T1620000 Red Lion Controls, T1620000 Datasheet - Page 23
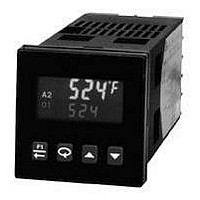
T1620000
Manufacturer Part Number
T1620000
Description
Process/Temperature Controller
Manufacturer
Red Lion Controls
Type
Temperaturer
Specifications of T1620000
Operating Temperature Max
50°C
Operating Temperature Min
0°C
Temperature Accuracy ±
0.3%
Output Voltage Max
7V
Output Voltage Min
4V
Controller Input
Thermocouple Or RTD
Brand/series
T16 Series
Dimensions
49.5mmW×49.5mmH×115.3mmD
Enclosure Rating
IP65
Input Type
RTD/Thermocouple
Ip Rating
IP65
Memory
EEPROM
Mounting Type
Panel
Output Type
Digital/SSR
Power, Rating
8 VA
Primary Type
Controller
Special Features
EEPROM
Standards
cURus, CE
Termination
Screw
Voltage, Supply
85 to 250 VAC
Thermocouple Type
J, K, T, E, R, S, B, N, C And Linear MV
Rohs Compliant
Yes
Lead Free Status / RoHS Status
Lead free / RoHS Compliant
PID Adjustments
calculated PID parameters. To do this, a chart recorder or data logging device is
needed to provide a visual means of analyzing the process. Compare the actual
process response to the PID response figures with a step change to the process.
Make changes to the PID parameters in no more than 20% increments from the
starting value and allow the process sufficient time to stabilize before evaluating
the effects of the new parameter settings.
MANUAL TUNING
between process cycles. This procedure is an alternative to the controller’s Auto-
Tune function. It will not provide acceptable results if system problems exist.
1. Set the Proportional Band (ProP) to 10.0% for temperature models (T16) and
2. Set both the Integral Time (Intt) and Derivative Time (dErt) to 0 seconds.
3. Set the Output Dampening Time (OPdP) in Output Module 2-OP to 0 seconds.
4. Set the Output Cycle Time [CYCt] in Output Module 2-OP to no higher than
5. Place the controller in Manual USEr Control Mode trnF in the Hidden Loop
6. Place the controller in Automatic (Auto) Control Mode trnF in the Hidden
In some applications, it may be necessary to fine tune the Auto-Tune
A chart recorder or data logging device is necessary to measure the time
100.0% for process models (P16).
one-tenth of the process time constant (when applicable).
and adjust the % Power to drive the process value to the Setpoint value.
Allow the process to stabilize after setting the % Power. Note: trnF must be
set to HidE in Parameter Lockouts Module 3-LC.
Loop. If the process will not stabilize and starts to oscillate, set the
Proportional Band two times higher and go back to Step 5.
PROCESS RESPONSE EXTREMES
23
control results or induced oscillations may cause system problems. In these
applications, Manual Tuning is an alternative.
7. If the process is stable, decrease Proportional Band setting by two times and
8. Fix the Proportional Band to three times the setting that caused the oscillation
9. Set the Integral Time to two times the period of the oscillation.
10. Set the Derivative Time to 1/8 (0.125) of the Integral Time.
11. Set the Output Dampening Time to 1/40 (0.025) the period of the oscillation.
In some unusual cases, the Auto-Tune function may not yield acceptable
change the Setpoint value a small amount to excite the process. Continue
with this step until the process oscillates in a continuous nature.
in Step 7.