FW330 Lineage Power, FW330 Datasheet - Page 22
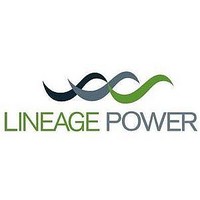
FW330
Manufacturer Part Number
FW330
Description
Fw330 Power Modules Dc-dc Converters 36 To 75 Vdc Input, 3.6, 3.3, 2.5, 2.0, Or 1.8 Vdc Output; 180 W To 330 W
Manufacturer
Lineage Power
Datasheet
1.FW330.pdf
(28 pages)
Available stocks
Company
Part Number
Manufacturer
Quantity
Price
Company:
Part Number:
FW330D1
Manufacturer:
EUPEC
Quantity:
292
Part Number:
FW330D1
Quantity:
55
Company:
Part Number:
FW330F-33T
Manufacturer:
LUCENT
Quantity:
27
Company:
Part Number:
FW330F-33T
Manufacturer:
COSEL
Quantity:
387
Company:
Part Number:
FW330F1
Manufacturer:
LUCENT
Quantity:
27
Company:
Part Number:
FW330F1
Manufacturer:
LUCENT
Quantity:
334
Part Number:
FW330F1
Quantity:
55
Part Number:
FW330G1
Quantity:
55
Part Number:
FW330Y1
Quantity:
55
36 to 75 Vdc Input, 3.6, 3.3, 2.5, 2.0, or 1.8 Vdc Output; 180 W to 330 W
Thermal Considerations
Heat Transfer with Heat Sinks
Example
If an 85 °C case temperature is desired, what is the
minimum airflow necessary? Assume the FW330Y1
module is operating at nominal line and an output cur-
rent of 100 A, maximum ambient air temperature of
40 °C, and the heat sink is 1 inch.
Solution
Given: V
Determine P
Then solve the following equation:
Use Figures 34 and 35 to determine air velocity for the
1 inch heat sink. The minimum airflow necessary for
this module depends on heat sink fin orientation and is
shown below:
n
n
Custom Heat Sinks
The heat sink resistances of Figures 34 and 35 are
dominated by the heat sink geometry of the heat sinks
shown in Figures 42 and 43. Because the heat sink
geometry is fixed, the heat sinks are not optimized for
all the air speeds shown. It may be necessary to design
a custom heat sink that provides lower thermal resis-
tance than the ones used in this testing or to use other
heat transfer removal methods.
22
22
1.25 m/s (250 ft./min.) (transverse orientation)
1.75 m/s (350 ft./min.) (longitudinal orientation)
θ
θ
θ
ca
ca
ca
I
T
T
Heat sink = 1 inch
P
O
=
=
=
A
C
I
D
= 54 V
= 100 A
= 40 °C
= 85 °C
= 68 W
0.66 °C/W
D
(
----------------------- -
(
----------------------- -
T
85 40
by using Figure 37:
C
P
68
–
–
D
T
A
)
)
(continued)
(continued)
A more detailed model can be used to determine the
required thermal resistance of a heat sink to provide
necessary cooling. The total module resistance can be
separated into a resistance from case-to-sink (θcs) and
sink-to-ambient (θsa) as shown in Figure 41.
Figure 41. Resistance from Case-to-Sink and Sink-
When custom heat sinks are used, the interface
between the module and the heat sink base should be
filled with a thermally conductive material (like a ther-
mal grease or a thermal pad/foil) to reduce the thermal
resistance between the module and the heat sink. It is
recommended that the material is at least 6 mils thick
to compensate for flatness differences between the
module and the heat sink. Also, special considerations
should be paid to the flatness and surface finish of the
heat sink base to ensure the lowest thermal interface
resistance feasible.
For a managed interface using thermal grease or foils,
a value of θcs = 0.1 °C/W to 0.3 °C/W is typical. The
solution for heat sink resistance is:
This equation assumes that all dissipated power must
be shed by the heat sink. Depending on the user-
defined application environment, a more accurate
model, including heat transfer from the sides and bot-
tom of the module, can be used. This equation pro-
vides a conservative estimate for such instances.
EMC Considerations
For assistance with designing for EMC compliance,
please refer to the FLTR100V10 data sheet
(DS99-294EPS).
Layout Considerations
Copper paths must not be routed beneath the power
module mounting inserts. For additional layout guide-
lines, refer to the FLTR100V10 data sheet
(DS99-294EPS).
θ
sa
P
D
=
→
(
------------------------ -
to-Ambient
T
C
T
P
–
C
D
T
A
)
–
θcs
θ
cs
T
S
θsa
April 3, 2008
Lineage Power
T
A
8-1304 (C)