NJM3773D2 NJR, NJM3773D2 Datasheet - Page 8
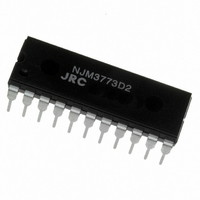
NJM3773D2
Manufacturer Part Number
NJM3773D2
Description
IC STEPPER MOTOR DVR DUAL 22-DIP
Manufacturer
NJR
Type
Stepper Motor Controller/Driverr
Datasheet
1.NJM3773D2.pdf
(9 pages)
Specifications of NJM3773D2
Applications
Stepper Motor Driver, 2 Phase
Number Of Outputs
1
Current - Output
750mA
Voltage - Load
10 V ~ 40 V
Voltage - Supply
4.75 V ~ 5.25 V
Operating Temperature
-20°C ~ 125°C
Mounting Type
Through Hole
Package / Case
22-DIP (0.400", 10.16mm)
Product
Stepper Motor Controllers / Drivers
Operating Supply Voltage
7 V
Supply Current
70 mA
Mounting Style
Through Hole
Lead Free Status / RoHS Status
Contains lead / RoHS non-compliant
Available stocks
Company
Part Number
Manufacturer
Quantity
Price
Company:
Part Number:
NJM3773D2
Manufacturer:
NJR
Quantity:
404
V
The comparator inputs of NJM3773 (V
gives a great deal of flexibility in selecting a suitable voltage divider network to interface to different types of Digital-
to-Analog converters. Unbuffered DACs are preferably interfaced by a high resistive divider network ( typ. 100
kohm), while for buffered DACs a low resistive network (typ. 5 kohm) is recommended. A filter capacitor in con-
junction with the resistor network will improve noise rejection. A typical filter time constant is 10 s. See figure 7. In
basic full and half-stepping applications, the reference voltage is easily divided from the V
Interference
Due to the switching operation of NJM3773, noise and transients are generated and coupled into adjacent circuitry.
To reduce potential interference there are a few basic rules to follow:
• Use separate ground leads for power ground (the ground connection of R
the ground of external analog and digital circuitry. The grounds should be connected together close to the GND
pins of NJM3773.
• Decouple the supply voltages close to the NJM3773 circuit. Use a ceramic capacitor in parallel with an electro-
lytic type for both V
• Do not place sensitive circuits close to the driver. Avoid physical current loops, and place the driver close to both
the motor and the power supply connector. The motor leads could preferably be twisted or shielded.
Motor selection
The NJM3773 is designed for two-phase bipolar stepper motors, i.e. motors that have only one winding per phase.
imposes certain restrictions on motor selection. Unstable chopping can occur if the chopping duty cycle exceeds
approximately 50%. See figure 5 for definitions. To avoid this, it is necessary to choose a motor with a low winding
resistance and inductance, i.e. windings with a few turns.
needs to be considered. Typical motors to be used together with the NJM3773 have a voltage rating of 1 to 6 V,
while the supply voltage usually ranges from 12 to 40 V.
give the same torque capability at low speed, the reduced number of turns in the winding in the low resistive, low
inductive motor must be compensated by a higher current. A compromise has to be made. Choose a motor with the
lowest possible winding resistance and inductance, that still gives the required torque, and use as high supply
voltage as possible, without exceeding the maximum recommended 40 V. Check that the chopping duty cycle does
not exceed 50% at maximum current.
Heat sinking
NJM3773 is a power IC, packaged in a power DIP, EMP or PLCC package. The ground leads of the package (the
batwing) are thermally connected to the chip. External heatsinking is achieved by soldering the ground leads onto a
copper ground plane on the PCB.
figures 8, 10 and 11 to determine the necessary heatsink, or to find the maximum output current under varying
conditions.
circuit to operate at 2 x 450 mA output current, at ambient temperatures up to 85 C.
Thermal shutdown
The circuit is equipped with a thermal shutdown function that turns the outputs off at a chip (junction) temperature
above 160 C. Normal operation is resumed when the temperature has decreased.
Programming
Figure 9 shows the different input and output sequences for full-step, half-step and modified halfstep operations.
Full-step mode.
Both windings are energized at all the time with the same current,
current direction (and the magnetic field direction) in one phase is reversed. The next step is then taken when the
other phase current reverses. The current changes go through a sequence of four different states which equal four
full steps until the initial state is reached again.
R
The chopping principle of the NJM3773 is based on a constant frequency and a varying duty cycle. This scheme
It is not possible to use a motor that is rated for the same voltage as the actual supply voltage. Only rated current
Low inductance, especially in combination with a high supply voltage, enables high stepping rates. However, to
Maximum continuous output current is heavily dependent on the heatsinking and ambient temperature. Consult
A copper area of 20 cm
(Reference) inputs
CC
and V
2
(approx. 1.8” x 1.8”), copper foil thickness 35 m on a 1.6 mm epoxy PCB, permits the
MM
Route the power supply lines close together.
R
and C) are high impedance, low current inputs (typically -0.2 A). This
I
M1
= I
M2
S
. To make the motor take one step, the
), the ground leads of NJM3773, and
CC
supply voltage.
NJM3773