A3981KLPTR-T Allegro Microsystems Inc, A3981KLPTR-T Datasheet - Page 36
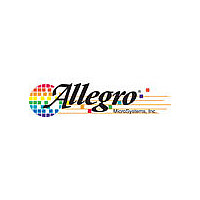
A3981KLPTR-T
Manufacturer Part Number
A3981KLPTR-T
Description
AUTOMOTIVE PROGRAMMABLE STEPPER DRVR
Manufacturer
Allegro Microsystems Inc
Datasheet
1.A3981KLPTR-T.pdf
(42 pages)
Specifications of A3981KLPTR-T
Applications
Stepper Motor Driver, 2 Phase
Number Of Outputs
1
Voltage - Load
7 V ~ 28 V
Voltage - Supply
3 V ~ 5.5 V
Operating Temperature
-40°C ~ 150°C
Mounting Type
Surface Mount
Package / Case
28-TSSOP (0.173", 4.40mm Width) Exposed Pad
Lead Free Status / RoHS Status
Lead free / RoHS Compliant
Current - Output
-
Lead Free Status / RoHS Status
Lead free / RoHS Compliant
Available stocks
Company
Part Number
Manufacturer
Quantity
Price
Part Number:
A3981KLPTR-T
Manufacturer:
ALLEGRO/雅丽高
Quantity:
20 000
A3981
In the next panel, panel (b), the current is flowing down through
the phase B winding from top to bottom and there is no current
in phase A. The result is an N pole on the B electromagnets and
an S pole on the B-bar electromagnets. These magnetic poles will
attract and repel the permanent magnets on the rotor producing a
force that moves the rotor from left to right in the diagram until
the poles of the permanent magnets again align with the poles of
the electromagnets.
In panel (c), the current is flowing up through the phase A wind-
ing from bottom to top and there is no current in phase B. This
reverses the pole orientation from the top panel, such that there
is an S pole on the A electromagnets and an N pole on the A-bar
electromagnets. As before, these magnetic poles will attract and
repel the permanent magnets on the rotor producing a force that
moves the rotor from left to right in the diagram, until poles of
the permanent magnets again align with the poles of the electro-
magnets.
The bottom panel, panel (d), shows the final combination with
current flowing up through the phase B winding from bottom to
top and there is no current in phase A. This produces an N pole
on the B electromagnets and a S pole on the B-bar electromag-
nets. As before, these magnetic poles will attract and repel the
permanent magnets on the rotor producing a force that moves the
rotor from left to right until poles of the permanent magnets again
align with the poles of the electromagnets.
Each of the four steps in figure A1 represents a single full
mechanical step of the stepper motor. The four steps together
represent a single electrical cycle.
The step resolution depends entirely on the mechanical construc-
tion of the motor and typically there will be 200 or more full
steps per mechanical revolution of the motor. A 200-step motor
will provide a resolution of 360 / 200 = 1.8° of rotation per step.
Stepping in the opposite direction to that described above is sim-
ply a case of changing the step sequence or inverting one of the
phase current directions.
Microstepping
In many applications it is necessary to improve the resolution of
the stepper motor, for more precise positioning control, or simply
to increase the number of steps per revolution to reduce the
torque ripple and therefore the vibration and noise of the motor.
Fortunately this can be achieved by driving both phases at the
same time in order to move the rotor to a position between two
electromagnets. This is known generically as microstepping.
Automotive, Programmable Stepper Driver
Figure A2 shows the basic principle of microstepping. Panels (a)
and (c) of figure A2 correspond to panels (a) and (b) of figure
A1. Panel (b) shows each phase energized such that there are now
two adjacent N poles and two adjacent S poles. In this example
the currents in both phases is the same, and so the S and N poles
of the rotor now move to half way between the positions in
diagrams (a) and (c). Figure A2 only shows a single mechanical
step in total, which is one quarter of a full electrical cycle. This
sequence is the lowest resolution form of microstepping, known
as half step, and is the simplest method of driving a stepper motor
in half-step mode.
The currents are switched-on in the correct direction in sequence
and no current control is required. The current is simply defined,
Figure A2. Half step operation
N
A
N
S
N
A
A
N
S
N
N
N
N
B
B
B
S
Stator
Stator
Stator
Rotor
A
S
N
S
A
A
_
_
_
S
Rotor
N
S
Rotor
N
_
B
_
B
S
_
B
S
S
A
N
S
N
A
A
N
115 Northeast Cutoff
1.508.853.5000; www.allegromicro.com
Allegro MicroSystems, Inc.
Worcester, Massachusetts 01615-0036 U.S.A.
S
N
A
A
A
B
B
B
(a) Same as
(b) Half-step
(c) Same as
figure A1(a)
position
figure A1(b)
36