20-101-1202 Rabbit Semiconductor, 20-101-1202 Datasheet
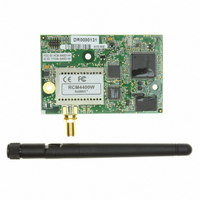
20-101-1202
Specifications of 20-101-1202
Related parts for 20-101-1202
20-101-1202 Summary of contents
Page 1
... RabbitCore RCM4400W C-Programmable Wi-Fi Core Module OEM User’s Manual 019–0160 • 090515–G ...
Page 2
... RabbitCore RCM4400W OEM User’s Manual Part Number 019-0160 • 090515–G • Printed in U.S.A. ©2007–2009 Digi International Inc. • All rights reserved. No part of the contents of this manual may be reproduced or transmitted in any form or by any means without the express written permission of Digi International. ...
Page 3
... Install Dynamic C .................................................................................................................................9 2.2 Hardware Connections........................................................................................................................10 2.2.1 Step 1 — Prepare the Prototyping Board for Development........................................................10 2.2.2 Step 2 — Attach the Antenna to the RCM4400W Module ........................................................11 2.2.3 Step 3 — Attach Module to Prototyping Board..........................................................................12 2.2.4 Step 4 — Connect Programming Cable ......................................................................................13 2.2.5 Step 5 — Connect Power ............................................................................................................14 2 ...
Page 4
Other Hardware .................................................................................................................................. 43 4.4.1 Clock Doubler ............................................................................................................................ 43 4.4.2 Spectrum Spreader...................................................................................................................... 43 4.5 Memory .............................................................................................................................................. 44 4.5.1 SRAM......................................................................................................................................... 44 4.5.2 Flash EPROM............................................................................................................................. 44 4.5.3 Serial Flash ................................................................................................................................. 44 Chapter 5. Software Reference 5.1 More About Dynamic C ..................................................................................................................... ...
Page 5
... B.4.4.1 RS-232 ............................................................................................................................. 106 B.5 Prototyping Board Jumper Configurations ......................................................................................108 Appendix C. Power Supply C.1 Power Supplies.................................................................................................................................111 C.1.1 Battery-Backup.........................................................................................................................111 C.1.2 Battery-Backup Circuit.............................................................................................................112 C.1.3 Reset Generator ........................................................................................................................113 C.1.4 Onboard Power Supplies ..........................................................................................................113 Index Schematics OEM User’s Manual 111 115 119 ...
Page 6
RabbitCore RCM4400W ...
Page 7
... Rabbit 4000’s internal real-time clock and the static RAM. One 50-pin header brings out the Rabbit 4000 I/O bus lines, parallel ports, and serial ports. ...
Page 8
... Six CMOS-compatible serial ports — four ports are configurable as a clocked serial port (SPI), and two ports are configurable as SDLC/HDLC serial ports. • Alternate I/O bus can be configured for 8 data lines and 6 address lines (shared with parallel I/O lines), I/O read/write • ...
Page 9
... Rabbit Field Utility to download compiled Dynamic C .bin files, and cloning board options for rapid production loading of programs. • Generous memory size allows large programs with tens of thousands of lines of code, and substantial data storage. • Easily scalable for commercial deployment applications OEM User’ ...
Page 10
... RCM4400W module. The items in the Development Kit and their use are as follows. • RCM4400W module with 2.4 GHz • Prototyping Board. • Universal AC adapter DC (includes Canada/Japan/U.S., Australia/N.Z., U.K., and European style plugs). Development Kits sold in North America may contain an AC adapter with only a North American style plug. ...
Page 11
... Online Documentation The online documentation is installed along with Dynamic C, and an icon for the docu- mentation menu is placed on the workstation’s desktop. Double-click this icon to reach the menu. If the icon is missing, use your browser to find and load folder, found in the Dynamic C installation folder. ...
Page 12
... Reorient or relocate the receiving antenna. • Increase the separation between the equipment and the receiver. • Connect the equipment into an outlet on a circuit different from that to which the receiver is connected. • Consult the dealer or an experienced radio/TV technician for help. ...
Page 13
... This exte- rior label can use wording such as the following: “Contains Transmitter Module FCC ID: VCB-540D144” or “Contains FCC ID: VCB-540D144.” Any similar wording that expresses the same meaning may be used ...
Page 14
... The logo mark diameter must bigger. If the equipment is 100 cm the logo mark is 3 mm. 1.4.4 Europe The marking shall include as a minimum: • the name of the manufacturer or his trademark; • the type designation; • equipment classification, (see below). Receiver Class Highly reliable SRD communication media, e.g., serving human life 1 inherent systems (may result in a physical risk to a person) ...
Page 15
... The installation allows you to choose the COM port that will be used. The default selec- tion is COM1. You may select any available port for Dynamic C’s use. If you are not cer- tain which port is available, select COM1. This selection can be changed later within Dynamic C ...
Page 16
... Remember to use ESD protection regardless of whether you are working with the RCM4400W module on the Prototyping Board or in your own OEM application. 2.2.1 Step 1 — Prepare the Prototyping Board for Development Snap in four of the plastic standoffs supplied in the bag of accessory parts from the Devel- opment Kit in the holes at the corners as shown in Figure 2 ...
Page 17
... Step 2 — Attach the Antenna to the RCM4400W Module Attach the antenna to the antenna SMA connector on the RCM4400W as shown in Figure 3. Figure 3. Attach the Antenna to the RCM4400W Module CAUTION: Do not remove the RF shield by the antenna since any attempt to remove the shield will damage the RF circuits underneath it. ...
Page 18
... Turn the RCM4400W module so that the mounting holes line up with the corresponding holes on the Prototyping Board. Insert the metal standoffs as shown in Figure 4, secure them from the bottom using the 4-40 × 3/16 screws and washers, then insert the module’s header J1 on the bottom side into socket RCM1 on the Prototyping Board. ...
Page 19
... Your PC should recognize the new USB hardware, and the LEDs in the shrink-wrapped area of the USB programming cable will flash — if you get an error message, you will have to install USB drivers. Drivers for Windows XP are available in the Dynamic C Drivers\Rabbit USB Programming Cable\WinXP_2K to install the USB drivers ...
Page 20
... AC adapter as shown in Figure 5, then press down on the plug until it clicks into place. Connect the AC adapter to 3-pin header J1 on the Prototyping Board as shown in Figure 5 above. The connector may be attached either way as long not offset to one side— the center pin always connected to the positive terminal, and either edge pin is ground. ...
Page 21
... Channel—the channel the access point is on (1–11). • Signal—the signal strength of the access point. • MAC—the hardware (MAC) address of access point. • Access Point SSID—the SSID the access point is using. OEM User’s Manual menu. Select ...
Page 22
... Dynamic C menu. Select a slower Max download baud rate. Click dialog on the “Communications” tab in the Dynamic C menu. Choose a lower debug baud rate. Click message once this step is completed successfully. , check that the COM port OK to save ...
Page 23
... The user's manual also provides complete hardware reference information and software function calls for the RCM4400W series of modules and the Prototyping Board. For advanced development topics, refer to the Dynamic C User’s Manual, also in the online documentation set. 2.4.1 Technical Support NOTE: If you purchased your RCM4400W through a distributor or through a Rabbit partner, contact the distributor or partner first for technical support ...
Page 24
RabbitCore RCM4400W ...
Page 25
... Wi-Fi features. NOTE: The sample programs assume that you have at least an elementary grasp of the C language. If you do not, see the introductory pages of the Dynamic C User’s Manual for a suggested reading list. In order to run the sample programs discussed in this chapter and elsewhere in this manual, 1. Your module must be plugged in to the Prototyping Board as described in Chapter 2, “ ...
Page 26
... Dynamic C STDIO window. Press “2” or “3” on your keyboard to select LED DS2 or DS3 on the Prototyping Board. Then follow the prompt in the Dynamic C or OFF. A logic low will light up the LED you selected. —demonstrates the use of assembly language to flash LEDs DS2 and • ...
Page 27
... TAMPERDETECTION.C mode. When an attempt is detected, the battery-backed onchip-encryption RAM on the Rabbit 4000 is erased. This battery-backed onchip-encryption RAM can be useful to store data such as an AES encryption key from a remote location. This sample program shows how to load and read the battery-backed onchip-encryption RAM and how to enable a visual indicator ...
Page 28
... Serial Port D for • FLOWCONTROL.C CTS/RTS flow control with serial data coming from Serial Port C (TxC) at 115,200 bps. The serial data received are displayed in the To set up the Prototyping Board, you will need to tie TxD and RxD ...
Page 29
... Since the J4 header locations on the two Prototyping Boards are connected with wires, there are no slip-on jumpers either Prototyping Board. —This program demonstrates transmitting and then receiving an • SWITCHCHAR.C ASCII string on Serial Ports C and D. It also displays the serial data received from both ports in the window ...
Page 30
... IDC header supplied with the accessory parts in the Development Kit. Once you have compiled and run this program, press and release switches the Prototyping Board. The data echoed between the serial ports will be displayed in the 24 —This program demonstrates how to set up Serial Ports E IOCONFIG.EXE folder. library generated by STDIO window. ...
Page 31
... Web server and stores a log of • SERIAL_FLASHLOG.C hits on the home page of the serial flash “server.” This log can be viewed and cleared from a browser at http://10.10.6.100/. You will likely have to first “configure” your net- work interface card for a “10Base-T Half-Duplex,” “100Base-T Half-Duplex,” “ ...
Page 32
RabbitCore RCM4400W ...
Page 33
... Chapter 4 describes the hardware components and principal hardware subsystems of the RCM4400W. Appendix A, “RCM4400W Specifica- tions,” provides complete physical and electrical specifications. Figure 6 shows the Rabbit-based subsystems designed into the RCM4400W. Figure 6. RCM4400W Subsystems The 58.98 MHz frequency shown for the RCM4400W is generated using a 29.49 MHz crystal with the Rabbit 4000 clock doubler enabled. OEM User’ ...
Page 34
RCM4400W Digital Inputs and Outputs Figure 7 shows the RCM4400W pinouts for header J1. standard 2 × 25 IDC header with a nominal 1.27 mm pitch. Headers Figure 7. RCM4400W Pinout RabbitCore RCM4400W ...
Page 35
... Figure 8 shows the use of the Rabbit 4000 microprocessor ports in the RCM4400W modules. Figure 8. Use of Rabbit 4000 Ports The ports on the Rabbit 4000 microprocessor used in the RCM4400W are configurable, and so the factory defaults can be reconfigured. Table 2 lists the Rabbit 4000 factory defaults and the alternate configurations. OEM User’s Manual 29 ...
Page 36
... PB6 Input/Output 23 PB7 Input/Output 30 Default Use Alternate Use Reset input Slave port data bus (SD0–SD7) External I/O data bus (ID0–ID7) SCLK External I/O Address IA6 SCLKA External I/O Address IA7 /SWR External I/O Address IA0 /SRD External I/O Address ...
Page 37
... PC3 Input/Output 28 PC4 Input/Output 29 PC5 Input/Output 30 PC6 Input/Output 31 PC7 Input/Output 32 PE0 Input/Output OEM User’s Manual Default Use Alternate Use TXD I/O Strobe I0 Timer C0 TCLKF RXD/TXD I/O Strobe I1 Timer C1 RCLKF Input Capture TXC/TXF I/O Strobe I2 Timer C2 RXC/TXC/RXF I/O Strobe I3 Timer C3 SCLKD ...
Page 38
Table 2. RCM4400W Pinout Configurations (continued) Pin Pin Name 33 PE1 Input/Output 34 PE2 Input/Output 35 PE3 Input/Output 36 PE4 Input/Output FPGA Interrupt 37 Output/PE5/ Input/Output SMODE0 FPGA Chip 38 Select/PE6/ Input/Output SMODE1 39 PE7/STATUS Input/Output 32 Default Use Alternate ...
Page 39
... Pin Name 40 PD0 Input/Output 41 PD1 Input/Output 42 PD2 Input/Output 43 PD3 Input/Output 44 PD4 Input/Output 45 PD5 Input/Output OEM User’s Manual Default Use Alternate Use I/O Strobe I0 Timer C0 D8 INT0 SCLKD/TCLKF QRD1B IA6 I/O Strobe I1 Timer C1 D9 INT1 RXD/RCLKF QRD1A Input Capture I/O Strobe I2 Timer C2 ...
Page 40
Table 2. RCM4400W Pinout Configurations (continued) Pin Pin Name 46 PD6 Input/Output 47 PD7 Input/Output 48 Not Connected 49 Not Connected 50 GND 34 Default Use Alternate Use I/O Strobe I6 D14 PWM2 TXA/TXE IA7 I/O Strobe I7 D15 PWM3 ...
Page 41
... Parallel Port A can also be used as an external I/O data bus to isolate external I/O from the main data bus. Parallel Port B pins PB2–PB7 can also be used as an auxiliary address bus. When using the auxiliary I/O bus for any reason, you must add the following line at the beginning of your program ...
Page 42
Serial Communication The RCM4400W module does not have any serial driver or receiver chips directly on the board. However, a serial interface may be incorporated on the board the RCM4400W is mounted on. For example, the Prototyping Board has ...
Page 43
... NOCHARASSYINBRK #define RS232_NOCHARASSYINBRK This macro is already defined so that it is the default behavior for the sample programs in the Dynamic C SAMPLES\RCM4400W\SERIAL OEM User’s Manual Serial Port E Serial Port F RCLKE and RCLKF must be selected the same parallel port as TXE and TXF respectively. library requires you to define the macro folder ...
Page 44
... The data interface between the FPGA and the UBEC UW2453 based 802.11b radio section consists of a D/A converter and an A/D converter. Both devices convert “I” and “Q” data samples at a rate of 40 MHz. The UBEC UW2453 is a single-chip transceiver with integrated power amplifier for the 2 ...
Page 45
... Many countries specify the channel range and power limits for Wi-Fi devices operated within their borders, and these limits are set automatically in the RCM4400W in firmware according to the country or region. For example, only channels 1–11 are authorized for use in the United States or Canada, and so channels 12 and 13 are disabled. See Section 6.2.4.1 for additional information and sample programs demonstrating how to configure an end device to meet the regulatory channel range and power limit requirements ...
Page 46
... Alternate Uses of the Programming Port All three Serial Port A signals are available as • a synchronous serial port • an asynchronous serial port, with the clock line usable as a general CMOS I/O pin The programming port may also be used as a serial port via the programming cable. ...
Page 47
... Run Mode when no programming cable is attached. When the Rabbit 4000 is reset, the operating mode is determined by the status of the SMODE pins. When the programming cable’s the SMODE pins are pulled high, placing the Rabbit 4000 in the Program Mode. When the programming cable’ ...
Page 48
... A program “runs” in either mode, but can only be downloaded and debugged when the RCM4400W is in the Program Mode. Refer to the Rabbit 4000 Microprocessor User’s Manual gramming port. 4.3.2 Standalone Operation of the RCM4400W Once the RCM4400W has been programmed successfully, remove the programming cable from the programming connector and reset the RCM4400W ...
Page 49
... The spectrum spreader will now remain off whenever you OK are in the project file where you defined the macro. NOTE: Refer to the Rabbit 4000 Microprocessor User’s Manual for more information on the spectrum-spreading setting and the maximum clock speed. OEM User’s Manual Options > ...
Page 50
... EPROM since it may be necessary to change the sector size in the future. Writing to arbitrary flash memory addresses at run time is discouraged. Instead, define a “user block” area to store persistent data. The functions writeUserBlock and readUserBlock are provided for this. Refer to the for additional information. ...
Page 51
... Dynamic C development environment. Debugging occurs while the application runs on the target. Alternatively, users can compile a program to an image file for later loading. Dynamic C runs on PCs under Windows NT and later— see Rabbit’s Technical Note TN257, Running Dynamic C additional information if you are using a Dynamic C under Windows Vista ...
Page 52
... C, SPI, GPS, file system. LCD display and keypad drivers. • Powerful language extensions for cooperative or preemptive multitasking • Loader utility program to load binary images into Rabbit targets in the absence of Dynamic C. • Provision for customers to create their own source code libraries and augment on-line help by creating “ ...
Page 53
... Certain function calls involve reading and storing calibration constants from/to the simulated EEPROM in flash memory located at the top 2K of the reserved user block memory area (3800–39FF). This leaves the address range 0–37FF in the user block available for your application. These address ranges may change in the future in response to the volatility in the flash memory market, in particular sector size ...
Page 54
... This flag is also stored in the battery-backed SRAM. When a protected variable is updated, the “inactive” copy is modified, and is made “active” only when the update is 100% complete. This assures the integrity of the data in case a reset or a power failure occurs during the update process ...
Page 55
... If your application has written to the flash before calling init() spin on as shown in the sample code to ensure that the write is complete. sf_isWriting() while (sf_isWriting()) { // waiting for write to complete before calling sock_init } sock_init(); OEM User’s Manual sock_ , be sure to sock_init() 49 ...
Page 56
Prototyping Board Function Calls The function calls described in this section are for use with the Prototyping Board features. The source code is in the Dynamic C library if you need to modify it for your own board design. ...
Page 57
... PARAMETERS the input port data register to poll (e.g., PADR) dataport the input port bit (0–7) to poll portbit the value receive value the duration of the timeout in seconds (enter 0 for no timeout) ...
Page 58
Upgrading Dynamic C Dynamic C patches that focus on bug fixes are available from time to time. Check the Web site www.rabbit.com/support/ 5.3.1 Add-On Modules Dynamic C installations are designed for use with the board they are included with, ...
Page 59
... PCI, PCMCIA, CompactFlash, USB and SD/MMC interfaces, and Wi-Fi devices such as Web-based cameras and print servers. 802.11b can operate in one of two modes—in a managed-access mode (BSS), called an infrastructure mode unmanaged mode (IBSS), called the ad-hoc mode. The 802.11 standard describes the details of how devices access each other in either of these modes ...
Page 60
In fact, the 802.11b default configuration is often sufficient for a device to join an access point automatically, which it can do once enabled. Commands issued to ...
Page 61
... The programming cable must connect the programming header on the module to your PC. 4. Power must be applied to the module through the Prototyping Board. Refer to Chapter 2, “Getting Started,” if you need further information on these steps. To run a sample program, open it with the Each sample program has comments that describe the purpose and function of the pro- gram. Follow the instructions at the beginning of the sample program. Complete information on Dynamic C is provided in the Dynamic C User’ ...
Page 62
... Wi-Fi Setup Figure 11 shows how your development setup might look once you’re ready to proceed. 56 Figure 11. Wi-Fi Host Setup RabbitCore RCM4400W ...
Page 63
... USB port to program the RCM4400W module. You will need either an access point for an existing Wi-Fi network that you are allowed to access and have note- book connected to that network (infrastructure mode), or you will need at least a PDA or PC with Wi-Fi to use the ad-hoc mode. User’s Manual 57 ...
Page 64
... FIG 5 or TCPCONFIG 1 #define TCPCONFIG 5 NOTE: TCPCONFIG 0 is not supported for Wi-Fi applications. There are some other “standard” configurations for mented in the Rabbit4000\LIB\TCPIP\TCP_CONFIG.LIB is available in the Dynamic C TCP/IP User’s Manual. 58 library. This macro "255.255.255.0" "10.10.6.1" "10.10.6.1" (no DHCP) and TCPCONFIG 1 at the beginning of your program. ...
Page 65
... PC/Laptop/PDA Configuration This section shows how to configure your PC or notebook to run the sample programs. Here we’re mainly interested in the PC or notebook that will be communicating wirelessly, which is not necessarily the PC that is being used to compile and run the sample program on the RCM4400W module. ...
Page 66
... Once a sample Connection program is running, you will be able to select the network from a list of available networks. You will have set your wireless network name with the the ad-hoc mode as explained in Section 6.2.3.1, “Network/Wi-Fi Configuration.” 60 tab, and check . Now click on _WIFI_SSID ...
Page 67
... The sample programs in Section 6.2.4.1 show how to set up the country- or region-specific attributes, but do not show the basic setup of a wireless network. The sample programs in Section 6.2.4.2 show the setup and operation of a wireless network — the sample program is ideal to demonstrate that the RCM4400W has been hooked up correctly and that the Wi-Fi setup is correct so that an access point can be found ...
Page 68
... RCM4400W module. Rabbit recommends that you check the reg- ulations for the country where your system incorporating the RCM4400W will be deployed for any other requirements. 62 —demonstrates how the multi-domain options from the #define WIFI_REGION_VERBOSE —demonstrates how the region or country can be set at #define _WIFI_ window will dis- STDIO win- STDIO ...
Page 69
... The Dynamic C dow will then display a menu that allows you to complete the configuration of the user interface. 6.2.4.2 Wi-Fi Operation —sends out a series of pings to a RabbitCore module on an ad-hoc • WIFIPINGYOU.C Wi-Fi network. ...
Page 70
... Before you run this sample program, configure the Dynamic C library and your TCPCONFIG 1. Use macro definitions in the “Defines” tab in the Dynamic C Options > Project Options menu to modify any parameter settings. If you are not using DHCP, set the IP parameters to values appropriate to your network. ...
Page 71
... BROWSELED.C Two “device LEDs” are created along with two buttons to toggle them. Users can use their Web browser to change the status of the lights. The DS2 and DS3 LEDs on the Prototyping Board will match those on the Web page. As long as you have not modified ...
Page 72
... Initially, it may be easier to use the 64 hexadecimal digits form of the key rather than the ASCII passphrase. A passphrase requires considerable computation effort, which delays the startup of the sample by about 40 seconds. If you want to add authentication, set the authentication to “open system,” which basi- cally means that knowing the key is sufficient to allow access. #define WIFI_AUTH WIFICONF_AUTH_OPEN_SYS Change to the host you want to ping ...
Page 73
... WIFI_WLN_API.LIB Wi-Fi Parameters • Access Point SSID— _WIFI_SSID macro to a string for the SSID of the access point in the infrastructure _WIFI_SSID (BSS) mode, or the SSID of the ad-hoc network in the ad-hoc (IBSS) mode. ...
Page 74
... The following four encryption keys are provided. If WEP encryption is enabled, at least one key should be specified — do not use the defaults. You will have to modify these keys according to the encryption keys in effect for the Wi-Fi network you wish to access. A key is specified as either comma-separated byte values. ...
Page 75
... SSID "rabbitTest" Using a passphrase is rather slow. It takes a Rabbit 4000 more than 20 seconds to gen- erate the actual 256-bit key from the passphrase. If you use a passphrase and WIFI_VERBOSE_PASSPHRASE corresponding to that passphrase and SSID. If both ...
Page 76
... Type “TCPCONFIG” in the Function Search field, and hit <Enter> . Scroll down to the section on “Wi-Fi Configuration.” The Dynamic C TCP/IP User’s Manual.(Volume 1) provides additional information about these macros and Wi-Fi also possible to redefine any of the above parameters dynamically using the function call ...
Page 77
... The cmd, data, and len parameters are described in detail below. Each cmd (command) has different requirements for the data and len parameters. Note that these are strings in all cases, even for “numeric” parameters. be down when you are using the shaded commands that change the configuration. ...
Page 78
... If you don’t want encryption enabled, do not execute the WIFI_WEP_FLAG command in the table. RETURN VALUE 0 = success ...
Page 79
... Use each command macro in its own the “rabbit” access point and set a transmit rate of 11 Mbits/s, you would have these two lines of code in your program. int wifi_ioctl(IF_WIFI0, WIFI_SSID, "rabbit", 0); int wifi_ioctl(IF_WIFI0, WIFI_TX_RATE, WIFICONF_RATE_11MBPS, 0); Let’s look at the individual wifi_ioctl() WIFI_SSID An SSID (service set identifier) names a specific wireless LAN (WLAN). All devices on a single WLAN must share a common SSID. Set this value to your WLAN’ ...
Page 80
... Japan _JAPAN_REGION Australia _AUSTRALIA_REGION The following sample code shows how to set Australia. auto int country; country = _AUSTRALIA_REGION; wifi_ioctl(IF_WIFI0, WIFI_COUNTRY_SET, &country, 0); 74 Macro Region Number Channel Range 1–11 1–11 (indoors) 9–11 (outdoors) 1–11 1–13 10–13 3–11 1–11 1–13 1–11 RabbitCore RCM4400W ...
Page 81
... You can use either 40-bit (5-byte) or 104-bit (13-byte) keys for WIFICONF_WEP_TKIP WEP (Wired Equivalent Privacy). WIFI_WEP_USEKEY Indicates which key ("0"–"3") is the default transmission key. The setting may be left at the "0" default. The setting of the WEP keys is described below. User’s Manual . ...
Page 82
... Set to 5 for a 40-bit key for a 104-bit key. Marketing literature sometimes refers len to these as 64-bit or 128-bit keys. The 24 “extra” bits that are included in the marketing description serve as a cryptographic initialization vector. WIFI_AUTH The authentication option is used to configure different types of authentication that the Wi-Fi device supports. There are three types of authentication that are supported— ...
Page 83
... WIFI_RTS_THRESH Sets the threshold (in bytes) beyond which an RTS (request to send) frame must be sent before the data frame can be sent. This can sometimes help performance with busy net- works, although it is not used frequently. User’s Manual ) ) ) ) ...
Page 84
... ID (max. length 32) ssid_len = SSID length in bytes channel = channel number (1–13) bss_addr = BSS ID (access point MAC address) bss_caps reserved wpa_info reserved erp_info reserved rates reserved rates_basic reserved atim reserved tx_rate = maximum transmit rate (in 100 kbps) rx_signal = received signal strength (0–107) 78 RabbitCore RCM4400W ...
Page 85
... BSS ID (access point MAC address) bss_caps reserved wpa_info reserved authen reserved encrypt reserved tx_rate = current transmit rate (in 100 kbps) rx_rate = last received rate (in 100 kbps) rx_signal = last received signal strength (0–107) tx_power reserved country_info reserved User’s Manual WLN_ST_xxx (see below) 79 ...
Page 86
The structure element can provide more information on the current state of the Wi-Fi state driver. It can have the following values. WLN_ST_STOPPED = Wi-Fi driver is stopped WLN_ST_SCANNING = currently performing a scan WLN_ST_ASSOC_ESS = associated with an access ...
Page 87
... Instead of executing the above sequence based debugging tool to transmit packets (ARP, DHCP, association, init_or_exit(1) and authentication) while bringing up the interface and to get the IP address. User’s Manual after all the Wi-Fi parameters have been defined. The macros. Otherwise the Wi-Fi interface is neither up nor ifup(IF_WIFI0) ...
Page 88
... Use the Technical Support e-mail form at www.rabbit.com/support/. If the sample programs ran fine, you are now ready to go on. An Introduction to TCP/IP and the Dynamic C TCP/IP User’s Manual.provide background and reference information on TCP/IP, and are available on the CD and on our Web site ...
Page 89
... Appendix A provides the specifications for the RCM4400W, and describes the conformal coating. OEM User’s Manual A A. RCM4400W PPENDIX S PECIFICATIONS 83 ...
Page 90
A.1 Electrical and Mechanical Characteristics Figure A-1 shows the mechanical dimensions for the RCM4400W. Figure A-1. RCM4400W Dimensions NOTE: All measurements are in inches followed by millimeters enclosed in parentheses. All dimensions have a manufacturing tolerance of ±0.01" (0.25 mm). ...
Page 91
... It is recommended that you allow for an “exclusion zone” of 0.04" (1 mm) around the RCM4400W in all directions when the RCM4400W is incorporated into an assembly that includes other printed circuit boards. An “exclusion zone” of 0.08" (2 mm) is recom- mended below the RCM4400W when the RCM4400W is plugged into another assembly. ...
Page 92
... SDLC/HDLC • 1 asynchronous clocked serial port shared with pro- gramming port • 1 clocked serial port shared with serial flash Maximum asynchronous baud rate = CLK/8 Slave port allows the RCM4400W to be used as an intelligent peripheral device slaved to a master ...
Page 93
... Power (pins unloaded) Operating Temperature Humidity Connectors Board Size Antenna Power Output Compliance OEM User’s Manual RCM4400W 2-channel quadrature decoder accepts inputs from external incremental encoder modules 3.3 V.DC ±5% 450 mA @ 3.3 V while transmitting/receiving 3.3 V while not transmitting/receiving -30°C to +75°C ...
Page 94
A.1.1 Antenna The RCM4400W Development Kit includes a 2.4 GHz (+2 dB) dipole antenna whose dimensions are shown in Figure A-3. Figure A-3. RCM4400W Development Kit Dipole Antenna NOTE: All measurements are in inches followed by millimeters enclosed in parentheses. ...
Page 95
... SMT header with a 1.27 mm pin spacing. J2, the programming port × 5 header with a 1.27 mm pin spacing Figure A-4 shows the layout of another board for the RCM4400W to be plugged into. These reference design values are relative to one of the mounting holes. Figure A-4. User Board Footprint for RCM4400W OEM User’s Manual 89 ...
Page 96
... V, 25°C All other I/O I DRIVE (except TXD+, TXDD+, TXD-, TXDD-) 90 Parameter Maximum Rating -40° to +85°C -55° to +125°C VDD IO (max. 3 –40°C to +85°C, VDD A Min 3 Typ Max 3.3 V 3.6 V 1.8 V 1.90 V 2.0 V ...
Page 97
... Table A-5 lists the external capacitive bus loading for the various RCM4400W output ports. Be sure to add the loads for the devices you are using in your custom system and verify that they do not exceed the values in Table A-5. Table A-5. External Capacitive Bus Loading -20°C to +85°C Output Port All I/O lines with clock doubler enabled OEM User’ ...
Page 98
... Figure A-5 shows a typical timing diagram for the Rabbit 4000 microprocessor external I/O read and write cycles. Figure A-5. External I/O Read and Write Cycles—No Extra Wait States NOTE: /IOCSx can be programmed to be active low (default) or active high. 92 RabbitCore RCM4400W ...
Page 99
... The measurements are taken at the 50% points under the following conditions. • -20°C to 85° VDD • Internal clock to nonloaded CLK pin delay ≤ 85°C/3.0 V The clock to address output delays are similar, and apply to the following delays. • the clock to address delay adr • ...
Page 100
... A.5 Conformal Coating The areas around the 32 kHz real-time clock crystal oscillator have had the Dow Corning silicone-based 1-2620 conformal coating applied. The conformally coated area is shown in Figure A-6. The conformal coating protects these high-impedance circuits from the effects of moisture and contaminants over time. ...
Page 101
... SMODE0 Output on J1 pin 37 PE7 or STATUS Output JP3 on J1 pin 39 JP4 Reserved for future use. NOTE: The jumper connections are made using 0 Ω surface-mounted resistors. OEM User’s Manual Pins Connected 1–2 PE6 2–3 SMODE1 1–2 PE5 2–3 SMODE0 1–2 PE7 2– ...
Page 102
RabbitCore RCM4400W ...
Page 103
... RCM4400W and to build prototypes of your own circuits. The Prototyping Board has power-supply connec- tions and also provides some basic I/O peripherals (RS-232, LEDs, and switches), as well as a prototyping area for more advanced hardware development. OEM User’s Manual B. P ROTOTYPING B OARD ...
Page 104
B.1 Introduction The Prototyping Board included in the Development Kit makes it easy to connect an RCM4400W module to a power supply and a PC workstation for development. It also pro- vides some basic I/O peripherals (RS-232, LEDs, and switches), ...
Page 105
... The header plug leading to bare leads provided for overseas customers can be connected to the 3-pin header in either orientation. Users providing their own power supply should ensure that it delivers 8– The voltage regulators will get warm while in use. Regulated Power Supply • ...
Page 106
... NOTE: No analog signals are available on the Prototyping Board with the RCM4400W RabbitCore module installed since no analog signals are present on the RCM4400W’s header J1. —Two 3-wire or one 5-wire RS-232 serial ports are available on the Prototyp- • RS-232 ing Board at header J4. A 10-pin 0.1" pitch header strip installed at J4 allows you to connect a ribbon cable that leads to a standard DE-9 serial connector ...
Page 107
... B.2 Mechanical Dimensions and Layout Figure B-2 shows the mechanical dimensions and layout for the Prototyping Board. Figure B-2. Prototyping Board Dimensions NOTE: All measurements are in inches followed by millimeters enclosed in parentheses. All dimensions have a manufacturing tolerance of ±0.01" (0.25 mm). OEM User’s Manual 101 ...
Page 108
... Prototyping Area Connectors B.3 Power Supply The RCM4400W requires a regulated 3.0 V – 3 power source to operate. Depend- ing on the amount of current required by the application, different regulators can be used to supply this voltage. The Prototyping Board has an onboard +5 V switching power regulator from which a +3 ...
Page 109
... The analog signals are brought out to labeled points at header location J3 on the Prototyping Board. Although header J3 is unstuffed × 7 header can be added. Note that analog signals are not available when the RCM4400W included in the Development Kit installed. OEM User’s Manual 103 ...
Page 110
... The holes in the prototyping area are spaced at 0.1" (2.5 mm). +3 and GND traces run along the top edge of the prototyping area for easy access. Small to medium circuits can be prototyped using point-to-point wiring with AWG wire between the proto- typing area, the +3 and GND traces, and the surrounding area where surface- mount components may be installed ...
Page 111
... Figure B-5. Prototyping Board Current-Measurement Option NOTE: Once you have cut the trace below header location JP1 or JP2, you must either be using the ammeter or have a jumper in place in order for power to be delivered to the Prototyping Board. OEM User’s Manual 105 ...
Page 112
... RS-232 transceiver installed at U3. This transceiver provides the voltage output, slew rate, and input voltage immunity required to meet the RS-232 serial communication protocol. Basically, the chip translates the Rabbit 4000’s signals to RS-232 signal levels. Note that the polarity is reversed in an RS-232 circuit so that a +3.3 V output becomes approxi- mately -10 V and output as +10 V ...
Page 113
... RS232.LIB of the flow control lines are specified using a set of five macros. SERX_RTS_PORT—Data register for the parallel port that the RTS line is on (e.g., PCDR). SERA_RTS_SHADOW—Shadow register for the RTS line's parallel port (e.g., PCDRShadow). SERA_RTS_BIT—The bit number for the RTS line. ...
Page 114
... Header Description JP1 +5 V Current Measurement JP2 +3.3 V Current Measurement JP3 PC0/TxD/LED DS2 JP4 108 Pins Connected 1–2 Via trace or jumper 1–2 Via trace or jumper JP3 TxD on header J4 1–2 JP4 PC0 to LED DS2 1–2 n.c. PC0 available on header J2 Factory Default ...
Page 115
... PC3 to Switch S3 1–2 JP10 RxC on header J4 1–2 n.c. PC3 available on header J2 1–2 1–2 Connected: PB2 to LED DS2 n.c. PB2 available on header J2 1–2 1–2 Connected: PB3 to LED DS3 n.c. PB3 available on header J2 1–2 1–2 Connected: PB4 to Switch S2 n ...
Page 116
... JP24 LN0_IN–LN3_IN JP25 Thermistor Location NOTE: Jumper connections JP3–JP10, JP12, JP14, JP16, JP18, JP23, and JP24 are made using 0 Ω surface-mounted resistors. Jumper connections JP11, JP13, JP15, JP17, and JP19–JP22 are made using 470 Ω surface-mounted resistors. 110 Pins Connected 1– ...
Page 117
... Rabbit 4000 real-time clock to retain data with the RCM4400W powered down. Figure C-1. External Battery Connections A battery with a nominal voltage and a minimum capacity of 165 mA·h is recom- mended. A lithium battery is strongly recommended because of its nearly constant nominal voltage over most of its life. OEM User’s Manual C. P PPENDIX at Header J1 S ...
Page 118
... It reduces the battery voltage to the SRAM and to the real-time clock, thereby limiting the current consumed by the real-time clock and lengthening the battery life. • It ensures that current can flow only out of the battery to prevent charging the battery. • A voltage, VOSC, is supplied to U13, which keeps the 32.768 kHz oscillator working when the voltage begins to drop ...
Page 119
... Wi-Fi circuits. The program in the SAMPLES\RCM4400W\TCPIP\ Figure C-3. RCM4400W Onboard Power Supplies Voltage +2. +2. +2. +1 OEM User’s Manual POWERDOWN.C folder demonstrates this functionality. Power Supply Use VDD_PA VDD_VCO VDD_XCVR FPGA VCCAUX FPGA VCCINT sample ...
Page 120
RabbitCore RCM4400W ...
Page 121
... JP20 (LN5 buffer/filter to RCM4400W) ............ 110 JP21 (LN6 buffer/filter to RCM4400W) ............ 110 JP22 (LN7 buffer/filter to RCM4400W) ............ 110 JP23 (analog inputs LN4– LN6 configuration) .. 110 JP24 (analog inputs LN0– LN3 configuration) .. 110 JP3–JP4 (PC0/TxD/LED DS2) ......................... 108 JP5–JP6 (PC1/RxD/Switch S2) ............................ 109 JP7– ...
Page 122
... RCM4400W ......................95 JP1 (FPGA chip select, PE6, or SMODE1 output on J1) .....................................95 JP2 (FPGA interrupt output, PE5, or SMODE0 output on J2) ..........................95 JP3 (PE7 or STATUS output on J1) ...............95 JP4 .................................95 jumper locations ............95 L labeling requirements ..............7 LEDs Wi-Fi association and activity ........................................40 O onchip-encryption RAM how to use ..........................21 operating region configura- tion ...
Page 123
... T technical support ................... 17 OEM User’s Manual U user block determining size ................ 47 function calls ..................... 47 readUserBlock() ............ 44 writeUserBlock() ........... 44 reserved area for calibration constants ....................... 47 W Wi-Fi additional resources .......... 82 bring interface down ...
Page 124
RabbitCore RCM4400W ...
Page 125
... RCM4400W Schematic www.rabbit.com/documentation/schemat/090-0239.pdf 090-0230 Prototyping Board Schematic www.rabbit.com/documentation/schemat/090-0230.pdf 090-0128 Programming Cable Schematic www.rabbit.com/documentation/schemat/090-0128.pdf 090-0252 USB Programming Cable Schematic www.rabbit.com/documentation/schemat/090-0252.pdf You may use the URL information provided above to access the latest schematics directly. OEM User’s Manual S CHEMATICS 119 ...
Page 126
...