HMC1022 Honeywell Microelectronics & Precision Sensors, HMC1022 Datasheet - Page 6
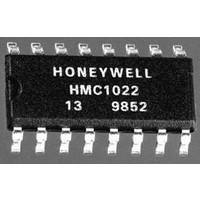
HMC1022
Manufacturer Part Number
HMC1022
Description
Magnetic Sensor
Manufacturer
Honeywell Microelectronics & Precision Sensors
Datasheets
1.HMC1021.pdf
(15 pages)
2.HMC1022.pdf
(15 pages)
3.HMC1022.pdf
(15 pages)
4.HMC1022.pdf
(15 pages)
Specifications of HMC1022
Sensitivity Range
1mV/V/G
Sensor Output
Voltage
Terminal Type
PCB Thru Hole
Output Type
Differential
Sensor Terminals
SMD Gull Wing
Leaded Process Compatible
No
Magnetic Field Max
6G
Axis Configuration
Two
Lead Free Status / RoHS Status
Lead free / RoHS Compliant
Available stocks
Company
Part Number
Manufacturer
Quantity
Price
Company:
Part Number:
HMC1022
Manufacturer:
honeywell
Quantity:
12 800
Part Number:
HMC1022
Manufacturer:
HONEYWE
Quantity:
20 000
Part Number:
HMC1022-TR
Manufacturer:
HITTITE
Quantity:
20 000
LINEAR MAGNETIC FIELD SENSORS
BASIC DEVICE OPERATION
Honeywell magnetoresistive sensors are simple resistive
bridge devices (Figure 1) that only require a supply voltage
to measure magnetic fields. When a voltage from 0 to 10
volts is connected to Vbridge, the sensor begins measuring
any ambient, or applied, magnetic field in the sensitive axis.
In addition to the bridge circuit, the sensor has two on-chip
magnetically coupled straps—the OFFSET strap and the
Set/Reset strap. These straps are patented by Honeywell
and eliminate the need for external coils around the devices.
Magnetoresistive sensors are made of a nickel-iron
(Permalloy) thin film deposited on a silicon wafer and
patterned as a resistive strip. In the presence of an applied
magnetic field, a change in the bridge resistance causes a
corresponding change in voltage output.
An external magnetic field applied normal to the side of the
film causes the magnetization vector to rotate and change
angle. This in turn will cause the resistance value to vary ( R/
R) and produce a voltage output change in the Wheatstone
bridge. This change in the Permalloy resistance is termed the
magnetoresistive effect and is directly related to the angle of
the current flow and the magnetization vector.
During manufacture, the easy axis (preferred direction of
magnetic field) is set to one direction along the length of the
film. This allows the maximum change in resistance for an
applied field within the permalloy film. However, the influence
of a strong magnetic field (more than 10 gauss) along the
easy axis could upset, or flip, the polarity of film
magnetization, thus changing the sensor characteristics.
Following such an upset field, a strong restoring magnetic
field must be applied momentarily to restore, or set, the
sensor characteristics. This effect will be referred to as
applying a set pulse or reset pulse. Polarity of the bridge
output signal depends upon the direction of this internal film
magnetization and is symmetric about the zero field output.
OUT+
(5)
Figure 1—On-Chip components (HMC1001)
R
R
R=600-1200
Vbridge
GND
(7)
(4)
R
R
OUT-
(8)
OFFSET +
S/R +
(2)
(1)
2.0
Iset, -Ireset
3.5
Ioffset
max.
max.
OFFSET -
S/R -
(3)
(6)
6
The OFFSET strap allows for several modes of operation
when a dc current is driven through it.
• An unwanted magnetic field can be subtracted out
• The bridge offset can be set to zero
• The bridge output can drive the OFFSET strap to cancel
• The bridge gain can be auto-calibrated in the system on
The Set/Reset (S/R) strap can be pulsed with a high current to:
• Force the sensor to operate in the high sensitivity mode
• Flip the polarity of the output response curve
• Be cycled during normal operation to improve linearity
The output response curves shown in Figure 2 illustrate the
effects of the S/R pulse. When a SET current pulse (Iset) is
driven into the SR+ pin, the output response follow the curve
with the positive slope. When a RESET current pulse
(Ireset) is driven into the SR- pin, the output response follow
the curve with the negative slope. These curves are mirror
images about the origin except for two offset effects.
In the vertical direction, the bridge offset shown in Figure 2,
is around -25mV. This is due to the resistor mismatch during
the manufacture process. This offset can be trimmed to zero
by one of several techniques. The most straight forward
technique is to add a shunt (parallel) resistor across one leg
of the bridge to force both outputs to the same voltage. This
must be done in a zero magnetic field environment, usually
in a zero gauss chamber.
The offset of Figure 2 in the horizontal direction is referred to
here as the external offset. This may be due to a nearby ferrous
object or an unwanted magnetic field that is interfering with the
applied field being measured. A dc current in the OFFSET
strap can adjust this offset to zero. Other methods such as
shielding the unwanted field can also be used to zero the
external offset. The output response curves due to the SET
and RESET pulses are reflected about these two offsets.
Figure 2—Output Voltage vs. Applied Magnetic Field
out the field being measured in a closed loop configuration
command.
and reduce cross-axis effects and temperature effects.
-20
-40
-60
-80
40
20
0
response
after Ireset
Vcc=8V
external
offset
(1001/1002)
Applied Field (Gauss)
bridge
offset
response
after Iset