CV500-MC421 Omron, CV500-MC421 Datasheet
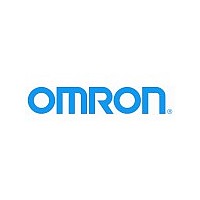
CV500-MC421
Specifications of CV500-MC421
Available stocks
Related parts for CV500-MC421
CV500-MC421 Summary of contents
Page 1
... Reverse compiling and reverse assembly of this product is strictly prohibited. 7. Transfer, exchange, or loan of this product in whole or in part to a third party is strict- ly prohibited. 8. OMRON will not be held responsible for any consequences resulting from the use of this manual or attached disk. 9. MS-DOS is a registered trademark of Microsoft Corporation. ...
Page 2
Instruction Manual OMNUC U Computer Monitor Software (Version 1.1) SERIES Servo Driver ...
Page 3
Safety Precautions Starting Up Multiple Axis Communications Caution Make sure not to duplicate the Unit No. of Drivers when setting up. Starting communications with you computer with duplicate Unit Nos. may result in damage to Drivers and/or the com- puter. ...
Page 4
...
Page 5
1 ...
Page 6
Functions OMNUC U-series Computer Monitor Software is a program which easily carries out the following functions on a IBM PC/AT or compatible computer: Parameter editing Jog operation and auto tuning Checking the condition of Servo Drivers Displaying graphs related ...
Page 7
Parameters (Setup Parameter & User Parameter) edited on a IBM PC/AT or compatible can be transferred to Servo Drivers. Parameters set in Servo Drivers can be read from the IBM PC/AT or compatible. Parameters edited on the ...
Page 8
Monitors speed feedback and torque commands. Displaying Graphs Related to Speed and Torque (HA/LA, UT, UE) Torque Command ([%]) Speed Feedback ([r/min]) I/0 [Esc] Key [Print Screen] Key Retrieves and displays time-related data such as torque commands, speed ...
Page 9
... Parameter Files Corresponding to an OMRON Position Control Unit (H/L, HA/LA, UT, UE) Parameter files have been developed for the exclusive use for the connection of SYSMAC C-series Position Control Units, Motion Control Units, and Servo Drivers. Parameter setup can be easily per- formed by just selecting the appropriate file and editing it. ...
Page 10
System Configuration The OMNUC U-series Computer Monitor Software will operate on a IBM PC/AT or com- patible computer (IBM DOS 3.30 or higher) System Configuration Computer IBM PC/AT or compatible computer Use an i486SX CPU or higher. One ...
Page 11
... Make sure that the cable length is no longer than 30 m. 17LE-13090-27(D2BC) (Optec Dai-Ichi Denko Co., Ltd. (DDK)) 9-pin D-sub Connector Connect to CN3 XM2A-0901 Soldered Plug (OMRON) XM2S-0912 Cover (OMRON) 17JE-23090-02(D1) (Optec Dai-Ichi Denko Co., Ltd. (DDK)) 17JE-09H-15 (Optec Dai-Ichi Denko Co., Ltd. (DDK)) Servo Driver (CN3) Shield Case FG ...
Page 12
Connecting to More than One Servo Driver (Connecting Directly to RS-232C Ports) IBM PC/AT or compatible (RS-232C) FG case Make sure that the cable length is no longer than 2 m. Driver (CN3) Case FG Shield Case FG To next ...
Page 13
Connecting to More than One Servo Driver (Connecting to RS-422A Converter Ports) Converter (RS-422A) Short-circuit the RTI (termination resis- tance inserted) and the RT2 (termina- tion resistance not inserted) of the last Servo Driver. When connecting to the RS-422A converter ...
Page 14
2 ...
Page 15
This chapter provides instructions for installing the OMNUC U-series Computer Monitor Software on an IBM PC/AT or compatible’s hard disk. 2-1 Installation on a IBM PC/AT or Compatible Before Installation If the hard disk has not been formatted yet, ...
Page 16
List of Files for Installation File name UMON.EXE Computer Monitor Software (Main File) UAL.TBL R88D-UA UPL.TBL R88D-UP UALA.TBL R88D-UP UPLA.TBL R88D-UP UTH.TBL R88D-UT UTW.TBL R88D-UT UEP.TBL R88D-UEP MOTOR.TBL Servo Motor Information Table File ATT.BGI Graphic Driver CGA.BGI Graphic Driver DOSVGA.BGI ...
Page 17
3 ...
Page 18
This chapter explains the basic operating methods for the OMNUC U-series Computer Monitor Software. 3-1 Mouse Operations Description and Methods of Mouse Operation Descriptions Click Press the button and release it quickly Double-click Press the button twice quickly Drag Move ...
Page 19
Keyboard Operations Descriptions and Functions of Keyboard Operations Descriptions While pressing the Alt Key, press the X Key. + ALT X Press the Return Key. Press the Space Key. SPACE Press the keys as listed ...
Page 20
Function Selection The functions of the Computer Monitor Software are displayed on a bar on the upper part of the screen. This is called the Menu Bar. Each menu provides a Pull-Down Menu menu is selected from ...
Page 21
Function Selection Using Keyboard Function selection using the keyboard is shown in the flowchart below. Note If a window is already open, press the Escape Key to close the window and then select a function. This is not required when ...
Page 22
Function Key Allocation Function keys are allocated to provide shortcuts for quick operation. Keys SHIFT SHIFT F6 + ALT SHIFT F10 Functions allocated Monitor ...
Page 23
4 ...
Page 24
Following Chapter 2 Installation , this chapter describes how to start and quit the Com- puter Monitor Software installed on an IBM PC/AT or compatible. The Computer Monitor Software has two modes. On line mode: The Servo Driver is connected ...
Page 25
Type the Start Command The Computer Monitor Software’s start command is UMON About the Start Option The UMON command has the following start option. When using a notebook personal computer with a black and white CRT, add ...
Page 26
Start Screen Operation 1. Select the Servo Driver Type Select the Servo Driver model connected ( connected) to the IBM PC/AT or compatible. Click on the selected Servo Driver model. Select [Servo Driver Type] using the Tab ...
Page 27
Quit Procedure Click [Quit]. Select [ ] -- [Quit] using the Tab Key or press the Alt+X Keys. This quits the Computer Monitor Software and returns to the DOS prompt or returns to the Menu ...
Page 28
5 ...
Page 29
This chapter describes the basic operations of the Computer Monitor Software in on line mode. The following explains each of these operations. The chapter concludes with a description of the off line edit mode. The screens used in this chapter ...
Page 30
Function Tree The following tree diagram provides a summary of Computer Monitor Software func- tions. Menu Bar Monitor Parameter Alarm Jog AutoTuning Adjust Graph Selection [ ] System Monitor Monitor Parameter Alarm Jog Auto Tuning Adjust Graph Selection Version ...
Page 31
System Monitor Version 1. Software Version Window Click on or select [ ] -- 2. Closing Software Version Window Click on [OK] or the [ ] in the upper-left part of the window. Press Space Key, Return Key, ...
Page 32
Change Directory Use one of the following two methods. Entering the Directory Name Directly Type the directory name in the [Directory Name] field and press the Return Key. This operation will change the directory and close the Change Directory ...
Page 33
Monitor Function Selecting the Servo Driver from the screen automatically displays the Monitor Display screen. The following explains how to use the four screens (on line mode). For informa- tion on each monitor, refer to the appropriate product operation ...
Page 34
Displaying the Window The following operation will re-display a window that has been removed from the screen. Displaying a Monitor Window Click on or select [Monitor] -- [Monitor]. All windows will be displayed. Chapter 5 ...
Page 35
... In parameter settings, each user parameter can be changed in real-time through such functions as parameter edit, parameter transfer to disk or Servo Driver, and parameter comparison check. When connected to an OMRON Position Control Unit, use the exist- ing Position Control Unit-compatible parameter files to speed-up the setting operation. ...
Page 36
The Edit Setup Parameter window opens. 3. Setting Each Bit to 0 or1 The setup parameter sets each bit and [X] indicate 0 and 1 settings respectively. For more information on ...
Page 37
Editing User Parameter Numbers from Cn-03 1. Opening the User Parameter Window Click on or select [Parameter] -- [User Parameter]. Note This operation is not necessary if the window is already open after setting the setup parameter. 2. Selecting the ...
Page 38
Transferring Parameters between IBM PC/AT or Compatible and Disk This section explains how to save the parameters recorded in IBM PC/AT or compatible memory to disk. This section also explains how to read the disk’s parameter files to the ...
Page 39
Typing Over an Existing File Double-click on a file name in the [Save File List]. Select [Save File List] using the Tab Key. Select the file name using the Up and Down Cursor Key and press the Return Key. Parameters ...
Page 40
... Select [PC Drive] using the Tab Key. Press the Space Key or Return Key. Applicable Position Control Unit H/L C500-NC222-E, CV500-MC221/MC421 H/L C200H-NC112/NC211 3G2A5-NC111-EV1 HA/LA C500-NC222-E, OMNUC N115/N116, OMNUC U43/U45 CV500-MC221/MC421 HA/LA C200H-NC112/NC211, 3G2A5-NC111-EV1 C200H-NC112/NC211, 3G2A5-NC111-EV1 C500-NC222-E, CV500-MC221/MC421 C200H-NC112/NC211, 3G2A5-NC111-EV1 C500-NC222-E, CV500-MC221/MC421 H/L C200H-NC112/NC211, 3G2A5-NC111-EV1 Chapter 5 ...
Page 41
Parameter Download window opens. 3. Selecting [Start] Click on [Start]. Select [Start] using the Tab Key. Press the Space Key or Return Key. Parameters are transferred to Servo Driver, Parameter Download window closes, and program re- turns to the User ...
Page 42
Select [PC Drive] using the Tab Key. Press the Space Key or Return Key. Parameter Upload window opens. 3. Selecting [Start] Click on [Start]. Select [Start] using the Tab Key. Press the Space Key or Return Key. Parameters are transferred ...
Page 43
Comparison of User Parameter window opens 3. Selecting [Start] Click on [Start]. Select [Start] using the Tab Key. Press the Space Key or Return Key. The message ”Verifying Parameter...Cn- Result of comparison: All in agreement Information window opens. Click on ...
Page 44
Information Window opens. The number of user parameters not in conformity is indicated. Click on [OK]. Press the Space Key or Return Key. The Information window closes, the User Parameter Window appears, and the number of user pa- rameters not ...
Page 45
Clearing Parameters This section describes how to clear all parameters stored in the IBM PC/AT or compatible memory (or revert to a “no setting entered” condition). 1. Opening the User Parameter Window Click on or select [Parameter] -- [User ...
Page 46
Sample Parameter Printout 5-5-7 Adjusting Parameters The user can make real-time changes in each user parameter. Therefore, the user parameter can be edited as if the R88A-PR02U or R88A-PR03U Parameter Unit was being used. Adjusting Parameters 1. Opening the User ...
Page 47
User Parameter Adjustment window opens. 2. Selecting the User Parameter Click on [Select]. The User Parameter Select window opens. Double-click on the user parameter item to be set. The User Parameter Adjustment window appears again. Select [Select] using the Tab ...
Page 48
Precautions for Parameter Adjustment Some user parameters are not enabled unless the Servo Driver is turned off and on after they are set. If the settings in such parameters are changed, turn off the Servo Driver, check that all indicators ...
Page 49
Alarm Display By selecting [Alarm] -- [Alarm], the user can check present and past alarm conditions. It also enables the user to reset a present alarm as well as clear past alarm records. Should an A.81 or A.82 alarm ...
Page 50
Jog Operation Jog speed enables normal or reverse motor rotation. Operating Jog 1. Opening the Jog Operation Window Click on or select [Jog] -- [Jog Operation]. Jog Operation window opens. 2. Selecting [Servo On] (See note 1.) Click on ...
Page 51
Note 2. Even when bit No the set up parameter No set to “1,” the [Servo Off] switch is valid. However, the Servo Driver will turn back ON if the Jog Operation window is closed. When ...
Page 52
Auto Tuning Auto tuning automatically adjusts the Servo System Gain according to set values of me- chanical rigidity. Auto Tuning 1. Opening the Auto Tuning Window Click on or select [Auto Tuning] -- [Auto Tuning]. Auto Tuning window opens. ...
Page 53
Setting the Mechanical Rigidity Click on the desired mechanical rigidity setting. Click on [OK]. Select the [Mechanical Rigidity] list using the Tab Key. Select the mechanical rigidity using the Up and Down Cursor Keys, then press the Return Key. ...
Page 54
Select [Forward] or [Reverse] position using the Tab Key. 8. Carrying out Auto Tuning Keep pressing the mouse button over [Forward] or [Reverse]. When auto tuning is complete, the [Mode] column will display [Auto Tuning ..... Complete]. When [Complete] is ...
Page 55
Adjustment Adjustment is used for analog input. This function is not used for pulse-train inputs. Adjustment can be used for the following models. Speed Command Automatic Zero Adjustment Speed Command Manual Zero Adjustment 12 bit Absolute Encoder Set Up ...
Page 56
Speed Command Manual Zero Adjustment window opens. 2. Turning the Servo ON Input the Run signal (ON). When bit No setup parameter No set to “1,” this operation is not required. 3. Setting the Voltage ...
Page 57
Absolute Encoder Setup Method This function is used to reset alarms (A.81, A.82) relating to the Absolute Encoder. In addition valid when the following conditions are met. Servo Driver model is R88-UA Starting of the Computer ...
Page 58
Select [Continue] Click on [Continue]. Press the Space Key or Return Key. [Alarm Reset ..... Stand-by] is displayed. 3. Select [Start] Click on [Start]. Press the Space Key or Return Key. [Alarm Reset ..... Resetting] is displayed. [Alarm Reset ...
Page 59
Graph This function retrieves and displays time series data such as torque command, speed command, speed feedback, and position deviation. This function retrieves and displays the ON/OFF status of I/O signals as time series data. It enables the storage ...
Page 60
Select [Graph] using the Tab Key. Press the Space Key or Return Key. The Selection of Graph window opens. Select [Graph 1] using the Tab Key, then select the data using Up and Down Cursor Keys. Select [Graph 2] using ...
Page 61
Select [Trigger Condition] using the Tab Key and type its numerical value. Select the [Edge Type] list using the Tab Key and select an edge type using the Up and Down Cursor Keys. Select [OK] using the Tab Key, then ...
Page 62
When I/O is Used as Trigger The Trigger Condition Setting window for I/O opens. Click on the I used as trigger. Click on one from among the [Edge Type]. Click on [OK]. Trigger Condition Setting window for ...
Page 63
Setting the Pretrigger (If there is no need to set Pretrigger the next step, Starting the Trace .) Pretrigger setting sets how much data stored prior to the trigger. Click on [Pretrigger]. The ...
Page 64
Graph is displayed print this graph, press the Print Screen Key of the IBM PC/AT or compatible. 8. Exiting the Graph Display Press the Escape Key You Want to Save the Data Graph? a) Select ...
Page 65
Selecting the Trace Buffer Click on [Buffer]. The Graph Buffer Load window opens. Double-click on the file name of the data to be displayed (or after clicking on the file name, click on [PC Disk]). Data is read from ...
Page 66
Graph is displayed. Torque Command ([%]) Speed Feedback ([r/min]) I/0 [Esc] Key [Print Screen] Key To print this graph, press the Print Screen Key of the IBM PC/AT or compatible. 5. Exiting the Graph Display Press the Escape ...
Page 67
Servo Driver Selection The Servo Driver, set when the Computer Monitor Software was started, can be changed. 1. Opening the Servo Driver Selection window Click on or select [Selection] -- [Servo Driver Selection]. The Servo Driver Selection window opens. ...
Page 68
When the power supply of the Servo Driver has been turned ON, but the Servo Driver type does not match, an error message is displayed. The Servo Driver type is not discriminated between the R88D-UA and the Servo ...
Page 69
Off Line Edit Off line edit is used for editing U-series parameters or creating a Re Display Graph under condition that the power supply of Servo Driver is OFF or that the Servo Driver is not connected to an ...
Page 70
Performing the Off Line Edit Functions which can be used for the off line edit are shown below: Parameter Setting Editing Parameters Transferring Parameters (Between IBM PC/AT or Compatible and Disk) Clearing Parameters Printing Parameters Re Display ...
Page 71
6 ...
Page 72
Error information is displayed when there is a mistake in selecting an item or when com- munications abnormalities occur. Since error information appears in various circumstances, take the necessary mea- sures according to the displayed content. Typical error information is ...