GNM314R71H102KD01D Murata, GNM314R71H102KD01D Datasheet - Page 159
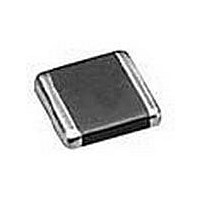
GNM314R71H102KD01D
Manufacturer Part Number
GNM314R71H102KD01D
Description
Manufacturer
Murata
Type
Ceramicr
Datasheet
1.GNM314R71H102KD01D.pdf
(220 pages)
Specifications of GNM314R71H102KD01D
Capacitance
1000pF
No. Of Capacitors
4
Tolerance (+ Or -)
10%
Voltage
50VDC
Number Of Terminals
8Terminal
Temp Coeff (dielectric)
X7R
Operating Temp Range
-55C to 125C
Mounting Style
Surface Mount
Package / Case
1206
Construction
SMT Chip
Failure Rate
Not Required
Product Height (mm)
0.8mm
Product Depth (mm)
1.6mm
Product Length (mm)
3.2mm
Lead Diameter (nom)
Not Requiredmm
Terminal Pitch
0.8mm
Lead Free Status / RoHS Status
Compliant
Available stocks
Company
Part Number
Manufacturer
Quantity
Price
Company:
Part Number:
GNM314R71H102KD01D
Manufacturer:
MURATA
Quantity:
120 000
- Current page: 159 of 220
- Download datasheet (4Mb)
!Note
• This PDF catalog is downloaded from the website of Murata Manufacturing co., ltd. Therefore, it’s specifications are subject to change or our products in it may be discontinued without advance notice. Please check with our
• This PDF catalog has only typical specifications because there is no space for detailed specifications. Therefore, please approve our product specifications or transact the approval sheet for product specifications before ordering.
sales representatives or product engineers before ordering.
!Note
7. Coating
1. A crack may be caused in the capacitor due to the stress
8. Die Bonding/Wire Bonding (GMA or GMD Series)
1. Die Bonding of Capacitors
Notice
of the thermal contraction of the resin during curing
process.
The stress is affected by the amount of resin and curing
contraction.
Select a resin with small curing contraction.
The difference in the thermal expansion coefficient
between a coating resin or a molding resin and capacitor
may cause the destruction and deterioration of the
capacitor such as a crack or peeling, and lead to the
deterioration of insulation resistance or dielectric
breakdown.
• Use the following materials for the Brazing alloys:
• Mounting
Continued from the preceding page.
Au-Sn (80/20) 300 to 320 degree C in N
(1) Control the temperature of the substrate so it
(2) Place the brazing alloy on the substrate and place
• Please read rating and !CAUTION (for storage, operating, rating, soldering, mounting and handling) in this catalog to prevent smoking and/or burning, etc.
• This catalog has only typical specifications because there is no space for detailed specifications. Therefore, please approve our product specifications or transact the approval sheet for product specifications before ordering.
matches the temperature of the brazing alloy.
the capacitor on the alloy. Hold the capacitor and
gently apply the load. Be sure to complete the
operation within 1 minute.
2
atmosphere
2. Select a resin that is less hygroscopic.
2. Wire Bonding
Select a resin for which the thermal expansion coefficient
is as close to that of capacitor as possible.
A silicone resin can be used as an under-coating to buffer
against the stress.
Using hygroscopic resins under high humidity conditions
may cause the deterioration of the insulation resistance of
a capacitor.
An epoxy resin can be used as a less hygroscopic resin.
• Wire
• Bonding
Gold wire: 25 micro m (0.001 inch) diameter
(1) Thermo compression, ultrasonic ball bonding.
(2) Required stage temperature: 150 to 200 degree C
(3) Required wedge or capillary weight: 0.2N to 0.5N
(4) Bond the capacitor and base substrate or other
devices with gold wire.
Notice
157
C02E.pdf
09.9.18
8
Related parts for GNM314R71H102KD01D
Image
Part Number
Description
Manufacturer
Datasheet
Request
R

Part Number:
Description:
Murata Microblower 20x20 DCDC Driver Board - Samples Only
Manufacturer:
Murata

Part Number:
Description:
357-036-542-201 CARDEDGE 36POS DL .156 BLK LOPRO
Manufacturer:
Murata
Datasheet:

Part Number:
Description:
Manufacturer:
Murata
Datasheet:

Part Number:
Description:
Manufacturer:
Murata
Datasheet:

Part Number:
Description:
Manufacturer:
Murata
Datasheet:

Part Number:
Description:
Manufacturer:
Murata
Datasheet:

Part Number:
Description:
Manufacturer:
Murata
Datasheet:

Part Number:
Description:
Manufacturer:
Murata
Datasheet:

Part Number:
Description:
Manufacturer:
Murata
Datasheet:

Part Number:
Description:
BLM21BD751SN1On-Board Type (DC) EMI Suppression Filters
Manufacturer:
Murata
Datasheet:

Part Number:
Description:
BLM15AG100SN1On-Board Type (DC) EMI Suppression Filters
Manufacturer:
Murata
Datasheet:

Part Number:
Description:
NFE31PT222Z1E9On-Board Type (DC) EMI Suppression Filters
Manufacturer:
Murata
Datasheet:

Part Number:
Description:
Chip Coil
Manufacturer:
Murata
Datasheet:

Part Number:
Description:
Chip Coil
Manufacturer:
Murata
Datasheet: