ADN8830ACPZ Analog Devices Inc, ADN8830ACPZ Datasheet - Page 21
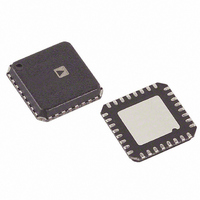
ADN8830ACPZ
Manufacturer Part Number
ADN8830ACPZ
Description
IC CTRLR THERMO COOLER 32-LFCSP
Manufacturer
Analog Devices Inc
Datasheet
1.ADN8830ACPZ-REEL7.pdf
(24 pages)
Specifications of ADN8830ACPZ
Applications
Thermoelectric Cooler
Current - Supply
8mA
Voltage - Supply
3.3 V ~ 5 V
Operating Temperature
-40°C ~ 85°C
Mounting Type
Surface Mount
Package / Case
32-LFCSP
Ic Function
Thermoelectric Cooler Controller
Supply Voltage Range
3V To 5.5V
Operating Temperature Range
-40°C To +85°C
Digital Ic Case Style
LFCSP
No. Of Pins
32
Msl
MSL 1 - Unlimited
Lead Free Status / RoHS Status
Lead free / RoHS Compliant
Other names
015-0070
Q2376189
Q2376189
Available stocks
Company
Part Number
Manufacturer
Quantity
Price
Company:
Part Number:
ADN8830ACPZ
Manufacturer:
ADI
Quantity:
317
Part Number:
ADN8830ACPZ
Manufacturer:
ADI/亚德诺
Quantity:
20 000
Using an RTD for Temperature Sensing
The ADN8830 can be used with a resistive temperature device
(RTD) as the temperature feedback sensor. The resistance of an
RTD is linear with respect to temperature, offering an advan-
tage over thermistors that have an exponential relationship to
temperature. A constant current applied through an RTD will
yield a voltage proportional to temperature. However, this volt-
age could be on the order of only 0.5 mV/ C, thus requiring the
use of additional amplification to achieve a usable signal level.
The ADT70 from Analog Devices can be used to bias and amplify
the voltage across an RTD, which can then be fed directly to the
THERMIN pin on the ADN8830 to provide temperature
feedback for the TEC controller. The ADT70 uses a 0.9 mA
current source to drive the RTD and an instrumentation ampli-
fier with adjustable gain to boost the RTD voltage. Application
notes and typical schematics for this device can be found in the
ADT70 Data Sheet.
Most RTDs have a positive temperature coefficient, also called
tempco, as opposed to thermistors, which have a negative tempco.
For the OUT A output to drive the TEC– input as shown in
Figure 1, the signal from an RTD must be conditioned to create
a negative tempco. This can be easily done using an inverting
amplifier. Alternately, OUT A can be connected to drive TEC+
with OUT B driving TEC– with a positive tempco at THERMIN.
This is highlighted in the Output Driver Amplifiers section.
For the ADN8830, proper operation care should be taken
to ensure the voltage at THERMIN remains within 0.4 V
and 2.0 V. Using a 1 k RTD with the ADT70 will yield a
THERMIN voltage of 0.9 V at 25 C. Using the application
circuit shown in Figure 22 will provide a nominal output
voltage of 1.0 V at 25 C and a total gain of 66.7 mV/ .
Using an RTD with a temperature coefficient of 0.375 / C
will give a THERMIN voltage swing from 1.5 V at 5 C to
0.5 V at 45 C, well within the input range of the ADN8830.
Using a Resistive Load as a Heating Element
The ADN8830 can be used in applications that do not neces-
sarily drive a TEC but require only a high current output into a
load resistance. Such applications generally only require heating
above ambient temperature and simply use the power dissipated
by the load element to accomplish this. Because the power
dissipated by such an element is proportional to the square of
the output voltage, the ADN8830 application circuit must be
modified. Figure 24 shows the preferred method for driving a
heating element load.
REV. C
–21–
Current is delivered from the PWM amplifier through Q3 when
the voltage at THERMIN is lower than TEMPSET. If the object
temperature is greater than the target temperature, Q3 will turn
off and the current through the load goes to zero, allowing the
object to cool back toward the ambient temperature. As the
target temperature is approached, a steady output current should
be reached. Naturally, a proper compensation network must be
found to ensure stability and adequate temperature settling time.
The P2 output from the ADN8830 should be left unconnected.
Suggested Pad Layout for CP-32 Package
Figure 25 shows the dimensions for the PC board pad layout for
the ADN8830, which is a 5
package. This package has a metallic heat slug that should be
soldered to a copper pad on the PC board. Although the pack-
age slug is electrically connected to the substrate of the IC, the
copper pad should be left electrically floating. This prevents
potential noise injection into the substrate while maintaining
good thermal conduction to the PC board.
Figure 24. Using the ADN8830 to Drive a Heating Element
Figure 25. Suggested PC Board Layout for CP-32
Pad Landing
CONTROLLING DIMENSIONS ARE IN MILLIMETERS; INCH DIMENSIONS
(IN PARENTHESES) ARE ROUNDED-OFF MILLIMETER EQUIVALENTS FOR
REFERENCE ONLY AND ARE NOT APPROPRIATE FOR USE IN DESIGN
THERMAL PAD SHOULD BE SOLDERED TO AN ELECTRICALLY FLOATING
PAD ON THE PC BOARD
(0.2110)
5.36
(0.0039)
N1
P1
0.10
(0.1488)
3.78
PVDD
NO CONNECTION TO P2 REQUIRED
Q1
Q2
L1
5, 32-lead lead frame chipscale
(0.1449)
C1
3.68
R
L
Q3
(0.0272)
0.69
ADN8830
(0.0110)
(0.0197)
PACKAGE
OUTLINE
OUT A
OUT B
N2
0.28
0.50