sc2441a Semtech Corporation, sc2441a Datasheet - Page 26
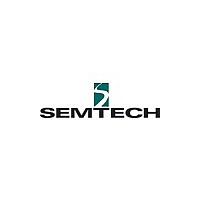
sc2441a
Manufacturer Part Number
sc2441a
Description
Sc2441a 1.8v To 20v Input 2-phase Synchronous Step-down Controllers With Step-up Converter
Manufacturer
Semtech Corporation
Datasheet
1.SC2441A.pdf
(37 pages)
Master - Slave Mode Configuration
The configuration for SC2441A master-slave mode
operation is shown in Figure 15. The master is made
free running, the master clock frequency should be within
the synchronizing range of the slave.
In the Master-Slave mode, the SS2441A can be
synchronized to an external clock signal applied to the
SYNC pin. External filtering componets (R
on the PLLF pin are necessary for the slave SC2441A .
The PLLF pull-up resistor is not necessary for the slave
converter.
Phase shift between the master and the slave is the
phase lag measured between the sync input and the clock
output of the slave. Typical relationship between the phase
shift and the slave value of the resistor R
the “Typical Characteristics”.
For the SC2441A running at slave mode, its free-runing
frequency (internal switching frequency) set with ROSC
should be programmed 20% higher than the external
synchronization frequency.
POWER MANAGEMENT
Applications Information
2006 Semtech Corp.
Figure 15. Master-Slave Synchronization
R4
SYNC
SYNC
CKOUT
CKOUT
SC2441A
SC2441A
Master
Slave
VIN
PLLF
PLLF
C2
R3
C1
R1
1
, R
2
2
is shown in
, C
1
and C
R2
2
)
26
As shown in Figure 15, the CKOUT signal of the master
SC2441A is the input sync signal for the slave SC2441A.
The R
the phase lock loop in the slave SC2441A. R2 (between
30k
the slave CKOUT and its SYNC input.
PLL Frequency Compensation
Applying synchronizing clock with step change in frequency
adjust compensation components until overshoot and
ringing at PLLF pin is minimized.
Output Inductor and Ripple Current in Step-down
Sections
Both step-down controllers in the SC2441A operate in
synchronous continuous-conduction mode (CCM)
regardless of the output load. The output inductor
selection/design is based on the output DC and transient
requirements. Both output current and voltage ripples
are reduced with larger inductors but it takes longer to
change the inductor current during load transients.
Conversely smaller inductors results in lower DC copper
losses but the AC core losses (flux swing) and the winding
AC resistance losses are higher. A compromise is to
choose the inductance such that the peak to peak
inductor ripple current is 20% to 30% of the rated output
current.
Assume that the inductor current ripple (peak-to-peak)
is
The peak current in the inductor becomes (1+ /2)*Io
and the RMS current is
The followings are to be considered when choosing
inductors.
a) Inductor core material: For high efficiency applications
above 350KHz, ferrite, Kool-Mu and polypermalloy
materials should be used. Low-cost powdered iron cores
can be used for cost sensitive-applications below 350KHz
but with attendant higher core losses.
1
, C
and 150k
Then the inductance will be
1
and C
2
constitute the filtering circuit stabilizing
determines the phase shift between
I
, L
rms
L
=
=
V
I
o
o
d
1 (
f I
1
o
-
+
s
D
12
d
)
2
.
.
SC2441A
www.semtech.com