MAX5419LETA+T Maxim Integrated Products, MAX5419LETA+T Datasheet - Page 8
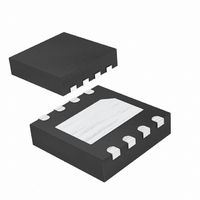
MAX5419LETA+T
Manufacturer Part Number
MAX5419LETA+T
Description
IC POT DGTL 256-TAP I2C 8-TDFN
Manufacturer
Maxim Integrated Products
Specifications of MAX5419LETA+T
Package / Case
8-TDFN Exposed Pad
Mounting Type
Surface Mount
Voltage - Supply
2.7 V ~ 5.25 V
Operating Temperature
-40°C ~ 85°C
Temperature Coefficient
35 ppm/°C Typical
Interface
I²C, 2-Wire Serial
Resistance In Ohms
200K
Number Of Circuits
1
Memory Type
Non-Volatile
Taps
256
Lead Free Status / RoHS Status
Lead free / RoHS Compliant
The MAX5417/MAX5418/MAX5419 consist of a resistor
array with 255 resistive elements; 256 tap points are
accessible to the wiper, W, along the resistor string
between H and L. The wiper tap point is selected by
programming the potentiometer through the 2-wire (I
interface. Eight data bits, an address byte, and a con-
trol byte program the wiper position. The H and L termi-
nals of the MAX5417/MAX5418/MAX5419 are similar to
the two end terminals of a mechanical potentiometer.
The MAX5417/MAX5418/MAX5419 feature power-on
reset circuitry that loads the wiper position from non-
volatile memory at power-up.
The MAX5417/MAX5418/MAX5419 feature an internal,
nonvolatile EEPROM that stores the wiper state for ini-
tialization during power-up. The shift register decodes
the control and address bits, routing the data to the
proper memory registers. Data can be written to a
volatile memory register, immediately updating the
wiper position, or data can be written to a nonvolatile
register for storage.
The volatile register retains data as long as the device
is powered. Once power is removed, the volatile regis-
ter is cleared. The nonvolatile register retains data even
after power is removed. Upon power-up, the power-on
reset circuitry controls the transfer of data from the non-
volatile register to the volatile register.
256-Tap, Nonvolatile, I
Digital Potentiometers
Figure 3. Start and Stop Conditions
Figure 4. Slave Address
SMBus is a trademark of Intel Corporation.
8
SDA
SCL
SDA
SCL
CONDITION
_______________________________________________________________________________________
START
S
MSB
0
1
Digital Interface
Analog Circuitry
1
1
CONDITION
STOP
P
2
C)
2
C-Interface,
0
The MAX5417/MAX5418/MAX5419 operate as a slave
that receives data through an I
patible 2-wire interface. The interface uses a serial data
access (SDA) line and a serial clock line (SCL) to
achieve communication between master(s) and
slave(s). A master, typically a microcontroller, initiates
all data transfers to the MAX5417/MAX5418/MAX5419,
and generates the SCL clock that synchronizes the
data transfer (Figure 1).
The MAX5417/MAX5418/MAX5419 SDA line operates
as both an input and an open-drain output. A pullup
resistor, typically 4.7kΩ, is required on the SDA bus.
The MAX5417/MAX5418/MAX5419 SCL operates only
as an input. A pullup resistor, typically 4.7kΩ, is
required on the SCL bus if there are multiple masters
on the 2-wire interface, or if the master in a single-mas-
ter system has an open-drain SCL output.
Each transmission consists of a START (S) condition
(Figure 3) sent by a master, followed by the
MAX5417/MAX5418/MAX5419 7-bit slave address plus
the 8th bit (Figure 4), 1 command byte (Figure 7) and 1
data byte, and finally a STOP (P) condition (Figure 3).
Both SCL and SDA remain high when the interface is
not busy. A master signals the beginning of a transmis-
sion with a START condition by transitioning SDA from
high to low while SCL is high. When the master has fin-
ished communicating with the slave, it issues a STOP
condition by transitioning the SDA from low to high
while SCL is high. The bus is then free for another
transmission (Figure 3).
One data bit is transferred during each clock pulse.
The data on the SDA line must remain stable while SCL
is high (Figure 5).
0
LSB
A0
Start and Stop Conditions
2
R/W
C- and SMBus™-com-
Serial Addressing
Bit Transfer
ACK