FW300B1 Lineage Power, FW300B1 Datasheet - Page 14
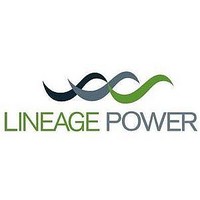
FW300B1
Manufacturer Part Number
FW300B1
Description
CONVERTER DC/DC 12V 300W OUT
Manufacturer
Lineage Power
Series
FW300r
Type
Isolated with Remote On/Offr
Datasheet
1.FW300B1.pdf
(20 pages)
Specifications of FW300B1
Output
12V
Number Of Outputs
1
Power (watts)
300W
Mounting Type
Through Hole
Voltage - Input
36 ~ 75V
Package / Case
Module
1st Output
12 VDC @ 25A
Size / Dimension
4.60" L x 2.40" W x 0.53" H (116.8mm x 61mm x 13.5mm)
Power (watts) - Rated
300W
Operating Temperature
-40°C ~ 100°C
Efficiency
87%
Approvals
CE, CSA, UL, VDE
Lead Free Status / RoHS Status
Contains lead / RoHS non-compliant
3rd Output
-
2nd Output
-
4th Output
-
Available stocks
Company
Part Number
Manufacturer
Quantity
Price
Company:
Part Number:
FW300B1
Manufacturer:
EUPEC/Infineon
Quantity:
1 000
Part Number:
FW300B1
Manufacturer:
SANKEN
Quantity:
20 000
Part Number:
FW300B1
Quantity:
55
Part Number:
FW300B1
Quantity:
55
FW250B1 and FW300B1 Power Modules: dc-dc Converters:
36 Vdc to 75 Vdc Input, 12 Vdc Output; 250 W to 300 W
Thermal Considerations
Heat Transfer with Heat Sinks
The power modules have through-threaded, M3 x 0.5
mounting holes, which enable heat sinks or cold plates
to be attached to the module. The mounting torque
must not exceed 0.56 N-m (5 in.-lb.). For the screw
attachment from the pin side, the recommended hole
size on the customer’s PWB around the mounting
holes is 0.130 ± 0.005 inches. If a larger hole is used,
the mounting torque from the pin side must not exceed
0.25 N-m (2.2 in.-lb.).
Thermal derating with heat sinks is expressed by using
the overall thermal resistance of the module. Total mod-
ule thermal resistance ( ca) is defined as the maximum
case temperature rise ( T
power dissipation (P
The location to measure case temperature (T
shown in Figure 18. Case-to-ambient thermal resis-
tance vs. airflow for various heat sink configurations is
shown in Figures 21 and 22. These curves were
obtained by experimental testing of heat sinks, which
are offered in the product catalog.
Figure 21. Case-to-Ambient Thermal Resistance
14
14
4.5
4.0
3.5
3.0
2.5
2.0
1.5
1.0
0.5
0.0
ca
0
=
Curves; Transverse Orientation
-------------------- -
(100)
0.5
T
P
C max
,
D
AIR VELOCITY, m/s (ft./min.)
D
(200)
):
1.0
=
C, max
----------------------- -
T
(300)
C
1.5
P
–
) divided by the module
D
T
A
(continued)
1 1/2 IN. HEAT SINK
1 IN. HEAT SINK
1/2 IN. HEAT SINK
1/4 IN. HEAT SINK
NO HEAT SINK
(400)
2.0
(500)
2.5
C
) is
8-1321 (C)
(600)
3.0
Figure 22. Case-to-Ambient Thermal Resistance
These measured resistances are from heat transfer
from the sides and bottom of the module as well as the
top side with the attached heat sink; therefore, the
case-to-ambient thermal resistances shown are gener-
ally lower than the resistance of the heat sink by itself.
The module used to collect the data in Figures 21 and
22 had a thermal-conductive dry pad between the case
and the heat sink to minimize contact resistance.
To choose a heat sink, determine the power dissipated
as heat by the unit for the particular application.
Figures 23 and 24 show typical heat dissipation for a
range of output currents and three voltages for the
FW250B1 and FW300B1.
Figure 23. FW250B1 Power Dissipation vs. Output
4.5
4.0
3.5
3.0
2.5
2.0
1.5
1.0
0.5
0.0
50
45
40
35
30
25
20
15
10
5
0
0
0
Curves; Longitudinal Orientation
Current at 25 °C
2
(100)
0.5
4
V
I
V
V
AIR VELOCITY, m/s (ft./min.)
= 55.5 V
I
I
(200)
= 75 V
= 36 V
OUTPUT CURRENT, I
6
1.0
8
(300)
10
1.5
Lucent Technologies Inc.
12
1 1/2 IN. HEAT SINK
1 IN. HEAT SINK
1/2 IN. HEAT SINK
1/4 IN. HEAT SINK
NO HEAT SINK
(400)
2.0
14
O
(A)
March 2000
Data Sheet
16
(500)
2.5
18
8-1320 (C)
8-1732 (C)
(600)
20
3.0