MAX17075ETG+ Maxim Integrated Products, MAX17075ETG+ Datasheet - Page 18
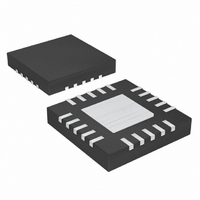
MAX17075ETG+
Manufacturer Part Number
MAX17075ETG+
Description
IC DC-DC CONV W/CHRG PUMP 24TQFN
Manufacturer
Maxim Integrated Products
Datasheet
1.MAX17075ETG.pdf
(22 pages)
Specifications of MAX17075ETG+
Applications
LCD TV/Monitor
Current - Supply
4mA
Voltage - Supply
2.3 V ~ 5.5 V
Operating Temperature
-40°C ~ 85°C
Mounting Type
Surface Mount
Package / Case
24-TQFN Exposed Pad
Lead Free Status / RoHS Status
Lead free / RoHS Compliant
Boost Regulator with Integrated Charge Pumps,
Switch Control, and High-Current Op Amp
Thermal-overload protection prevents excessive power
dissipation from overheating the MAX17075. When the
junction temperature exceeds +160°C, a thermal sen-
sor immediately activates the fault protection, which
shuts down all outputs except the reference, allowing
the device to cool down. Once the device cools down
by approximately 15°C, cycle the input voltage (below
the UVLO falling threshold) to clear the fault latch and
reactivate the device.
The thermal-overload protection protects the controller
in the event of fault conditions. For continuous opera-
tion, do not exceed the absolute maximum junction
temperature rating of +150°C.
Based upon the input at the RSTIN and VCC pins, the
XAO controller either pulls the reset pin RST low or sets
it to high impedance. RST is an open-drain output. Pull
it high to system 3.3V through a 10kΩ resistor. Connect
RSTIN to V
(Figure 1) to set the proper XAO threshold.
Once V
controller initiates a 220ms blanking period during
which the drop on V
high impedance. After this blanking period and if RSTIN
goes below approximately 1.25V, RST is pulled low
indicating low RSTIN input. RST stays low until V
below approximately 1V. Then RST cannot be held low
any more. The controller gives up and RST is pulled up
by the external resister. A 50mV hysteresis is imple-
mented for XAO threshold.
The minimum inductance value, peak current rating,
and series resistance are factors to consider when
selecting the inductor. These factors influence the con-
verter’s efficiency, maximum output load capability,
transient-response time, and output voltage ripple. Size
and cost are also important factors to consider.
The maximum output current, input voltage, output volt-
age, and switching frequency determine the inductor
value. Very high inductance values minimize the current
ripple, and therefore reduce the peak current, which
decreases core losses in the inductor and conduction
losses in the entire power path. However, large inductor
values also require more energy storage and more turns
of wire, which increase size and can increase conduc-
tion losses in the inductor. Low inductance values
decrease the size, but increase the current ripple and
18
______________________________________________________________________________________
CC
voltage exceeds approximately 2.25V, the
IN
through resistor-dividers R11 and R12
Thermal-Overload Protection
CC
is ignored and RST is set to
XAO Voltage Detector
Design Procedure
Step-Up Regulator
Inductor Selection
CC
falls
peak current. Finding the best inductor involves choos-
ing the best compromise between circuit efficiency,
inductor size, and cost.
The equations used here include a constant LIR, which
is the ratio of the inductor peak-to-peak ripple current to
the average DC inductor current at the full load current.
The best trade-off between inductor size and circuit
efficiency for step-up regulators generally has an LIR
between 0.3 and 0.6. However, depending on the AC
characteristics of the inductor core material and ratio of
inductor resistance to other power-path resistances, the
best LIR can shift up or down. If the inductor resistance
is relatively high, more ripple can be accepted to
reduce the number of turns required and increase the
wire diameter. If the inductor resistance is relatively low,
increasing inductance to lower the peak current can
decrease losses throughout the power path. If extreme-
ly thin high-resistance inductors are used, as is com-
mon for LCD-panel applications, the best LIR can
increase to between 0.5 and 1.0.
Once a physical inductor is chosen, higher and lower
values of the inductor should be evaluated for efficiency
improvements in typical operating regions.
Calculate the approximate inductor value using the typ-
ical input voltage (V
(I
from an appropriate curve in the Typical Operating
Characteristics section, and an estimate of LIR based
on the above discussion:
Choose an available inductor value from an appropriate
inductor family. Calculate the maximum DC input cur-
rent at the minimum input voltage (V
servation of energy and the expected efficiency at that
operating point (η
in the Typical Operating Characteristics :
Calculate the ripple current at that operating point and
the peak current required for the inductor:
MAIN(MAX
L
AVDD
I
AVDD RIPPLE
I
AVDD PEAK
)), and the expected efficiency (η
I
IN DC MAX
=
_
_
(
⎛
⎝ ⎜
V
AVDD
,
V
IN
MIN
=
=
)
IN
⎞
⎠ ⎟
) taken from the appropriate curve
I
V
IN DC MAX
=
2
IN MIN
), the maximum output current
(
I
⎛
⎜
⎝
AVDD MAX
(
L
I
AVDD MAX
AVDD
V
,
IN MIN
V
)
AVDD
(
(
×
(
)
(
× ×
V
+
)
AVDD
V
)
I
× η
−
AVDD RIPPLE
AVDD
×
)
V
×
IN(MIN)
V
IN
MIN
AVDD
f
S
−
W W
_
2
×
V
IN MIN
⎞
⎟
⎠
f
SW
⎛
⎝ ⎜
) using con-
(
η
TYP)
LIR
TYP
)
)
⎞
⎠ ⎟
taken