R88A-CAGA005BR Omron, R88A-CAGA005BR Datasheet - Page 6
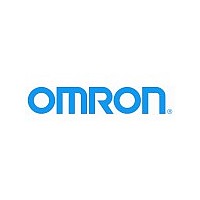
R88A-CAGA005BR
Manufacturer Part Number
R88A-CAGA005BR
Description
5M High Flex Motor Brake Cable
Manufacturer
Omron
Datasheet
1.XW2Z-100J-A28.pdf
(52 pages)
Specifications of R88A-CAGA005BR
Lead Free Status / Rohs Status
Lead free / RoHS Compliant
6
SMARTSTEP2: Selection Guide
The optimum combination can be found from
to handle various applications.
Selection Guide
Interface
Torque
control
Pulse
GAIN
train
FIT
Pulse train:
The speed and travel
distance are input to the
Servo as pulse trains.
Torque control:
adjust the rotational force. Torque control
is suitable for applications such as parts
insertion, pressing, and screw tightening.
Fit gain:
autotuning for position control is set
automatically. By repeatedly inputting
a specific operation pattern, the
optimum rigidity is set automatically.
AC100V
AC200V
AC100V
AC200V
Command type
Control modes
Control mode switching
Vibration control
Autotuning
Realtime autotuning
Torque limits
Encoder output
Internal set speeds
The rigidity for the realtime
Control is applied to
Single-phase
Single/
Three-phase
Three-phase
Analog
Analog:
The speed and torque
are input to the Servo
as analog signals.
ABS
Single-phase
kW
2
switching
Mode
Absolute output:
power supply is turned ON, the Controller
reads the Servo absolute position data to
restore the absolute position.
750
50
50
W
W
W
kW
3
Position
control
Command control mode switching:
Switching is possible between any two of
the three control modes: position control,
speed control, and torque control.
kW
Pulse
GAIN
4
train
ABS
100
100
900
FIT
Single-phase
Three-phase
W
W
W
Single/
Speed
control
switching
Torque
speeds
Vibration
control
AUTO
Mode
limit
4.5
kW
When the Controller
ML2
8
Analog
Adaptive
filter
200
200
kW
INC
W
W
*1
*1
1
kW
5
ML2:
high-speed Servo
communications motion
network.
Torque
control
*2
Three-phase
MECHATROLINK-II
kW
*1. Two limits.
6
(See note.)
400
400
1.5
kW
W
W
7.5
kW
INC
Incremental output:
the Controller power supply is
turned ON, operation is always
started from the origin point.
Single-phase
kW
2
*2. One adaptive filter and two notch filters.
control
Position
Vibration
control
750
50
50
W
W
W
kW
3
control
Position
Position control:
applied to move to the target
position and then stop at the
target position.
Vibration control function:
Vibration is suppressed by
automatically setting a filter for
the vibration frequency.
kW
4
100
100
900
ABS
Single-phase
Three-phase
W
W
W
When
Single/
Speed
control
switching
Vibration
Adaptive
Torque
Mode
control
AUTO
ML2
filter
limit
4.5
kW
Adaptive
200
200
INC
kW
filter
W
W
*1
*2
*1
1
kW
5
Control is
Torque
control
Three-phase
Adaptive filter:
load inertia is calculated in
realtime and the result is used to
automatically set the optimum gain.
kW
6
400
400
1.5
kW
W
W
7.5
kW
Speed
control
AUTO
The machine
Single-phase
*3. One adaptive filter and one notch filter.
Autotuning:
command pattern automatically generated by the Servo
Drive, then estimates the load inertia from the torque
required at that time to automatically set the optimum gain.
Speed control:
or rotational speed. For example, speed control is used
for applications such as turning grindstones, controlling
welding speeds, and controlling feeding speeds.
50
50
W
W
Torque
limit
The motor is moved according to a
Single-phase
Three-phase
Control is applied to change the linear
Single/
Position
control
Adaptive
Torque
speeds
Vibration
control
AUTO
Pulse
filter
limit
train
100
200
100
200
INC
Torque limit:
possible between the first torque
limit and the second torque limit to
limit the Servomotor output torque.
W
W
W
W
4
*3
*1
400
200
W
W
Three-phase
Switching is