STM23S-2AN Applied Motion, STM23S-2AN Datasheet - Page 4
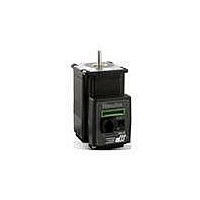
STM23S-2AN
Manufacturer Part Number
STM23S-2AN
Description
Stepper Motors 125 oz-in max RS-232 Comm.
Manufacturer
Applied Motion
Datasheet
1.STM23S-2AE.pdf
(4 pages)
Specifications of STM23S-2AN
Voltage Rating
24 V
Rotor Inertia
1.42 oz-in-sq
Continuous Output Power
40 mA
Dimensions
92.4 mm x 56.4 mm x 56.4 mm
Minimum Holding Torque
125 oz-in
Lead Free Status / RoHS Status
Lead free / RoHS Compliant
Anti-Resonance/Electronic Damping
Step motor systems have a natural tendency to resonate at
certain speeds. The STM drive+motor automatically calcu-
lates the system’s natural frequency and applies damping
to the control algorithm. This greatly improves midrange
stability, allows for higher speeds, greater torque utilization
and also improves settling times.
Microstep Emulation
With Microstep Emulation, low resolution systems can still provide
smooth motion. The drive can take low-resolution step pulses and
create fine resolution micro-step motion.
Torque Ripple Smoothing
All step motors have an inherent low speed torque ripple
that can affect the motion of the motor. By analyzing this
torque ripple the system can apply a negative harmonic
to negate this effect, which gives the motor much
smoother motion at low speed.
Command Signal Smoothing
Command Signal smoothing can soften the effect of
immediate changes in velocity and direction, making the
motion of the motor less jerky. An added advantage is
that it can reduce the wear on mechanical components.
Dynamic Current Control
Allows for three current settings to help the motor run cooler and reduce power con-
sumption.
▪
▪
▪
System Runs Cooler
Delivers better motor performance and higher speeds
Delivers smoother motion in any application
Delivers smoother motion at lower speeds
Delivers smoother system performance
Self Test & Auto Setup
At start-up the drive measures motor parameters, including the resistance and inductance,
then uses this information to optimize the system performance.
Running Current - the current the drive will deliver for continuous motion.
Accel Current - the current the drive will deliver when accelerating or decelerating.
Idle Current - reduces current draw when motor is stationary.
1.8° Steps
Synthesized
Microsteps
The ST drive with the CANopen option board has the ability to access, modify
and trigger a Q program stored in the drive.
The user develops and downloads a program using the Q Programmer™
software via RS-232. The program sequences can then be triggered via the
CANopen network, creating a powerful distributed motion control system.
CANopen Model
RS232 Model
Q over CANopen
ID 5
# 5
# 5
MMI Control Option
ID 4
# 4
# 4
RS232
Each drive connects
to a port on the hub.
ID 3
# 3
# 3
Run/Stop (Toggle Switch)
ID 2
# 2
3rd Party Controller
# 2
RS232
Speed1/Speed2 (Toggle Switch)
RS485
RS485/422
RS485 Model
Speed (Potentiometer)
UP TO
AXES
UP TO
AXES
8
4
ID 1
# 1
ID 5
# 5
# 1
RS232
# 5
or
MMI Control Option
UP TO
32
UP TO
32
AXES
AXES
127
ID 4
# 4
UP TO
AXES
# 4
RS232
Each drive connects
to a port on the hub.
RS232
ID 3
# 3
# 3
Run/Stop (Toggle Switch)
ID 2
# 2
3rd Party Controller
# 2
RS232
Speed1/Speed2 (Toggle Switch)
RS485
RS485/422
Speed (Potentiometer)
RS485/422
RS485/422
RS485/422
UP TO
UP TO
AXES
AXES
8
4
ID 1
# 1
# 1
RS232
Step & Direction
Oscillator / Run-Stop
Host Control
Stand-Alone Programmable
Multi-axis Systems
Use SiNet Hub Programmer software to develop your sequence of events, then download
them to a SiNet Hub for a stand-alone system or stream serial commands to the drives from a
PC, PLC, HMI, or other host controller.
or
RS232
ID 5
ID 5
# 5
# 5
# 5
# 5
UP TO
32
UP TO
32
AXES
AXES
127
UP TO
AXES
ID 5
# 5
MMI Control Option
MMI Control Option
# 5
RS232
ID 4
ID 4
# 4
# 4
ID 5
# 5
# 5
MMI Control Option
# 4
# 4
RS232
RS232
MMI Control Option
ID 4
# 4
# 4
RS232
MMI Control Option
Each drive connects
to a port on the hub.
Each drive connects
to a port on the hub.
ID 3
ID 3
# 3
# 3
# 3
# 3
RS232
ID 4
# 4
# 4
RS232
Each drive connects
to a port on the hub.
ID 3
# 3
# 3
RS232
RS232
ID 2
ID 2
# 2
# 2
# 2
# 2
Run/Stop (Toggle Switch)
Each drive connects
to a port on the hub.
RS232
RS232
ID 2
# 2
ID 3
# 2
# 3
3rd Party Controller
RS485
RS485
# 3
Each drive connects
to a port on the hub.
RS485/422
RS485/422
RS232
Speed1/Speed2 (Toggle Switch)
RS485
Speed (Potentiometer)
RS485/422
RS485/422
RS485/422
RS485/422
RS485/422
RS485/422
RS485/422
UP TO
UP TO
UP TO
UP TO
AXES
AXES
AXES
AXES
8
8
4
4
Speed (Potentiometer)
ID 1
ID 1
# 1
# 1
RS232
RS232
# 1
# 1
RS485/422
RS485/422
RS485/422
UP TO
UP TO
AXES
AXES
8
4
ID 1
# 1
# 1
or
or
RS232
Run/Stop (Toggle Switch)
ID 2
# 2
3rd Party Controller
RS232
# 2
UP TO
32
UP TO
32
UP TO
32
UP TO
32
AXES
AXES
AXES
AXES
or
127
127
C
UP TO
AXES
UP TO
AXES
UP TO
32
UP TO
32
Run/Stop (Toggle Switch)
AXES
AXES
RS232
Speed1/Speed2 (Toggle Switch)
3rd Party Controller
RS485
127
UP TO
AXES
RS485/422
RS232
Speed (Potentiometer)
Speed1/Speed2 (Toggle Switch)
RS485
RS232
RS232
UP TO
AXES
UP TO
AXES
RS232
8
4
ID 1
# 1
# 1
RS232
Speed (Potentiometer)
or
UP TO
UP TO
AXES
AXES
8
4
UP TO
32
AXES
UP TO
32
AXES
RS232
127
UP TO
AXES
▪
▪
▪
▪
RS-232 Model
▪
RS-485 Model
▪
▪
C
CANopen Model
▪
▪
▪
▪
▪
▪
▪
▪
▪
or
Q
Software configuration
Two speeds
Vary speed with analog input
Joystick compatible
Accepts serial commands from
host PC or PLC
Accepts serial commands from
host PC or PLC
Multi-axis capable
Connect to CANopen network
DS301 and DSP402 protocols
Comprehensive text based language
Download, store & execute programs
High level features: multi-tasking,
conditional programming,
& math functions
Host interface while executing
internal programs
Step & Direction
CW & CCW Pulse
A/B Quadrature (Master
Encoder)
RS232
RS232
RS232
RS232
RS232
RS232
RS232
RS232
RS232
RS232
RS232
RS