H-38-11 Bourns Inc., H-38-11 Datasheet - Page 39
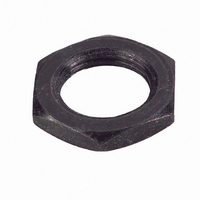
H-38-11
Manufacturer Part Number
H-38-11
Description
HDWR NUT MOUNTING FOR ECW ENCODR
Manufacturer
Bourns Inc.
Type
Mounting Nutr
Series
Hr
Datasheet
1.H-37-2.pdf
(73 pages)
Specifications of H-38-11
Mounting Hole Size
9 mm
Features
Hardware indicated by shaded area is normally supplied with unit
Lead Free Status / RoHS Status
Lead free / RoHS Compliant
For Use With
ECW1DB24BC0024 - ENCODER DIGITAL CONT 24 CPRECW1JB24BC0024 - ENCODER DIGITAL CONT 24 CPR
Lead Free Status / Rohs Status
Lead free / RoHS Compliant
38
Application Notes
Belt and pulley arrangement can be used to transmit
rotary or linear motion to the encoder. Standard
timing belts or chains, round belts, wire fishing line,
etc., are commonly utilized. A pulley or gear can be
mounted directly to the encoder shaft. In some cases
it is necessary to reduce heavy side loading created
by belt tension. Adding a separate pulley with
suitable bearings and connecting the pulley shaft to
the encoder with a flexible coupling can accomplish
this.
Rack and pinion arrangement can easily transmit
linear motion to the encoder. The pinion can be
attached directly onto the encoder shaft.
Other methods of interfacing encoder shafts are:
When choosing an interfacing technique, remember
that the accuracy of the encoder will be no better
than the accuracy of the transmission system.
• Tubing or springs pressed onto the shafts
• Interlocking shafts
• Rubber wheels
• Flatted shafts and receptacles
• Gear transmission systems
Typical Interface Circuits
The EN Series Optical Encoder may be used as a
manual input device for digitally controlled
equipment such as CAD/CAM systems, electronic
test equipment, medical electronics,
instrumentation, computer peripherals and machine
tools. Typically, the encoder drives an up/down
counter and is used to control one or more
functions. Common applications include motor
speed control, cursor control, frequency setting,
amplifier gain adjustment and table positioning.
This device can also be used for position sensing
applications. In this case, a gear can be placed on the
encoder shaft allowing it to be interfaced with a
moving table, rotating shaft, stepping motor, etc.
Movement of the encoder shaft is translated into a 2-
bit quadrature signal, which (fed through a logic
circuit) allows the microprocessor to determine
changes in position. As a position feedback device,
there are a wide variety of possible uses for an
optical encoder including machine tools, plotters,
automated storage systems and robotics.