LTC1700 Linear Technology, LTC1700 Datasheet - Page 10
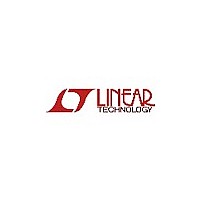
LTC1700
Manufacturer Part Number
LTC1700
Description
No RSENSE Synchronous Step-Up DC/DC Controller
Manufacturer
Linear Technology
Datasheet
1.LTC1700.pdf
(16 pages)
Available stocks
Company
Part Number
Manufacturer
Quantity
Price
Company:
Part Number:
LTC1700EMS
Manufacturer:
LT
Quantity:
10 000
Part Number:
LTC1700EMS
Manufacturer:
LINEAR/凌特
Quantity:
20 000
Part Number:
LTC1700EMS#PBF
Manufacturer:
LT凌特厂
Quantity:
20 000
LTC1700
APPLICATIONS
To eliminate this subharmonic oscillations, a compensat-
ing ramp is added internally to the LTC1700 on the
inductor current waveform when the duty cycle exceeds
5%. This scheme, known as slope compensation, makes
the loop perceive that there is more inductor current than
it actually has. As a result, the maximum current capability
of the regulator is reduced. This reduction is proportional
to the duty cycle and is shown in Figure 5. Hence for
applications that operate at high duty cycles, the
N-channel MOSFET chosen should have a lower R
to make up for this reduction (See Design Example).
Inductor Value Selection
Given the input voltage, inductor value and operating
frequency, the ripple current can be calculated:
Lower ripple current reduces core losses in the inductor,
ESR losses in the output capacitors and output voltage
ripple. Thus, highest efficiency operation is obtained at
low frequency with small ripple current. To achieve this,
however, requires a larger inductor.
A reasonable starting point is to choose a ripple current
that is about 40% of I
current occurs at the highest V
current does not exceed a specified maximum, the induc-
tor should be chosen according to:
10
I
L
Figure 5. Maximum Output Current vs Duty Cycle
V
IN
1.2
1.0
0.8
0.6
0.4
0.2
DC
0
fL
0
10
U
O(MAX)
20
INFORMATION
DUTY CYCLE (%)
U
30
. Note that the largest ripple
IN
40
. To guarantee that ripple
W
50
60
1700 F05
70
U
DS(ON)
With Burst Mode operation enabled on the LTC1700, the
ripple current is normally set such that the inductor
current is continuous during burst periods. Remember
that during bursting, the peak current is clamped at
approximately:
Hence the peak-to-peak ripple selected for optimal burst
mode operation should not exceed I
implies a minimum inductance of:
In applications that invoke Burst Mode operation, the
inductor should be chosen so it has low ripple (0.4I
current during heavy load and continuous operation dur-
ing bursting. The criteria for selecting which equation to
use is:
A smaller value than L
however, the inductor current will not be continuous
during burst periods. The advantage of using a smaller
inductance than L
higher output ripple.
Inductor Core Selection
Once the value for L is known, the type of inductor must be
selected. High efficiency converters generally cannot af-
ford the core loss found in low cost powdered iron cores,
forcing the use of more expensive ferrite, molypermalloy,
or Kool M
size for a fixed inductor value, but it is very dependent on
inductance selected. As inductance increases, core losses
go down. Unfortunately, increased inductance requires
more turns of wire and therefore copper losses will
Kool M is a registered trademark of Magnetics, Inc.
I
Use L
Use L
L
L
BURST(PEAK)
MIN
MINBURST
MIN
MINBURST
V
®
IN MAX
for Duty Cycle > 36%
cores. Actual core loss is independent of core
(
MIN
( )( . )
36mV/R
)
f
for Duty Cycle 36%
V
f I
0 66
IN MAX
DC
is primarily size. The disadvantage is
(
MIN
L
DS(ON)
)
1
could be used in the circuit;
I
OMAX
–
DC
DC
BURST(PEAK)
. This
OMAX
)