal, will not tarnish PCBs, copper,
or solder joints, and offers excellent wetting and soldering characteristics. WS482 flux residue is readily soluble in hot
water. IPC flux classification for this material is ORL0.
Availability:
-
-
-
-
-
Application:
-
-
-
-
-
Cleaning:
Post-process residues should be removed within a two to three day period. Deionized water is recommended for the final
rinse. A temperature of 38º - 60ºC (100° - 140°F) is sufficient for removing residues. An in-line or other pressurized spray
cleaning system is suggested, but is not required.
Handling and Storage:
-
-
-
Safety:
-
-
-
The information contained herein is based on data considered accurate and is offered at no charge. Product information is based upon the assumption of
proper handling and operating conditions. All information pertaining to solder paste is produced with 45-micron powder. Liability is expressly
disclaimed for any loss or injury arising out of the use of this information or the use of any materials designated. Please refer to
http://www.aimsolder.com/terms.cfm
WS482 is standard with a 3.0% flux core for tin-lead (3.0% flux core for lead-free) alloys.
WS482 is available in Sn/Pb, Sn/Ag/Cu, SN100C
Standard spool sizes; ½ lb. for .010 and .015 diameters, 1 lb. for .020, .032, .040, .050, and .062 diameters.
Packaging of ½ lb. and 1 lb. spools is standard in 12 lb. and 24 lb. cases.
Other flux percentages, alloys, diameters and spool sizes may be available upon special request.
Solder iron tip temperature should be between 350° - 400°C (650° - 750°F ) for Sn63 and Sn62 alloys, 370° - 425°C
(700° - 800°F) for Sn/Ag and Sn/Ag/Cu alloys.
Hold the solder iron at a 45° to 60° angle to the work surface.
The solder iron should contact both the component lead and PCB pad surface.
Solder and flux should flow onto both the lead and pad or lead and barrel to promote optimum flux activity to the joint
being worked.
If additional flux is needed, the use of AIM’s 716 flux is recommended. Operators should use an applicator capable of
dispensing precise amounts of flux to eliminate over-saturation and excessive flux spread.
WS482 cored wire has an indefinite shelf life when proper storage conditions are observed.
Store WS482 in a clean dry area away from moisture and sunlight.
Do not freeze this product.
Use with adequate ventilation and proper personal protective equipment.
Refer to the accompanying MSDS for any specific emergency information.
Do not dispose of any hazardous materials in non-approved containers.
Americas +1-401-463-5605 · Europe +44-1737-222-258 · Asia-Pacific +86-755-2993-6487 · info@aimsolder.com · www.aimsolder.com
to review AIM's terms and conditions.
- Good Thermal Transfer
- Good Wetting Properties
Manufacturing and Distribution Worldwide
Water Soluble Cored Wire Solder
AIM
WS482
IS
®
ISO9001:2000 C
alloys.
ERTIFIED
- Extended Cleaning Times, Safe Up to 2 to 3 Days
- For Standard and High-Temperature Applications
08/09
Rev 2