NJM3771FM2-TE3 NJR, NJM3771FM2-TE3 Datasheet - Page 7
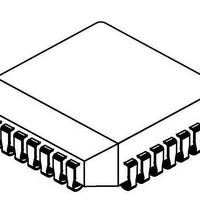
NJM3771FM2-TE3
Manufacturer Part Number
NJM3771FM2-TE3
Description
Motor / Motion / Ignition Controllers & Drivers Dual Stepper Motor Driver
Manufacturer
NJR
Type
Stepper Motor Controller/Driverr
Datasheet
1.NJM3771FM2.pdf
(9 pages)
Specifications of NJM3771FM2-TE3
Product
Stepper Motor Controllers / Drivers
Operating Supply Voltage
10 V to 45 V
Supply Current
38 mA to 50 mA
Mounting Style
SMD/SMT
Package / Case
PLCC-28
Lead Free Status / Rohs Status
Lead free / RoHS Compliant
External components
The voltage across the sensing resistor is fed back to the comparator via a low-pass filter section, to prevent
erroneous switching due to switching transients. The recommended filter component values, 1 kohm and 820 pF,
are suitable for a wide range of motors and operational conditions.
the sensing resistor, and hence the peak motor current, will reach a slightly higher level than the threshold, V
by the reference voltage
(V
performance, especially if a low (12 V) supply voltage is used. Increasing the time constant may result in unstable
switching.
nominal frequency of 26.5 kHz. A lower frequency will result in higher current ripple and may cause audible noise
from the motor, while increasing the frequency results in higher switching losses and possibly increased iron losses
in the motor.
current, reference voltage and the value of R
the maximum output current which is 650 mA per channel (or 500 mA per channel, both channels fully on, see
“Recommended Operating Conditions”).
Motor selection
The NJM3771 is designed for bipolar motors, i.e., motors that have only one winding per phase. A unipolar motor,
having windings with a center tap, can also be used, see figure 8.
scheme imposes certain restrictions on motor selection. Unstable chopping can occur if the chopping duty cycle
exceeds approximately 50%. To avoid this, it is necessary to choose a motor with a low winding resistance. Low
winding resistance means less inductance and will therefore enable higher stepping rates, however it also means
less torque capability. A compromise has to be made.
supply voltage as possible without exceeding the maximum recommended 40 V. Check that the chopping duty
cycle does not exceed 50% at maximum current.
at the same voltage as the actual supply voltage. Only rated current needs to be considered. Typical motors to be
used together with the NJM3771 have voltage ratings of 5 to 12 V, while the supply voltage usually ranges from 24
to 40 V.
Since the low-pass filtering action introduces a small delay of the signal to the comparator, peak voltage across
The time constant of the low-pass filter may therefore be reduced to minimize the delay and optimize low-current
The frequency of the clock oscillator is set by the R-C combination at pin RC. The recommended values give a
The sensing resistor, R
The chopping principle in the
Choose a motor with the lowest possible winding resistance that still gives the required torque and use as high
Since the NJM3771 produces a regulated, constant output current it is not necessary to use a motor that is rated
C
= 450 mV @V
R
Figure 8. Connection of unipolar motors
= 2.5 V).
S
, should be selected for maximum motor current. The relationship between peak motor
Best for high speed
NJM3771
NJM3771 is based on a constant frequency and a varying duty cycle. This
S
is described under “Current control” above. Be sure not to exceed
Best for high torque
NJM3771
NJM3771
C
, set