LT1107 Linear Technology, LT1107 Datasheet - Page 7
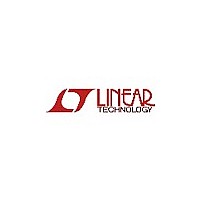
LT1107
Manufacturer Part Number
LT1107
Description
Micropower DC/DC Converter Adjustable and Fixed 5V/ 12V
Manufacturer
Linear Technology
Datasheet
1.LT1107.pdf
(12 pages)
Available stocks
Company
Part Number
Manufacturer
Quantity
Price
Part Number:
LT1107-15-AE3-3-R
Manufacturer:
UTC/友顺
Quantity:
20 000
Part Number:
LT1107-15-AF5-3-R
Manufacturer:
UTC/友顺
Quantity:
20 000
Part Number:
LT1107-18-AE3-3-R
Manufacturer:
UTC/友顺
Quantity:
20 000
Part Number:
LT1107-18-AF5-3-R
Manufacturer:
UTC/友顺
Quantity:
20 000
Part Number:
LT1107-25-AE3-3-R
Manufacturer:
UTC/友顺
Quantity:
20 000
Company:
Part Number:
LT1107CN8-12
Manufacturer:
LT
Quantity:
5 510
Company:
Part Number:
LT1107CN8-12
Manufacturer:
AD
Quantity:
5 510
Company:
Part Number:
LT1107CN8/CN8-12
Manufacturer:
LT
Quantity:
5 510
can be used. These equations assume that at t = 0,
inductor current is zero. This situation is called “discon-
tinuous mode operation” in switching regulator parlance.
Setting “t” to the switch ON time from the LT1107 speci-
fication table (typically 11 s) will yield I
“L” and V
at the end of the switch ON time can be calculated as:
E
the required power. For best efficiency I
kept to 1A or less. Higher switch currents will cause
excessive drop across the switch resulting in reduced
efficiency. In general, switch current should be held to as
low a value as possible in order to keep switch, diode and
inductor losses at a minimum.
Inductor Selection –– Step-Up Converter
In a step-up, or boost converter (Figure 1), power gener-
ated by the inductor makes up the difference between
input and output. Power required from the inductor is
determined by:
where V
Energy required by the inductor per cycle must be equal or
greater than:
in order for the converter to regulate the output.
When the switch is closed, current in the inductor builds
according to:
where R is the sum of the switch equivalent resistance
(0.8
When the drop across the switch is small compared to V
the simple lossless equation:
A
L
PPLICATI
must be greater than P
I
E
P
P f
I t
L
L
L
L
L OSC
t
typical at 25 C) and the inductor DC resistance.
D
2
1
V
IN
is the diode drop (0.5V for a 1N5818 Schottky).
LI
OUT
V
V
R
. Once I
L
IN
IN
PEAK
2
t
1
O
V
PEAK
e
D
U
R t
L
S
V
is known, energy in the inductor
IN MIN
L
/f
I FOR ATIO
OSC
U
for the converter to deliver
I
OUT
W
PEAK
PEAK
for a specific
should be
U
02
03
05
04
01
IN
,
As an example, suppose 12V at 60mA is to be generated
from a 3V to 6V input. Recalling equation (01),
Energy required from the inductor is:
Picking an inductor value of 33 H with 0.2 DCR results
in a peak switch current of:
Substituting I
Since 11.9 J > 9.05 J, the 33 H inductor will work. This
trial-and-error approach can be used to select the opti-
mum inductor.
A resistor can be added in series with the I
switch current limit. The resistor should be picked so the
calculated I
Switch Current (from Typical Performance Characteristic
curves). Then, as V
held constant, resulting in increasing efficiency.
Inductor Selection –– Step-Down Converter
The step-down case (Figure 2) differs from the step-up in
that the inductor current flows through the load during
both the charge and discharge periods of the inductor.
Current through the switch should be limited to ~650mA
in this mode. Higher current can be obtained by using an
external switch (see LT1111 and LT1110 data sheets). The
I
inputs.
After establishing output voltage, output current and input
voltage range, peak switch current can be calculated by the
formula:
LIM
P
I
E
I
f
PEAK
OSC
PEAK
P
L
L
pin is the key to successful operation over varying
L
2
1
12
570
1
PEAK
3
33
2
63
V
V
I
DC
PEAK
OUT
kHz
mW
H
0 5
at minimum V
1
into Equation 04 results in:
V
0 85
e
V
IN
IN
9 05
1
V
increases, peak switch current is
33
3
A
OUT
V
11
V
H
2
SW
60
J
s
IN
mA
11 91
V
is equal to the Maximum
D
V
850
D
570
J
mA
LIM
mW
pin to invoke
LT1107
7
07
06
08
09
10