AD648JR Analog Devices Inc, AD648JR Datasheet - Page 7
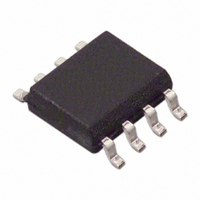
AD648JR
Manufacturer Part Number
AD648JR
Description
IC OPAMP BIFET 1MHZ DUAL 8SOIC
Manufacturer
Analog Devices Inc
Datasheet
1.AD648JRZ.pdf
(12 pages)
Specifications of AD648JR
Mounting Type
Surface Mount
Rohs Status
RoHS non-compliant
Amplifier Type
J-FET
Number Of Circuits
2
Slew Rate
1.8 V/µs
Gain Bandwidth Product
1MHz
Current - Input Bias
5pA
Voltage - Input Offset
750µV
Current - Supply
340µA
Current - Output / Channel
15mA
Voltage - Supply, Single/dual (±)
±4.5 V ~ 18 V
Operating Temperature
0°C ~ 70°C
Package / Case
8-SOIC (3.9mm Width)
No. Of Amplifiers
2
Bandwidth
1MHz
No. Of Pins
8
Peak Reflow Compatible (260 C)
No
Input Bias Current
20pA
Input Offset Voltage Max
2mV
Common Mode Ratio
76
Output Type
-
-3db Bandwidth
-
Lead Free Status / RoHS Status
Contains lead / RoHS non-compliant
Available stocks
Company
Part Number
Manufacturer
Quantity
Price
Company:
Part Number:
AD648JR
Manufacturer:
ADI
Quantity:
4 130
Part Number:
AD648JR
Manufacturer:
ADI/亚德诺
Quantity:
20 000
Part Number:
AD648JRZ
Manufacturer:
ADI/亚德诺
Quantity:
20 000
APPLICATION NOTES
The AD648 is a pair of JFET-input op amps with a guaranteed
maximum I
trimmed to 1.0 mV and 10 µV/°C, respectively (AD648B). AC
specs include 1 MHz bandwidth, 1.8 V/µs typical slew rate and
8 µs settling time for a 20 V step to ± 0.01%—all at a supply
current less than 400 µA. To capitalize on the device’s perfor-
mance, a number of error sources should be considered.
The minimal power drain and low offset drift of the AD648
reduce self-heating or “warm-up” effects on input offset voltage,
making the AD648 ideal for on/off battery powered applica-
tions. The power dissipation due to the AD648’s 400 µA supply
current has a negligible effect on input current, but heavy out-
put loading will raise the chip temperature. Since a JFET’s
input current doubles for every 10°C rise in chip temperature,
this can be a noticeable effect.
The amplifier is designed to be functional with power supply
voltages as low as ± 4.5 V. It will exhibit a higher input offset
voltage than at the rated supply voltage of ± 15 V, due to power
supply rejection effects. Common-mode range extends from 3 V
more positive than the negative supply to 1 V more negative
than the positive supply. Designed to cleanly drive up to 10 kΩ
and 100 pF loads, the AD648 will drive a 2 kΩ load with reduced
open-loop gain.
Figure 21 shows the recommended crosstalk test circuit. A
typical value for crosstalk is –120 dB at 1 kHz.
LAYOUT
To take full advantage of the AD648’s 10 pA max input current,
parasitic leakages must be kept below an acceptable level. The
practical limit of the resistance of epoxy or phenolic circuit
board material is between 1 × 10
result in an additional leakage of 5 pA between an input of 0 V
and a –15 V supply line. Teflon or a similar low leakage material
(with a resistance exceeding 10
high impedance input lines from adjacent lines carrying high
voltages. The insulator should be kept clean, since contaminants
will degrade the surface resistance.
A metal guard completely surrounding the high impedance
nodes and driven by a voltage near the common-mode input
potential can also be used to reduce some parasitic leakages.
The guarding pattern in Figure 22 will reduce parasitic leakage
due to finite board surface resistance; but it will not compensate
for a low volume resistivity board.
REV. E
B
of less than 10 pA, and offset and drift laser-
Figure 21. Crosstalk Test Circuit
17
12
Ω) should be used to isolate
Ω and 3 × 10
12
Ω. This can
–7–
INPUT PROTECTION
The AD648 is guaranteed to withstand input voltages equal to
the power supply potential. Exceeding the negative supply volt-
age on either input will forward bias the substrate junction of
the chip. The induced current may destroy the amplifier due to
excess heat.
Input protection is required in applications such as a flame
detector in a gas chromatograph, where a very high potential
may be applied to the input terminals during a sensor fault
condition. Figures 23a and 23b show simple current limiting
schemes that can be used. R
the maximum overload current is 1.0 mA (for example 100 kΩ
for a 100 V overload).
Figure 23b shows the recommended method for protecting a
voltage follower from excessive currents due to high voltage
breakdown. The protection resistor, R
A nominal value of 100 kΩ will limit the input current to less
than 1 mA with a 100 volt input voltage applied.
The stray capacitance between the summing junction and
ground will produce a high-frequency roll-off with a corner
frequency equal to:
Accordingly, a 100 kΩ value for R
a 3 dB corner frequency to occur at 531 kHz.
Figure 23b. Voltage Follower Input Protection Method
Figure 23a. Input Protection of l-to-V Converter
Figure 22. Board Layout for Guarding Inputs
f
corner
PROTECT
=
2 π R
P
with a 3 pF C
1
P
should be chosen such that
C
P
, limits the input current.
stray
stray
AD648
will cause