QSH4218-41-10-035 TRINAMIC, QSH4218-41-10-035 Datasheet - Page 12
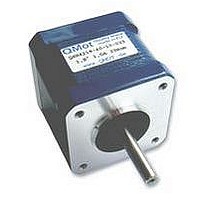
QSH4218-41-10-035
Manufacturer Part Number
QSH4218-41-10-035
Description
STEPPER MOTOR, 1.8DEG, 1A, 0.35NM
Manufacturer
TRINAMIC
Datasheet
1.QSH4218-35-10-027.pdf
(13 pages)
Specifications of QSH4218-41-10-035
Torque Max
10N-m
No. Of Phases
2
Inductance
7.5mH
Inertia
35g-cm2
Current Per Phase
1A
External Depth
42mm
External Length / Height
39.4mm
External Width
42mm
Holding
RoHS Compliant
Coil Type
Bipolar
Svhc
No SVHC (15-Dec-2010)
Rohs Compliant
Yes
QSH4218 Manual (V1.05/2009-JUN-20)
6.5
While the motor performance curves are depicted for fullstepping and halfstepping, most modern
drivers provide a microstepping scheme. Microstepping uses a discrete sine and a cosine wave to
drive both coils of the motor, and gives a very smooth motor behavior as well as an increased
position resolution. The amplitude of the waves is 1.41 times the nominal motor current, while the
RMS values equal the nominal motor current. The stepper motor does not make loud steps any more
– it turns smoothly! Therefore, 16 microsteps or more are recommended for a smooth operation and
the avoidance of resonances. To operate the motor at fullstepping, some considerations should be
taken into account.
Driver Scheme Resolution
Fullstepping
Halfstepping
Microstepping
Mixed: Micro-
stepping and
fullstepping for
high velocities
Microstepping gives the best performance for most applications and can be considered as state-of-the
art. However, fullstepping allows some ten percent higher motor velocities, when compared to
microstepping. A combination of microstepping at low and medium velocities and fullstepping at
high velocities gives best performance at all velocities and is most universal. Most Trinamic driver
modules support all three modes.
6.5.1
When operating the motor in fullstep, resonances may occur. The resonance frequencies depend on
the motor load. When the motor gets into a resonance area, it even might not turn anymore! Thus
you should avoid resonance frequencies.
6.5.1.1 Avoiding motor resonance in fullstep operation
A resonance dampener might be required, if the resonance frequencies cannot be skipped
Copyright © 2008, TRINAMIC Motion Control GmbH & Co. KG
Do not operate the motor at resonance velocities for extended periods of time. Use a reasonably
high acceleration in order to accelerate to a resonance-free velocity. This avoids the build-up of
resonances. When resonances occur at very high velocities, try reducing the current setting.
Choosing the Commutation Scheme
Fullstepping
200 steps per
rotation
200 steps per
rotation * 2
200 * (number of
microsteps) per
rotation
200 * (number of
microsteps) per
rotation
Table 6.3: Comparing microstepping and fullstepping
Velocity range
Low to very high.
Skip resonance
areas in low to
medium velocity
range.
Low to very high.
Skip resonance
areas in low to me-
dium velocity
range.
Low to high.
Low to very high.
Torque
Full torque if dam-
pener used,
otherwise reduced
torque in resonance
area
Full torque if dam-
pener used,
otherwise reduced
torque in resonance
area
Reduced torque at
very high velocity
Full torque
Comments
Audible noise
especially at low
velocities
Audible noise
especially at low
velocities
Low noise, smooth
motor behavior
At high velocities,
there is no audible
difference for full-
stepping
12