XW2Z-100J-A27 Omron, XW2Z-100J-A27 Datasheet - Page 11
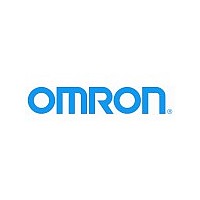
XW2Z-100J-A27
Manufacturer Part Number
XW2Z-100J-A27
Description
SERVO RELAY UNIT CABLES 1M
Manufacturer
Omron
Datasheet
1.XW2Z-100J-A27.pdf
(30 pages)
Specifications of XW2Z-100J-A27
Lead Free Status / Rohs Status
Lead free / RoHS Compliant
Other names
XW2Z100JA27
*14.Supported only by the CJ2M-CPU3@.
Function Blocks
Debugging
Self-
diagnosis
and
Restoration
Languages in Function Block Definitions
Online Editing
Force-Set/Reset
Differentiate Monitoring
Data Tracing
Storing Location of Error when an Error Occurs
Program Check
Error Log
CPU Error Detection
User-defined Failure Diagnosis
Load OFF Function
RUN Output
Basic I/O Load Short-circuit Detection
Failure Point Detection
CPU Standby Detection
Non-fatal Error
Detection
Fatal Error
Detection
Continuous Tracing
Automatically starting tracing when operation
starts
Function
System FAL Error Detection
(User-defined non-fatal error)
Duplicate Refreshing Error
Detection
Basic I/O Unit Error Detection This function detects the errors in Basic I/O Units.
Backup Memory Error
Detection
PLC Setup Error Detection
CPU Bus Unit Error Detection
Special I/O Unit Error
Detection
Tag Memory Error Detection *13
Battery Error Detection
CPU Bus Unit Setting Error
Detection
Special I/O Unit Setting Error
Detection
Option Board Error Detection *13 This function detects the errors in Serial Option Board mounting status.
Memory Error Detection
I/O Bus Error Detection
Unit/Rack Number
Duplication Error
Too Many I/O Points Error
Detection
I/O Setting Error Detection
Standard programming can be encapsulated as function blocks.
Ladder programming or structured text
The program can be changed during operation (in MONITOR or PROGRAM mode), except for
block programming areas.
Specified bits can be set or reset.
Force-set/reset to the EM Area is enabled by specifying a start bank in parameter setting.
ON/OFF changes in specified bits can be monitored.
The specified I/O memory data can be stored in the trace memory in the CPU Unit. The
triggers can be set.
The trace data can be uploaded during data tracing using CX-Programmer, which enables
continuously logging the data by constantly uploading the trace data.
Data tracing can be automatically started when operation is started (i.e., when the operating
mode is changed from PROGRAM mode to MONITOR or RUN mode).
The location and task number where execution stopped for a program error is recorded.
The programs can be checked for items such as no END instruction and FALS/FAL errors at
startup.
A function is provided to store predefined error codes in CPU Unit, error information, and time
at which the error occurred.
CPU Unit WDT errors are detected.
Errors can be generated for user-specified conditions: Non-fatal errors (FAL) and fatal errors
(FALS).
Program section time diagnosis and program section logic diagnosis are supported (FPD
instruction).
This function turns OFF all outputs from Output Units when an error occurs.
The RUN output from the CJ1W-PA205R turns ON while CPU Unit is in RUN mode or
MONITOR mode.
This function provides alarm information from Basic I/O Units that have load short-circuit
protection.
The time and logic of an instruction block can be analyzes using the FPD instruction.
This function indicates when the CPU Unit is on standby because all Special I/O Units and
CPU Bus Units have not been recognized at the startup in RUN or MONITOR mode.
This function generates a non-fatal (FAL) error when the user-defined conditions are met in
program.
This function detects an error when an immediate refreshing Instruction in an interrupt task is
competing with I/O refreshing of a cyclic task.
This function detects errors in the memory backup of the user programs and parameter area
(backup memory).
This function detects setting errors in the PLC Setup.
This function detects an error when there is an error in data exchange between the CPU Unit
and a CPU Bus Unit.
This function detects an error when there is an error in data exchange between the CPU Unit
and a Special I/O Unit.
This function detects errors in tag memory.
This function detects an error when a battery is not connected to the CPU Unit or when the
battery voltage drops.
This function detects an error when the model of a CPU Bus Unit in the registered I/O tables
does not agree with the model that is actually mounted in the PLC.
This function detects an error when the model of a Special I/O Unit in the registered I/O tables
does not agree with the model of Unit that is actually mounted.
This function detects errors that occur in memory of the CPU Unit.
This function detects when an error occurs in data transfers between the Units mounted in
Rack slots and the CPU Unit and detects when the End Cover is not connected to the CPU
Rack or an Expansion Rack.
This function detects an error when the same unit number is set for two or more Units, the
same word is allocated to two or more Basic I/O Units, or the same rack number is set for two
or more Racks.
This function detects an error when the total number of I/O points set in the I/O tables or the
number of Units per Rack exceeds the specified range.
This function detects an error when the number of Units in the registered I/O tables does not
agree with the actual number of Units that is mounted, or an Interrupt Unit has been connected
in the wrong position, i.e., not in slot 0 to 4.
CJ2M-CPU3@/-CPU1@/-MD21@
Description
11