LTC1272-3ACSW#PBF Linear Technology, LTC1272-3ACSW#PBF Datasheet - Page 11
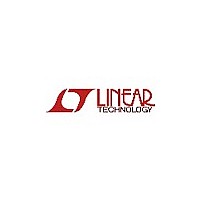
LTC1272-3ACSW#PBF
Manufacturer Part Number
LTC1272-3ACSW#PBF
Description
IC A/D CONV 12BIT SAMPLNG 24SOIC
Manufacturer
Linear Technology
Datasheet
1.LTC1272-3CCSW.pdf
(20 pages)
Specifications of LTC1272-3ACSW#PBF
Number Of Bits
12
Sampling Rate (per Second)
250k
Data Interface
Parallel
Number Of Converters
1
Power Dissipation (max)
75mW
Voltage Supply Source
Single Supply
Operating Temperature
0°C ~ 70°C
Mounting Type
Surface Mount
Package / Case
24-SOIC (0.300", 7.50mm Width)
Lead Free Status / RoHS Status
Lead free / RoHS Compliant
Available stocks
Company
Part Number
Manufacturer
Quantity
Price
A
Application Hints
Wire wrap boards are not recommended for high resolu-
tion or high speed A/D converters. To obtain the best
performance from the LTC1272 a printed circuit board is
required. Layout for the printed circuit board should
ensure that digital and analog signal lines are separated as
much as possible. In particular, care should be taken not
to run any digital track alongside an analog signal track or
underneath the LTC1272. The analog input should be
screened by AGND.
A single point analog ground separate from the logic
system ground should be established with an analog
ground plane at pin 3 (AGND) or as close as possible to the
LTC1272, as shown in Figure 11. Pin 12 (LTC1272 DGND)
and all other analog grounds should be connected to this
single analog ground point. No other digital grounds
should be connected to this analog ground point. Low
impedance analog and digital power supply common
returns are essential to low noise operation of the ADC and
0V TO 5V
ANALOG
Figure 10. Unipolar 0V to 5V Operation with Gain Error Adjust
PPLICATI
INPUT
*ADDITIONAL PINS OMITTED FOR CLARITY
V
IN
+
–
LT1007
A1
O
U
S
CIRCUITRY
ANALOG
I FOR ATIO
INPUT
U
R1
200Ω
15Ω
20k
R2
R3
+
–
1
W
A
IN
Figure 11. Power Supply Grounding Practice
AGND
3
1
3
A
AGND
LTC1272
IN
C1
U
LTC1272 • TA12
V
REF
LTC1272
2
ANALOG GROUND PLANE
C2
C3
the foil width for these tracks should be as wide as
possible.
Noise: Input signal leads to A
from AGND (pin 3) should be kept as short as possible to
minimize input noise coupling. In applications where this
is not possible, a shielded cable between source and ADC
is recommended. Also, since any potential difference in
grounds between the signal source and ADC appears as an
error voltage in series with the input signal, attention
should be paid to reducing the ground circuit impedances
as much as possible.
In applications where the LTC1272 data outputs and
control signals are connected to a continuously active
microprocessor bus, it is possible to get LSB errors in
conversion results. These errors are due to feedthrough
from the microprocessor to the successive approximation
comparator. The problem can be eliminated by forcing the
microprocessor into a Wait state during conversion (see
Slow Memory Mode interfacing), or by using three-state
buffers to isolate the LTC1272 data bus.
Timing and Control
Conversion start and data read operations are controlled
by three LTC1272 digital inputs; HBEN, CS and RD. Figure
12 shows the logic structure associated with these inputs.
The three signals are internally gated so that a logic “0” is
required on all three inputs to initiate a conversion. Once
initiated it cannot be restarted until conversion is com-
plete. Converter status is indicated by the BUSY output,
and this is low while conversion is in progress.
V
DD
24
C4
DGND
12
GROUND CONNECTION
TO DIGITAL CIRCUITRY
SYSTEM
DIGITAL
LTC1272 • TA13
IN
and signal return leads
LTC1272
11
1272fb