HMC1042L-TR Honeywell Microelectronics & Precision Sensors, HMC1042L-TR Datasheet - Page 5
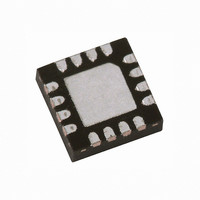
HMC1042L-TR
Manufacturer Part Number
HMC1042L-TR
Description
MAGNETIC SENSORS
Manufacturer
Honeywell Microelectronics & Precision Sensors
Type
Linearr
Datasheet
1.HMC1042L-TR.pdf
(6 pages)
Specifications of HMC1042L-TR
Sensing Range
±6g
Voltage - Supply
1.8 V ~ 20 V
Output Type
Differential Voltage
Features
Compass - Two Axis
Operating Temperature
-40°C ~ 125°C
Package / Case
16-VQFN Exposed Pad
Lead Free Status / RoHS Status
Lead free / RoHS Compliant
For Use With
342-1064 - DEMO BOARD FOR HMC1042L/HMC1041Z
Current - Supply
-
Current - Output (max)
-
Lead Free Status / RoHS Status
Lead free / RoHS Compliant
Other names
342-1053-2
HMC1042L
Stencil Design and Solder Paste
A 4 mil stencil and 100% paste coverage is recommended for the electrical contact pads. The HMC1042L has been
tested successfully with no-clean solder paste.
BASIC DEVICE OPERATION
The Honeywell HMC1042L magnetoresistive sensors are Wheatstone bridge devices to measure magnetic fields. With
power supply applied to the bridges, the sensors convert any incident magnetic field in the sensitive axis directions to a
differential voltage output. In addition to the bridge circuit, the sensor has two on-chip magnetically coupled straps; the
offset strap and the set/reset strap. These straps are Honeywell patented features for incident field adjustment and
magnetic domain alignment; and eliminate the need for external coils positioned around the sensors. The straps are
common in effect to both bridges.
The magnetoresistive sensors are made of a nickel-iron (Permalloy) thin-film deposited on a silicon wafer and patterned
as a resistive strip element. In the presence of a magnetic field, a change in the bridge resistive elements causes a
corresponding change in voltage across the bridge outputs.
These resistive elements are aligned together to have a common sensitive axis (indicated by arrows on the pinouts) that
will provide positive voltage change with magnetic fields increasing in the sensitive direction. Because the output only is in
proportion to the one-dimensional axis (the principle of anisotropy) and its magnitude, additional sensor bridges placed at
orthogonal directions permit accurate measurement of arbitrary field direction. The combination of sensor bridges in two
and three orthogonal axis permit applications such as compassing and magnetometry.
The offset strap allows for several modes of operation when a direct current is driven through it. These modes are: 1)
Subtraction (bucking) of an unwanted external magnetic field, 2) null-ing of the bridge offset voltage, 3) Closed loop field
cancellation, and 4) Auto-calibration of bridge gain.
The set/reset strap can be pulsed with high currents for the following benefits: 1) Enable the sensor to perform high
sensitivity measurements, 2) Flip the polarity of the bridge output voltage, and 3) Periodically used to improve linearity,
lower cross-axis effects, and temperature effects.
Offset Strap
The offset strap is a spiral of metallization that couples in the sensor element’s sensitive axis. The offset strap measures
nominally 15 ohms, and requires 10mA for each gauss of induced field. The straps will easily handle currents to buck or
boost fields through the ±6 gauss linear measurement range, but designers should note the extreme thermal heating on
the die when doing so.
With most applications, the offset strap is not utilized and can be ignored. Designers can leave one or both strap
connections (Off- and Off+) open circuited, or ground one connection node. Do not tie both strap connections together to
avoid shorted turn magnetic circuits.
Set/Reset Strap
The set/reset strap is another spiral of metallization that couples to the sensor elements easy axis (perpendicular to the
sensitive axis on the sensor die. Each set/reset strap has a nominal resistance of 5 ohms with a nominal required peak
current of 500mA for reset or set pulses. With rare exception, the set/reset strap must be used to periodically condition the
magnetic domains of the magneto-resistive elements for best and reliable performance.
A set pulse is defined as a positive pulse current entering the S/R+ strap connection. The successful result would be the
magnetic domains aligned in a forward easy-axis direction so that the sensor bridge’s polarity is a positive slope with
positive fields on the sensitive axis result in positive voltages across the bridge output connections.
A reset pulse is defined as a negative pulse current entering the S/R+ strap connection. The successful result would be
the magnetic domains aligned in a reverse easy-axis direction so that bridge’s polarity is a negative slope with positive
fields on the sensitive axis result in negative voltages across the bridge output connections.
Typically a reset pulse is sent first, followed by a set pulse a few milliseconds later. By shoving the magnetic domains in
completely opposite directions, any prior magnetic disturbances are likely to be completely erased by the duet of pulses.
For simpler circuits with less critical requirements for noise and accuracy, a single polarity pulse circuit may be employed
www.honeywell.com
5