SMS3.3TCT Semtech, SMS3.3TCT Datasheet - Page 6
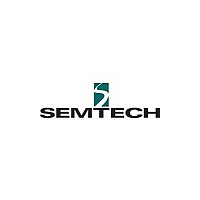
SMS3.3TCT
Manufacturer Part Number
SMS3.3TCT
Description
Manufacturer
Semtech
Datasheet
1.LC03-3.3TBT.pdf
(12 pages)
Component Selection - Introduction
Referring to the 6 LED typical schematic below, there are
three components that depend upon the application that
need to be determined:
RSET - this resistor sets the output current for the device
RLIM - this resistor sets the peak inductor current
L - the output inductor
All the other components can be mostly generalized and
are addressed below the following design steps.
IOUT ADJUST
Step 1: Continuous or Discontinuous?
The first thing to do when designing with the SC104 is to
determine whether the output inductor will be operating
in continuous mode (where the inductor current does not
drop to zero while the device is switching) or discontinuous
mode (where the inductor current drops to zero while
switching). This determination can be made simply by
calculating the required duty cycle needed for the target
output voltage, and comparing it to the guaranteed
minimum value for the maximum duty cycle from the
Electrical Characteristics on Page 3. %
duty). If DC is greater than 0.7 then discontinuous mode
is required. The required duty cycle is calculated as
follows:
Where:
V
forward voltage drop at the required output voltage
plus the feedback voltage, 0.35V.
V
V
V
Using the 6 LED example above:
V
V
DC
POWER MANAGEMENT
IOUT = 15mA
Applications Information
OUT
IN
f
CE(SAT)
OUT
IN
2005 Semtech Corp.
= Schottky diode (D1) forward voltage drop
= minimum input voltage
= 3V
=
= output voltage, the sum of the total LED (max.)
= (6 * 3.475) + 0.35 = 21.2V
(
= power switch saturation voltage
V
LED4
OUT
(
LED3
V
OUT
−
LED5
V
−
LED2
CE
V
(
IN
SAT
LED6
+
LED1
RSET
23.2R
)
V
+
f
V
)
f
)
COUT
0.47uF
1
2
3
4
U1
ADJ
FB
GND
OUT
D1
DC(MIN)
SC104
LIM
EN
IN
LX
8
7
6
5
= 70% (or 0.7
VIN = 3V to 5V
L1
12uH
CIN
4.7uF
RLIM
7.50k
ENABLE
6
V
V
thus DC = 0.87
Since this value is greater than the guaranteed minimum
value for maximum duty cycle, the device will be operating
in discontinuous mode to provide the desired output. Note
that the duty cycle does not depend upon the output
current, and that unless the output to input ratio is low,
the device will usually need to be in discontinuous mode,
so we will cover that first (Step 1 through Step 5).
Continuous mode calculations start at Step 6.
Step 2: Calculating the Inductor for Discontinuous Mode
Having determined that we need to be operating in
discontinuous mode, we next need to calculate the
maximum inductor value allowed that will permit the part
to output the correct power. The maximum discontinuous
inductor value, L
Where:
t
I
t
Using our 6 LED example:
I
thus L
Selecting the next lower standard value gives us
L
if desired, but may not necessarily be the most efficient
choice.
Step 3: Calculating the Current Limit Required with this
Inductor for Discontinuous Mode
Having determined the inductor value we are going to use,
we next need to calculate the current limit required to
meet the necessary output power. The discontinuous
mode current limit, I
L
I
OUT
OUT
ON(MIN)
OFF(MIN)
LIM
(D)
f
CE(SAT)
(
D
= 0.35V
)
(
= 12µH. Of course a lower value inductor may be used
D
= required output current
= 15mA
=
)
2
=
= minimum switch on-time = 1.8µs
(D)
= 0.25V
= minimum switch off-time = 0.6µs
•
(
1
V
= 14.4µH
4 .
t
IN
ON
•
−
(
MIN
V
V
OUT
)
CE
2
•
(D)
(
L
•
SAT
V
I
(
OUT
D
IN
is given by:
)
)
•
)
LIM(D)
•
•
(
V
(
t
t
IN
ON
ON
, is given by:
−
(
(
MIN
MIN
V
CE
)
)
+
(
SAT
t
OFF
)
)
(
MIN
)
)
•
(
V
OUT
(
www.semtech.com
V
OUT
SC104
−
V
−
CE
V
(
IN
SAT
+
)
V
+
f
V
)
f
)