A3981KLPTR-T Allegro Microsystems Inc, A3981KLPTR-T Datasheet - Page 9
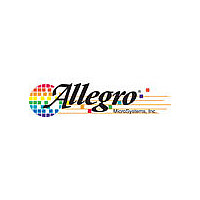
A3981KLPTR-T
Manufacturer Part Number
A3981KLPTR-T
Description
AUTOMOTIVE PROGRAMMABLE STEPPER DRVR
Manufacturer
Allegro Microsystems Inc
Datasheet
1.A3981KLPTR-T.pdf
(42 pages)
Specifications of A3981KLPTR-T
Applications
Stepper Motor Driver, 2 Phase
Number Of Outputs
1
Voltage - Load
7 V ~ 28 V
Voltage - Supply
3 V ~ 5.5 V
Operating Temperature
-40°C ~ 150°C
Mounting Type
Surface Mount
Package / Case
28-TSSOP (0.173", 4.40mm Width) Exposed Pad
Lead Free Status / RoHS Status
Lead free / RoHS Compliant
Current - Output
-
Lead Free Status / RoHS Status
Lead free / RoHS Compliant
Available stocks
Company
Part Number
Manufacturer
Quantity
Price
Part Number:
A3981KLPTR-T
Manufacturer:
ALLEGRO/雅丽高
Quantity:
20 000
A3981
impedance allowing multiple SDI slaves to have common SDI,
SCK, and SDO connections.
DIAG Diagnostic output. Function selected via the serial inter-
face, setting Configuration Register 1. Default is Fault output.
OSC With bit 13 in Configuration Register 1 set to 0, either con-
nect this pin to AGND to use the internal oscillator running at the
default frequency of 4 MHz, or connect a resistor to VDD to set
the internal oscillator frequency. ( The approximate frequency is
calculated from:
where f
is the value, in kΩ of the resistor between OSC and VDD.)
If bit 13 in Configuration Register 1 is set to 1, then OSC is the
input for an external system clock, which must have a frequency
between 3 and 5 MHz. In this mode a watchdog is provided to
detect loss of the system clock. If the OSC pin remains high or
low for more than the watchdog time, t
Fault Register flag (bit 15 in the diagnostic registers) is set and
the outputs are disabled until the clock restarts.
Driving a Stepper Motor
A two-phase stepper motor is made to rotate by sequencing
the relative currents in each phase. In its simplest form, each
phase is simply fully energized in turn by applying a voltage to
the winding. For more precise control of the motor torque over
temperature and voltage ranges, current control is required. For
efficiency this is usually accomplished using pulse width modula-
tion (PWM) techniques. In addition current control also allows
the relative current in each phase to be controlled, providing more
precise control over the motor movement and hence improve-
ments in torque ripple and mechanical noise. Further details of
stepper motor control are provided in Appendix A.
For bipolar stepper motors the current direction is significant,
so the voltage applied to each phase must be reversible. This
requires the use of a full bridge (also known as an H-bridge)
which can switch each phase connection to supply or to ground.
Phase Current Control
In the A3981, current to each phase of the two-phase bipolar
stepper motor is controlled through a low impedance N-channel
DMOS full bridge. This allows efficient and precise control of
the phase current using PWM switching. The full-bridge con-
figuration provides full control over the current direction during
the PWM on-time, and over the current decay mode during the
PWM off-time. Due to the flexibility of the A3981 these control
techniques can be completely transparent to the user or can be
OSC
is the internal oscillator frequency in MHz, and R
f
OSC
= 10 000 / (48 R
OSC
WD
, 1 μs typical, then the
– 20)
Automotive, Programmable Stepper Driver
OSC
partially- or fully-programmed through the serial interface.
Each leg (high-side, low-side pair) of a bridge is protected from
shoot-through by a fixed dead time. This is the time between
switching off one FET and switching on the complementary FET.
Cross-conduction is prevented by lock-out logic in each driver pair.
The phase currents and in particular the relative phase currents
are defined in the Phase Current table (table 7). This table defines
the two phase currents at each microstep position. For each of the
two phases, the currents are measured using a sense resistor, R
with voltage feedback to the respective SENSx pin. The target
current level is defined by the voltage from the digital-to-analog
converter (DAC) for that phase. The sense voltage is amplified by
a fixed gain and compared to the output of the DAC.
There are two types of maximum current: the absolute maximum,
I
tor and the reference input; and the phase maximum, I
maximum current delivered to a motor phase.
The absolute maximum current, I
where V
resistor value.
The phase maximum, I
phase current table and may be a fraction of the absolute maxi-
mum current, I
MXI1 bits in Configuration Register 0.
For example:
• if R
• if MXI1= 1 and MXI0 = 0, then I
The actual current delivered to each phase at each Step Angle
Number is determined by the value of I
of the Phase Current table. For each phase, the value in the table
is passed to the DAC, which uses I
level (code 63) and reduces the current target depending on the
DAC code. The output from the DAC is used as the input to the
current comparators.
The current comparison is ignored at the start of the PWM
on-time for a duration referred to as the blank time. The blank
time is necessary to prevent any capacitive switching currents
from causing a peak current detection.
The PWM on-time starts at the beginning of each PWM period.
The current rises in the phase winding until the sense voltage
reaches the required current level. At this point the PWM off-time
SMAX
S
, the maximum possible current defined by the sense resis-
= 180 mΩ and V
REF
is the voltage at the REF pin, and R
SMAX
I
, depending on the value of the MXI0 and
SMAX
PMAX
REF
= V
115 Northeast Cutoff
1.508.853.5000; www.allegromicro.com
Allegro MicroSystems, Inc.
Worcester, Massachusetts 01615-0036 U.S.A.
= 2 V, then I
, is the 100% reference level for the
REF
SMAX
/ (16 × R
PMAX
PMAX
, is defined as:
PMAX
SMAX
= 520 mA
as the reference 100%
S
)
and the contents
= 694 mA
S
is the sense
PMAX
, the
S
,
9