ADNS-7700-H4MY Avago Technologies US Inc., ADNS-7700-H4MY Datasheet - Page 9
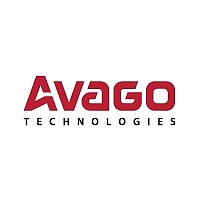
ADNS-7700-H4MY
Manufacturer Part Number
ADNS-7700-H4MY
Description
USB SoC Lsr Snsr 3B+TW
Manufacturer
Avago Technologies US Inc.
Datasheet
1.ADNS-7700-H4MY.pdf
(60 pages)
Specifications of ADNS-7700-H4MY
Lead Free Status / RoHS Status
Contains lead / RoHS non-compliant
Lead Free Status / RoHS Status
Contains lead / RoHS non-compliant
Available stocks
Company
Part Number
Manufacturer
Quantity
Price
Company:
Part Number:
ADNS-7700-H4MY
Manufacturer:
VISHAY
Quantity:
40 000
Part Number:
ADNS-7700-H4MY
Manufacturer:
AVAGO/安华高
Quantity:
20 000
PCB Layout Considerations:
1. The DGND and AGND paths MUST be layout as far as
2. All caps MUST be as close to VDD5, REFA, REFB & +VCSEL
3. 1.5k: pullup resistor (R1) should be ± 1% tolerance
4. Ceramic non-polarity caps and tantalum polarity caps
5. Caps should have less than 5nH of self inductance.
6. Caps connected to VDD5 MUST have less than 0.2: ESR.
7. REFC pin requires an open ended trace of min 50 mm
8. Do not use jumper on ground plane, D+ and D- paths.
9. Data lines (D+ and D-) should be as far as possible from
PCB Assembly Considerations
1. Insert the sensor package and all other electrical
2. Wave solder the entire assembly in a non-wash solder
3. Place the lens onto the base plate. Care must be taken
4. Hold the PCB vertically and remove the Kapton tape
5. Place the PCB over the lens onto base plate. The sensor
9
possible and connected together at the USB ground
point with star topology. Ensure large grounding plane
on the PCB layout for better performance on ESD and
EFTB.
sensor pins as possible and ground at the DGND and
AGND plane that connected to USB GND, with trace
length less than 5mm.
and connected to REFB pin with shortest possible trace
length.
are recommended.
lengths within DGND plane for EFTB performance im-
provement. Refer to System Design Recommendations
Application Note.
resonator.
components into the application PCB. To maintain the
Z alignment of sensor package, the sensor reference
plane can be sit directly on the PCB.
process utilizing solder fixture. The solder fixture is
needed to protect the sensor during the solder process
shielding the optical aperture from direct solder
contact.
to avoid contamination and scratches on the optical
surfaces.
attached to the respective aperture of sensor and
VCSEL. During the removal process of Kapton tape, care
must be taken to prevent contaminants from entering
through the apertures. Do NOT place the PCB facing
upwards during the entire mouse assembly process.
package should be self-aligned and locked to the lens
by the lens’ alignment guide posts. The optical center
reference for the PCB is set by base plate and lens. Note
that the PCB movement due to button presses must be
minimized to maintain good optical alignment.
6. Optional: The lens can be permanently locked to the
7. Then, install the mouse top case. There MUST be feature
Design Considerations for Improving ESD Performance
For improved electrostatic discharge performance, typical
creepage and clearance distance are shown in the table
below. Assumption: base plate construction as per the
Avago supplied 3D model file when use with ADNS-6180-
001 trim lens or ADNS-6180-002 wide trim lens. The lens
flange can be sealed (i.e. glued) to the base plate. Note
that the lens material is polycarbonate and therefore, cya-
noacrylate based adhesives or other adhesives that may
damage the lens should NOT be used.
Regulatory Requirements
x Passes FCC B and worldwide analogous emission limits
x Passes EN 61000-4-4/IEC 801-4 EFT tests when
x Passes IEC-61000-4-2 Electrostatic Discharge Immunity
x Passes IEC/EN 60825-1 Class-1 Eye Safety when ADNS-
Typical Distance
(mm)
Creepage
Clearance
sensor package by melting the lens’ guide posts over
the sensor with heat staking process.
in the top case (or other area) to press down onto the
sensor or PCB assembly to ensure the sensor and lens
are interlocked to correct vertical height.
when assembled into a mouse with unshielded cable
and following Avago Technologies recommendations.
assembled into a mouse with shielded cable and
following Avago Technologies recommendations.
Test (ESD) and provides sufficient ESD creepage/
clearance distance to withstand up to 12 kV discharge
when assembled into a mouse with ADNS-6180-001
trim lens and up to 15 kV discharge when assembled
into a mouse with ADNS-6180-002 wide trim lens.
7700 is driving the laser using ADNS-6180-001 or
ADNS-6180-002 lens with recommended operating
conditions.
ADNS-6180-001
trim lens
5.5
1.8
ADNS-6180-002
wide trim lens
17.5
1.8