R88M-G1K020T-BS2 Omron, R88M-G1K020T-BS2 Datasheet - Page 131
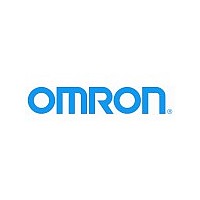
R88M-G1K020T-BS2
Manufacturer Part Number
R88M-G1K020T-BS2
Description
1KW 2KRPM ABS B KEY G-SrvMtr
Manufacturer
Omron
Datasheet
1.XW2Z-050J-A31.pdf
(159 pages)
Specifications of R88M-G1K020T-BS2
Lead Free Status / Rohs Status
Lead free / RoHS Compliant
Parameter
134
Default Display
Torque Limit Selection
Drive Prohibit Input
Selection
Communications Control
Power ON Address
Display Duration Setting
Speed Monitor (SP)
Selection
Torque Monitor (IM)
Selection
Prohibit Parameter
Changes via Network
Operation Switch When
Using Absolute Encoder
RS-232 Baud Rate
Setting
Position Loop Gain (RT)
Speed Loop Gain (RT)
Speed Loop Integration
Time Constant (RT)
Speed Feedback Filter
Time Constant (RT)
Torque Command Filter
Time Constant (RT)
Speed Feed-forward
Amount (RT)
Feed-forward Filter Time
Constant (RT)
Position Loop Gain 2
(RT)
Speed Loop Gain 2 (RT)
Speed Loop Integration
Time Constant 2 (RT)
Speed Feedback Filter
Time Constant 2 (RT)
Torque Command Filter
Time Constant 2 (RT)
R88A-RP02G : Parameter Unit Part Names
Servo Parameters
Parameter name
8.8.8.8.8.8.
8.8
OMNUC G-series AC Servomotors/Servo Drives with Built-in MECHATROLINK-II Communications
Selects the data to be displayed on the 7-
segment LED display on the front panel.
Selects the torque limit function, or the torque
feed-forward function during speed control.
Selects the function for the Forward and Reverse
Drive Prohibit Inputs (CN1 POT: pin 19, NOT: pin
20).
Controls errors and warnings for
MECHATROLINK-II communications.
Sets the duration to display the node address
when the control power is turned ON.
Selects the output to the Analog Speed Monitor
(SP on the front panel).
Selects the output to the Analog Torque Monitor
(IM on the front panel).
Allows/prohibits parameter changes via the
network.
Selects how the absolute encoder is used.
Sets the baud rate for RS-232 communications.
Sets the position loop responsiveness.
Sets the speed loop responsiveness.
Adjusts the speed loop integration time constant.
Sets the type of speed detection filter time
constant. Normally, use a setting of 0.
Adjusts the first-order lag filter time constant for
the torque command section.
Sets the speed feed-forward amount.
Sets the time constant for the speed feed-
forward first-order lag filter.
Sets the position loop gain when using gain 2
switching.
Sets the speed loop gain when using gain 2
switching.
Sets the speed loop integration time constant
when using gain 2 switching.
Sets the speed detection filter when using gain 2
switching.
Sets the first-order lag filter time constant for the
torque command section when using gain 2
switching.
LED Display (6 Digits)
Unit No. Display (2 Digits)
Increment/Decrement Key
Mode Key
Shift Key
Data Key
If an error occurs, all digits will flash and the
display will switch to the error display.
Displays the parameter type (servo, 16 bit, or
32 bit).
In Parameter Setting Mode, displays the
2-digit parameter number.
Switches between the following six modes.
• Monitor Mode
• Parameter Setting Mode • Auxiliary Function Mode
• Parameter Write Mode • Copy Mode
Increases or decreases parameter numbers
or set values.
Shifts the digit being changed to the left.
Switches between the parameter and setting
displays, saves settings, etc.
Explanation
• Normal mode autotuning
Notch Filter 1 Frequency
Notch Filter 1 Width
Inertia Ratio (RT)
Realtime Autotuning
Mode Selection
Realtime Autotuning
Machine Rigidity
Selection
Adaptive Filter Selection
Vibration Filter Selection
Normal Mode Autotuning
Operation Setting
Overrun Limit Setting
Instantaneous Speed
Observer Setting (RT)
Notch Filter 2 Frequency
Notch Filter 2 Width
Notch Filter 2 Depth
Vibration Frequency 1
Vibration Filter 1 Setting
Vibration Frequency 2
Vibration Filter 2 Setting
Adaptive Filter Table
Number Display
Gain Switching Operating
Mode Selection (RT)
Gain Switch Setting (RT)
Gain Switch Time (RT)
Gain Switch Level Setting
(RT)
Gain Switch Hysteresis
Setting (RT)
Position Loop Gain
Switching Time (RT)
Jog Speed
Emergency Stop Input
Setting
Origin Proximity Input
Logic Setting
Parameter name
Sets the notch frequency of notch filter 1 for
resonance suppression.
Selects the notch width of notch filter 1 for
resonance suppression.
Selects the load inertia as a percentage of the
Servomotor rotor inertia.
Sets the operating mode for realtime autotuning.
Sets the machine rigidity for realtime autotuning.
Enables or disables the adaptive filter.
Selects the vibration filter type and the switching
mode.
Sets the operating pattern for normal mode
autotuning.
Sets the Servomotor’s allowable operating range
for the position command input range.
The Instantaneous Speed Observer improves
speed detection accuracy, thereby improving
responsiveness and reducing vibration when
stopping.
Sets the notch frequency of notch filter 2 for
resonance suppression.
Selects the notch width of notch filter 2 for
resonance suppression.
Selects the notch depth of notch filter 2 for
resonance suppression.
Sets the vibration frequency 1 for damping
control to suppress vibration at the end of the
load.
When setting Vibration Frequency 1 (Pn02B),
reduce this setting if torque saturation occurs, or
increase it to make the movement faster.
Sets the vibration frequency 2 for damping
control to suppress vibration at the end of the
load.
Sets vibration filter 2 for damping control to
suppress vibration at the end of the load.
Displays the table entry number corresponding
to the frequency of the adaptive filter.
Enables or disables gain switching.
Sets the trigger for gain switching.
The details depend on the control mode.
Enabled when the Gain Switch Setting (Pn031)
is set to 3, or 5 to 10. Sets the lag time from the
trigger detection to actual gain switching when
switching from gain 2 to gain 1.
Sets the judgment level to switch between Gain
1 and Gain 2 when the Gain Switch Setting
(Pn031) is set to 3, 5, 6, 9, or 10. The unit for the
setting depends on the condition set in the Gain
Switch Setting (Pn031).
Sets the hysteresis of the judgment level for the
Gain Switch Level Setting (Pn033) when the
Gain Switch Setting (Pn031) is set to 3, 5, 6, 9,
or 10.
The unit for the setting depends on the condition
set for the Gain Switch Setting (Pn031).
This parameter can prevent the position loop
gain from increasing suddenly when the position
loop gain and position loop gain 2 differ by a
large amount.
Sets the jog operation speed with the Parameter
Unit or CX-Drive.
Enables the Emergency Stop Input (STOP).
Sets the logic for the Origin Proximity Input
(DEC).
R88M-G/R88D-GN@-ML2
Explanation