SC1401 Semtech Corporation, SC1401 Datasheet - Page 12
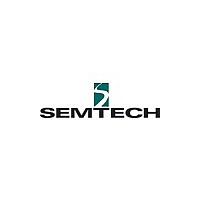
SC1401
Manufacturer Part Number
SC1401
Description
HIGH PERFORMANCE SYNCHRONOUS BUCK CONTROLLER WITH LDO FOR PORTABLE POWER
Manufacturer
Semtech Corporation
Datasheet
1.SC1401.pdf
(17 pages)
Available stocks
Company
Part Number
Manufacturer
Quantity
Price
Part Number:
SC1401A-12A
Manufacturer:
SOCIONEXT
Quantity:
20 000
Part Number:
SC1401ISS
Manufacturer:
SC
Quantity:
20 000
Company:
Part Number:
SC1401ISSTR
Manufacturer:
HITACHI
Quantity:
5 936
November 21, 2000
© 2000 SEMTECH CORP.
Detailed Description
The SC1401 is a high performance, high efficiency,
PWM synchronous buck controller, designed to
power the latest generation microprocessors in
battery operated systems. Two high-current gate
drive outputs are supplied to control both MOSFETs
in the synchronous rectified buck converter. This
power supply can be programmed to operate at
either fixed (1.25V) or adjustable output voltages.
The power save feature enables high efficiency over
a wide range of load current. The control and fault
monitoring circuitry associated with the PWM
controller includes digital softstart, turn-on
sequencing, frequency compensation, power save,
overcurrent and over and under voltage fault
protection. An LDO NMOS linear regulator is also
generated by the SC1401. A block diagram of the
SC1401 is shown in Figure 1.
PWM Control Block
The SC1401 employs peak-current-mode control with
slope compensation to provide fast output response
to load and line transients. The PWM control block
consists of an analog PWM modulator followed by
PWM logic control. The analog modulator combines
the current output, slope compensation signal and
error voltage to generate a PWM pulse train. The
PWM logic uses the pulse train from the modulator
and other control signals to generate the output
states for the high and low side gate driver outputs.
A block diagram of the PWM control block is shown
in Figure 2.
An error amplifier generates the difference signal
between the reference voltage and the feedback
voltage to generate the control voltage for the peak
current mode comparator. A nominal gain of 8 is
used in the error amplifier to further increase the
system loop-gain and reduce the load regulation
error typically seen with low loop-gain current mode
controllers. The increased gain in the voltage loop is
compensated by pole-zero-pole response of the
voltage error amplifier. The current feedback signal
is summed with the slope compensation signal and
compared to the control voltage by the PWM
comparator.
When the power supply is operating in continuous
conduction mode with current > 25% of its peak
value, the high side MOSFET is turned on at the
beginning of each switching cycle. The high-side
MOSFET is turned off when the desired duty cycle is
HIGH PERFORMANCE SYNCHRONOUS BUCK
CONTROLLER WITH LDO FOR PORTABLE
POWER
TEL:805-498-2111 FAX:805-498-3804 WEB:http://www.semtech.com
V
∆I
652 MITCHELL ROAD
reached. Active shoot-through protection delays the
turn-on of the low-side power device until the
PHASE node drops below 1.25V. The low-side
devices remains on until the beginning of the next
switching cycle. Again, active shoot-through
protection ensures that the gate to the low-side
power device is low before the high-side device is
turned on.
When PSAVE is enabled (low) and the output
current drops below 25% of its peak level, the PWM
logic will automatically enter PSAVE mode to
improve efficiency. When the controller enters
power save, it increases the regulation point by
0.8%, typically issuing one more high side pulse as
the converter enters PSAVE. The PWM control
then disables switching cycles until the FB falls
below the reference. At light loads the effective
switching frequency will drop dramatically and
efficiency will increase because of the reduced gate
charge current required to switch the power stage.
Boosting the regulation point when entering PSAVE
gives the output improved dynamic regulation
because the output voltage is not allowed to droop
below the nominal regulation point. Load current
steps, that cause the converter to come out of
PSAVE, will not cause as large a negative dip in the
output voltage.
The PSAVE threshold is a function of the load and
peak-to-peak inductor current. It can be calculated
by the following equations:
!I
I
V
V
D = Duty Cycle
f = Frequency
L = Inductance
O
THPSAVE
IN
O
L
= Load Current
L
= Output Voltage
= Input Voltage
= peak-to-peak inductor current
V
IN
L
-
I
V
O
-
O
∆I
2
L
D
f
R
S
NEWBURY PARK CA 91320
SC1401
12