MAX16010TAC+T Maxim Integrated Products, MAX16010TAC+T Datasheet - Page 8
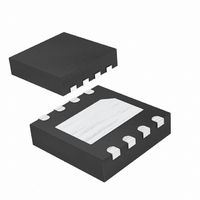
MAX16010TAC+T
Manufacturer Part Number
MAX16010TAC+T
Description
IC OVERVOLTAGE PROT/DETEC 8-TDFN
Manufacturer
Maxim Integrated Products
Type
Multi-Voltage Supervisorr
Datasheet
1.MAX16013TTT.pdf
(12 pages)
Specifications of MAX16010TAC+T
Number Of Voltages Monitored
2
Output
Open Drain or Open Collector
Reset
Active Low
Voltage - Threshold
Adjustable/Selectable
Operating Temperature
-40°C ~ 125°C
Mounting Type
Surface Mount
Package / Case
8-TDFN Exposed Pad
Undervoltage Threshold
1.215 V, 1.12 V
Overvoltage Threshold
1.18 V, 1.265 V
Output Type
Active Low, Open Drain
Manual Reset
Not Resettable
Watchdog
No Watchdog
Battery Backup Switching
No Backup
Supply Voltage (max)
72 V
Supply Voltage (min)
5.5 V
Supply Current (typ)
25 uA
Maximum Power Dissipation
1455 mW
Maximum Operating Temperature
+ 125 C
Mounting Style
SMD/SMT
Minimum Operating Temperature
- 40 C
Power Fail Detection
No
Lead Free Status / RoHS Status
Lead free / RoHS Compliant
For the MAX16011, drive EN low to force OUTA low,
OUTB low when LOGIC = low, and OUTB high when
LOGIC = high. When the device is enabled (EN = high)
the state of OUTA and OUTB depends on the INA+,
INB-, and LOGIC input (see Table 2).
For the MAX16013/MAX16014, drive EN low to pull
GATE2 to V
When the device is enabled (EN = high), GATE2 is
pulled to the greater of (V
the external MOSFET (P2).
Most automotive applications are powered by a multi-
cell, 12V lead-acid battery with a voltage between 9V
and 16V (depending on load current, charging status,
temperature, battery age, etc.). The battery voltage is
distributed throughout the automobile and is locally
regulated down to voltages required by the different
system modules. Load dump occurs when the alterna-
tor is charging the battery and the battery becomes
disconnected. Power in the alternator inductance flows
into the distributed power system and elevates the volt-
age seen at each module. The voltage spikes have rise
times typically greater than 5ms and decays within sev-
eral hundred milliseconds but can extend out to 1s or
more depending on the characteristics of the charging
system. These transients are capable of destroying
sensitive electronic equipment on the first fault event.
The MAX16013/MAX16014 provide the ability to dis-
connect the load from the charging system during an
overvoltage condition to protect the module. In addi-
tion, the MAX16013 can be configured in a voltage-lim-
iting mode. This allows continuous operation while
providing overvoltage protection. See the Overvoltage
Limiter section.
Ultra-Small, Overvoltage Protection/
Detection Circuits
Table 2. MAX16011 Output Logic
8
LOGIC
High
High
Low
Low
_______________________________________________________________________________________
> V
> V
< V
< V
CC
INA+
TH+
TH+
, turning off the p-channel MOSFET (P2).
TH-
TH-
Applications Information
> V
> V
< V
< V
INB-
TH+
TH+
TH-
TH-
CC
- 10V) or GND turning on
Impedance
Impedance
OUTA
High
High
Low
Low
Load Dump
Impedance
Impedance
OUTB
High
High
Low
Low
When the external MOSFET is turned off during an
overvoltage occurrence, stray inductance in the power
path may cause voltage ringing to exceed the
MAX16013/MAX16014 absolute maximum input (V
supply rating. The following techniques are recom-
mended to reduce the effect of transients:
•
•
When operating in overvoltage-limiter mode, the
MAX16013 drives the external p-channel MOSFET (P2),
resulting in the external MOSFET operating as a voltage
regulator.
During normal operation, GATE2 is pulled to the greater
of (V
voltage is monitored through a resistor-divider between
the P2 output and SET. When the output voltage rises
above the adjusted overvoltage threshold, an internal
comparator pulls GATE2 to V
voltage goes below the overvoltage threshold, the
p-channel MOSFET (P2) is turned on again. This
process continues to keep the voltage at the output reg-
ulated to within approximately a 5% window. The output
voltage is regulated during the overvoltage transients
and the MOSFET (P2) continues to conduct during the
overvoltage event, operating in switched-linear mode.
Caution must be exercised when operating the
MAX16013 in voltage-limiting mode for long durations
due to the MOSFET’s power dissipation consideration
(see the MOSFET Selection and Operation section).
Most battery-powered applications must include reverse
voltage protection. Many times this is implemented with a
diode in series with the battery. The disadvantage in
using a diode is the forward voltage drop of the diode,
which reduces the operating voltage available to down-
stream circuits (V
MAX16013 and MAX16014 include high-voltage GATE1
drive circuitry allowing users to replace the high-voltage-
drop series diode with a low-voltage-drop MOSFET
device (as shown in the Typical Operating Circuit and
Figure 3). The forward voltage drop is reduced to I
x R
voltage drop can be reduced to millivolts.
DS-ON
CC
Minimize stray inductance in the power path using
wide traces, and minimize loop area including the
power traces and the return ground path.
Add a zener diode or transient voltage suppresser
(TVS) rated below V
(Figure 3).
- 10V) or GND. The external MOSFET’s drain
of P1. With a suitably chosen MOSFET, the
MOSFET Selection and Operation
LOAD
(MAX16013 and MAX16014)
Input Transients Clamping
= V
CC
absolute maximum rating
BATTERY
Overvoltage Limiter
CC
. When the monitored
- V
DIODE
). The
LOAD
CC
)