A3981KLPTR-T Allegro Microsystems Inc, A3981KLPTR-T Datasheet - Page 12
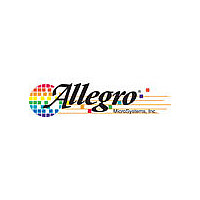
A3981KLPTR-T
Manufacturer Part Number
A3981KLPTR-T
Description
AUTOMOTIVE PROGRAMMABLE STEPPER DRVR
Manufacturer
Allegro Microsystems Inc
Datasheet
1.A3981KLPTR-T.pdf
(42 pages)
Specifications of A3981KLPTR-T
Applications
Stepper Motor Driver, 2 Phase
Number Of Outputs
1
Voltage - Load
7 V ~ 28 V
Voltage - Supply
3 V ~ 5.5 V
Operating Temperature
-40°C ~ 150°C
Mounting Type
Surface Mount
Package / Case
28-TSSOP (0.173", 4.40mm Width) Exposed Pad
Lead Free Status / RoHS Status
Lead free / RoHS Compliant
Current - Output
-
Lead Free Status / RoHS Status
Lead free / RoHS Compliant
Available stocks
Company
Part Number
Manufacturer
Quantity
Price
Part Number:
A3981KLPTR-T
Manufacturer:
ALLEGRO/雅丽高
Quantity:
20 000
A3981
Hot Warning If the chip temperature rises above the Hot Tem-
perature Warning Threshold, T
the Hot Warning bits will be set in the diagnostic registers. No
action will be taken by the A3981. When the temperature drops
below the Hot Temperature Warning Threshold, the Fault flag
will go high but the Hot Warning bits remain set in the diagnostic
registers until reset.
Cold Warning If the chip temperature falls below the Cold
Temperature Warning Threshold, T
and the Cold Warning bits will be set in the diagnostic registers.
No action will be taken by the A3981. When the temperature rises
above the Cold Temperature Warning Threshold, the Fault flag
will go high but the Cold Warning bits remain set in the diagnos-
tic registers until reset.
Overtemperature Shutdown If the chip temperature rises
above the Overtemperature Shutdown Threshold, T
flag will go low and the Thermal Shutdown bits will be set in the
diagnostic registers. The A3981 will disable the outputs to try to
prevent a further increase in the chip temperature. When the tem-
perature drops below the Overtemperature Shutdown Threshold,
the Fault flag will go high but the Thermal Shutdown bits remain
set in the diagnostic registers until reset.
Bridge and Output Diagnostics
The A3981 includes monitors that can detect a short to supply or
a short to ground at the motor phase connections. These condi-
tions are detected by monitoring the current from the motor
phase connections through the bridge to the motor supply and to
ground.
Low current comparators and timers are provided to help detect
possible open load conditions.
Short to Supply A short from any of the motor connections to
the motor supply (VBBA or VBBB) is detected by monitoring the
voltage across the low-side current sense resistor in each bridge.
This gives a direct measurement of the current through the low
side of the bridge.
When a low-side FET is in the On state, the voltage across the
sense resistor, under normal operating conditions, should never
be more than the Maximum Sense Voltage, V
an overcurrent is determined to exist when the voltage across the
sense resistor exceeds the Low-Side Overcurrent Sense Voltage,
V
ously present for at least the Overcurrent Fault Delay, t
before the short fault is confirmed by setting the relevant bit in
OCL
, typically 2 × V
SMAX
. This overcurrent must be continu-
JWH
, the Fault flag will go low and
JWC
, the Fault flag will go low
SMAX
. In this state,
Automotive, Programmable Stepper Driver
JF
, the Fault
SCT
,
FAULT0 and driving the DIAG output low if the Fault Output
flag is selected. The output is switched off and remains off until a
fault reset occurs.
Note that the sense resistor cannot distinguish which low-side
FET is in an overcurrent state. So, if more than one low-side FET
is active when the fault is detected, for example during low-side
recirculation with synchronous rectification, then the shorted con-
nection is determined from the internal PWM state.
The actual overcurrent that V
value of the sense resistor and is typically 2 × I
Short to Ground A short from any of the motor connections
to ground is detected by directly monitoring the current through
each of the high-side FETs in each bridge.
When a high-side FET is in the On state the maximum current
is typically always less than 1 A. In this state, an overcurrent is
determined to exist when the current through the active high-side
FET exceeds the High-Side Overcurrent Threshold, I
This overcurrent must be present for at least the Overcurrent
Fault Delay, t
the relevant bit in FAULT0 and driving the DIAG output low if
the Fault Output flag is selected. The output is switched off and
remains off until a fault reset occurs.
Note that when a short to ground is present the current through
the high-side FET is limited to the High-Side Current Limit,
I
large negative transients at the phase output pins when the out-
puts are switched off.
Shorted Load A short across the load is indicated by concurrent
short faults on both high side and low side.
Short Fault Blanking All overcurrent conditions are ignored
for the duration of the Overcurrent Fault Delay, t
detection delay timer is started when an overcurrent first occurs.
If the overcurrent is still present at the end of the short detection
delay time then a short fault will be generated and latched. If the
overcurrent goes away before the short detection delay time is
complete, then the timer is reset and no fault is generated.
This prevents false short detection caused by supply and load
transients. It also prevents false short detections resulting from
current transients generated by the motor or wiring capacitance
when a FET is first switched on.
Short Fault Reset and Retry When a short circuit has been
detected all outputs for the faulty phase are disabled until the
LIMH
, during the Overcurrent Fault Delay, t
SCT
, before the short fault is confirmed by setting
115 Northeast Cutoff
1.508.853.5000; www.allegromicro.com
Allegro MicroSystems, Inc.
Worcester, Massachusetts 01615-0036 U.S.A.
OCL
represents is determined by the
SCT
SMAX
. This prevents
SCT
. The short
.
OCH
.
12