HLMP-ED31-TVTDD Avago Technologies US Inc., HLMP-ED31-TVTDD Datasheet - Page 10
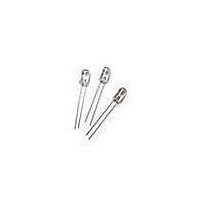
HLMP-ED31-TVTDD
Manufacturer Part Number
HLMP-ED31-TVTDD
Description
LED ROUND 5MM 630NM RED
Manufacturer
Avago Technologies US Inc.
Datasheet
1.HLMP-ED31-SV000.pdf
(13 pages)
Specifications of HLMP-ED31-TVTDD
Viewing Angle
30°
Package / Case
Radial - 2 Lead
Color
Red
Luminous Flux @ Current - Test
1 lm
Millicandela Rating
4000mcd
Current - Test
20mA
Wavelength - Dominant
630nm
Wavelength - Peak
639nm
Voltage - Forward (vf) Typ
2.4V
Lens Type
Clear
Lens Style/size
Round, 5mm, T-1 3/4
Height
8.71mm
Mounting Type
Through Hole
Resistance Tolerance
630nm
Led Size
T-1 3/4
Illumination Color
Red
Lens Color/style
Clear
Wavelength
630 nm
Mounting Style
Through Hole
Lead Free Status / RoHS Status
Lead free / RoHS Compliant
Available stocks
Company
Part Number
Manufacturer
Quantity
Price
Company:
Part Number:
HLMP-ED31-TVTDD
Manufacturer:
AVAGO
Quantity:
40 000
Precautions:
Lead Forming:
• The leads of an LED lamp may be preformed or cut to
• For better control, it is recommended to use proper
• If manual lead cutting is necessary, cut the leads after
Soldering and Handling:
• Care must be taken during PCB assembly and soldering
• LED component may be effectively hand soldered
• ESD precaution must be properly applied on the
• Recommended soldering condition:
Note:
1. Above conditions refers to measurement with thermocouple
2. It is recommended to use only bottom preheaters in order to reduce
• Wave soldering parameters must be set and
10
length prior to insertion and soldering on PC board.
tool to precisely form and cut the leads to applicable
length rather than doing it manually.
the soldering process. The solder connection forms
a mechanical ground which prevents mechanical
stress due to lead cutting from traveling into LED
package. This is highly recommended for hand solder
operation, as the excess lead length also acts as small
heat sink.
process to prevent damage to the LED component.
to PCB. However, it is only recommended under
unavoidable circumstances such as rework. The
closest manual soldering distance of the soldering
heat source (soldering iron’s tip) to the body is
1.59mm. Soldering the LED using soldering iron tip
closer than 1.59mm might damage the LED.
soldering station and personnel to prevent ESD
damage to the LED component that is ESD sensitive.
Do refer to Avago application note AN 1142 for details.
The soldering iron used should have grounded tip to
ensure electrostatic charge is properly grounded.
mounted at the bottom of PCB.
thermal stress experienced by LED.
maintained
temperature and dwell time. Customer is advised
to perform daily check on the soldering profile to
ensure that it is always conforming to recommended
soldering conditions.
Pre-heat temperature
Preheat time
Peak temperature
Dwell time
according
Wave
Soldering
105 °C Max.
60 sec Max
250 °C Max.
3 sec Max.
1.59mm
to
[1, 2]
the
recommended
Manual Solder
Dipping
-
-
260 °C Max.
5 sec Max
Note:
1. PCB with different size and design (component density) will have
2. Avago Technologies’ high brightness LED are using high efficiency
Avago Technologies LED configuration
• Any alignment fixture that is being applied during
• At elevated temperature, LED is more susceptible to
• If PCB board contains both through hole (TH) LED and
• Recommended PC board plated through holes (PTH)
• Over-sizing the PTH can lead to twisted LED after
different heat mass (heat capacity). This might cause a change in
temperature experienced by the board if same wave soldering
setting is used. So, it is recommended to re-calibrate the soldering
profile again before loading a new type of PCB.
LED die with single wire bond as shown below. Customer is advised
to take extra precaution during wave soldering to ensure that the
maximum wave temperature does not exceed 250°C and the solder
contact time does not exceeding 3sec. Over-stressing the LED
during soldering process might cause premature failure to the LED
due to delamination.
Note: Electrical connection between bottom surface of LED die and
the lead frame is achieved through conductive paste.
wave soldering should be loosely fitted and should
not apply weight or force on LED. Non metal material
is recommended as it will absorb less heat during
wave soldering process.
mechanical stress. Therefore, PCB must allowed to
cool down to room temperature prior to handling,
which includes removal of alignment fixture or pallet.
other surface mount components, it is recommended
that surface mount components be soldered on the
top side of the PCB. If surface mount need to be on the
bottom side, these components should be soldered
using reflow soldering prior to insertion the TH LED.
size for LED component leads.
clinching. On the other hand under sizing the PTH can
cause difficulty inserting the TH LED.
LED component
lead size
0.45 x 0.45 mm
(0.018x 0.018 inch)
0.50 x 0.50 mm
(0.020x 0.020 inch)
CATHODE
AllnGaP Device
Diagonal
0.636 mm
(0.025 inch)
0.707 mm
(0.028 inch)
Plated through
hole diameter
0.98 to 1.08 mm
(0.039 to 0.043 inch)
1.05 to 1.15 mm
(0.041 to 0.045 inch)