DM163029 Microchip Technology, DM163029 Datasheet - Page 42
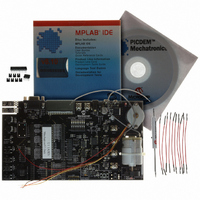
DM163029
Manufacturer Part Number
DM163029
Description
BOARD PICDEM FOR MECHATRONICS
Manufacturer
Microchip Technology
Specifications of DM163029
Main Purpose
Power Management, Motor Control
Embedded
*
Utilized Ic / Part
*
Primary Attributes
*
Secondary Attributes
*
Processor To Be Evaluated
PIC16F917
Interface Type
RS-232
Silicon Manufacturer
Microchip
Silicon Core Number
DM163029
Silicon Family Name
PICDEM
Kit Contents
PICDEM Mechatronics Board, MCU Samples, Software And Cables
Rohs Compliant
Yes
Lead Free Status / RoHS Status
Lead free / RoHS Compliant
Lead Free Status / RoHS Status
Lead free / RoHS Compliant, Lead free / RoHS Compliant
Available stocks
Company
Part Number
Manufacturer
Quantity
Price
Company:
Part Number:
DM163029
Manufacturer:
Microchip Technology
Quantity:
135
Company:
Part Number:
DM163029
Manufacturer:
MICROCHIP
Quantity:
12 000
PICDEM
DS51557C-page 38
TM
Instructions
Adjusting POT1 varies the speed of the motor. Toggle between single stepping, half
stepping, and microstepping modes by pressing SW2. At low speeds, the motor should
noticeably step in single stepping and half stepping modes. The movement will be quite
jerky in both modes, though to a lesser extent in the half stepping mode. In
microstepping mode, the jerky motion should be virtually eliminated.
Discussion
Stepper motors are used in many positioning applications. For example, ink jet printers
and smaller CNC machines employ stepper motors. Stepper motors are ideal for these
applications because, as long as they are not overloaded, the distance a stepper motor
moves is always known. Stepper motors are also brushless, which makes them more
reliable than brushed motors. Finally, stepper motors are very responsive to starting
and stopping and will produce the highest torque at low speeds.
Half stepping is used to give a stepping motor two times its rated step resolution.
However, there is a word of caution. A stepper motor is typically not rated to have more
than one winding energized at a time. As a result, the motor will heat up if both windings
are energized at the rated voltage of the motor. To offset this, when both windings are
energized simultaneously, the average current to each winding should be 0.707 times
the rated current.
Microstepping offers several advantages over single stepping and half stepping. First,
torque is fairly constant between steps. This results in smoother rotation and decreased
shaft oscillation. Secondly, a higher step resolution is achieved. This means a low-cost
motor can be used in an application that would normally require a more expensive,
higher resolution motor. Finally, the current in the motor windings is being controlled in
a way that prevents the motor from running outside its rated current, thereby eliminating
the excess heat associated with half stepping. The drawback to microstepping is that
the drive circuitry is more complex.
Mechatronics Demo Board User’s Guide
© 2006 Microchip Technology Inc.