VIPER53ESPTR-E STMicroelectronics, VIPER53ESPTR-E Datasheet - Page 9
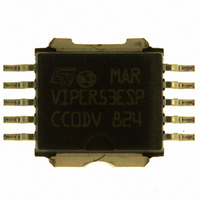
VIPER53ESPTR-E
Manufacturer Part Number
VIPER53ESPTR-E
Description
IC OFFLINE SWIT PWM POWERSO10
Manufacturer
STMicroelectronics
Series
VIPER™r
Datasheet
1.VIPER53ESPTR-E.pdf
(31 pages)
Specifications of VIPER53ESPTR-E
Output Isolation
Isolated
Frequency Range
93 ~ 300kHz
Voltage - Input
8.4 ~ 19 V
Voltage - Output
620V
Power (watts)
40W
Operating Temperature
25°C ~ 125°C
Package / Case
PowerSO-10 Exposed Bottom Pad
On Resistance (max)
1.7 Ohms
Supply Voltage (max)
19 V
Supply Voltage (min)
2.6 V
Maximum Operating Temperature
+ 150 C
Minimum Operating Temperature
- 40 C
Mounting Style
SMD/SMT
Number Of Switches
Single
Off Isolation (typ)
8.4 V
Operating Temperature (max)
150C
Operating Temperature (min)
-40C
Pin Count
10
Mounting
Surface Mount
Package Type
PowerSO
Screening Level
Automotive
For Use With
497-8435 - BOARD EVAL FOR VIPER53 28W497-6458 - BOARD EVAL BASED ON VIPER53-E497-6262 - BOARD REF SGL VIPER53 90-264VAC497-5866 - EVAL BOARD 24W NEG OUT VIPER53E497-5865 - EVAL BOARD 24W POS OUT VIPER53E497-4933 - BOARD PWR SUPPLY 24W OUTPUT VIPE
Lead Free Status / RoHS Status
Lead free / RoHS Compliant
Other names
497-5772-2
Available stocks
Company
Part Number
Manufacturer
Quantity
Price
Company:
Part Number:
VIPER53ESPTR-E
Manufacturer:
TI
Quantity:
1 500
Part Number:
VIPER53ESPTR-E
Manufacturer:
ST
Quantity:
20 000
VIPer53EDIP - E / VIPer53ESP - E
5
Secondary Feedback Configuration Example
The secondary feedback is implemented through an optocoupler driven by a programmable
zener diode (TL431 type) as shown in
The optocoupler is connected in parallel with the compensation network on the COMP pin
which delivers a constant biasing current of 0.6mA to the optotransistor. This current does
not depend on the compensation voltage, and so it does not depend on the output load
either. Consequently, the gain of the optocoupler ensures a constant biasing of the TL431
device (U3), which is responsible for secondary regulation. If the optocoupler gain is
sufficiently low, no additional components are required to a minimum current biasing of U3.
Additionally, the low biasing current protects the optocoupler from premature failure.
The constant current biasing can be used to simplify the secondary circuit: instead of a
TL431, a simple zener and resistance network in series with the optocoupler diode can
insure a good secondary regulation. Current flowing in this branch remains constant just as
it does by using a TL431, so typical load regulation of 1% can be achieved from zero to full
output current with this simple configuration.
Since the dynamic characteristics of the converter are set on the secondary side through
components associated to U3, the compensation network has only a role of gain
stabilization for the optocoupler, and its value can be freely chosen. R5 can be set to a fixed
value of 2.2k , offering the possibility of using C7 as a soft start capacitor: When starting up
the converter, the VIPer53E device delivers a constant current of 0.6mA on the COMP pin,
creating a constant voltage of 1.3V in R5 and a rising slope across C7. This voltage shape,
together with the operating range of 0.5V to 4.5V provides a soft startup of the converter.
The rising speed of the output voltage can be set through the value of C7. The C4 and C6
values must be adjusted accordingly in order to ensure a correct startup.
DocRev1
Figure 3 on page 8
Secondary Feedback Configuration Example
9/31