A3981KLPTR-T Allegro Microsystems Inc, A3981KLPTR-T Datasheet - Page 38
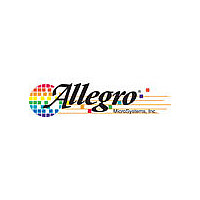
A3981KLPTR-T
Manufacturer Part Number
A3981KLPTR-T
Description
AUTOMOTIVE PROGRAMMABLE STEPPER DRVR
Manufacturer
Allegro Microsystems Inc
Datasheet
1.A3981KLPTR-T.pdf
(42 pages)
Specifications of A3981KLPTR-T
Applications
Stepper Motor Driver, 2 Phase
Number Of Outputs
1
Voltage - Load
7 V ~ 28 V
Voltage - Supply
3 V ~ 5.5 V
Operating Temperature
-40°C ~ 150°C
Mounting Type
Surface Mount
Package / Case
28-TSSOP (0.173", 4.40mm Width) Exposed Pad
Lead Free Status / RoHS Status
Lead free / RoHS Compliant
Current - Output
-
Lead Free Status / RoHS Status
Lead free / RoHS Compliant
Available stocks
Company
Part Number
Manufacturer
Quantity
Price
Part Number:
A3981KLPTR-T
Manufacturer:
ALLEGRO/雅丽高
Quantity:
20 000
A3981
Improved Half Step
Figure A5 shows a circle superimposed on the phase diagram.
This circle represents the required locus of the resultant phase cur-
rent vectors to maintain 100% current magnitude. At the full-step
positions, 0, 2, 4, and 6, only one phase is active and the magni-
tude of the phase current is at 100%. At the half-step positions, 1,
3, 5, and 7, both phases are active. To ensure that the magnitude
of the resultant current is 100%, the magnitude of each phase cur-
rent must be 70.7%. Calculating the value of the resultant current
as before gives a resultant current of 100%.
Figure A5. Phase diagram for improved half step
Figure A6. Phase diagram for quarter step
0.707
2
F
4
8
9
7
+ 0.707
H
H
10
6
3
5
11
2
5
=
Phase A
Current
12
2
6
0.5 + 0.5 =
I
A
F
F
4
13
3
Resultant
1
7
14
2
1 = 1
H
H
1
15
0
0
F
Automotive, Programmable Stepper Driver
Phase B
Current
I
B
The current vectors at half-step position 1 are shown specifically
to illustrate that the magnitude of the resultant sits on the 100%
circle.
For a standard stepper motor to operate with minimum torque
ripple, the resultant current must always lie on the constant torque
circle irrespective of the number of microsteps. For higher resolu-
tion microstepping this then defines the relative phase currents at
each microstep position.
Quarter Step
For example consider the next resolution in microstepping; quar-
ter step. The locus of the required phase currents are shown in
figure A6. The required current level in each phase can be calcu-
lated using simple trigonometry. For example, consider microstep
position 7 in figure A6 as detailed in figure A7.
There are 4 quarter steps for each full step. A full step on the
phase diagram is represented by 90°. So each quarter step incre-
ments the phase angle by 90° / 4 = 22.5°.
In figure A7 the resultant motor current at quarter-step position 8
is one quarter step from the horizontal, so it is at 22.5°. The mag-
nitude of the current in phase A at quarter-step position 7, I
is therefore sin 22.5°, which is equal to 0.383 or 38.3% of the
maximum current.
Similarly, the magnitude of the current in phase B at quarter-step
position 7, I
92.4% of the maximum current.
At the 45° positions, 2, 6, 10 and 14, the magnitude of the current
in phase A and phase B will be cos 45° = 0.707 or 70.7%, which
is the same magnitude as in the half-step case shown in figure A5.
Due to symmetry, the phase A current is the same at quarter-step
positions 7 and 1. The phase A current at quarter-step positions
9 and 15 also has the same magnitude, but the current is in the
Figure A7. Calculating phase current magnitudes
8
B7
7
, is therefore cos 22.5°, which is equal to 0.924 or
I
B7
=-cos22.5°
6
115 Northeast Cutoff
1.508.853.5000; www.allegromicro.com
Allegro MicroSystems, Inc.
Worcester, Massachusetts 01615-0036 U.S.A.
22.5°
I
A
=sin22.5°
I
I
A7
B
A7
,
38