CS1W-CN625 Omron, CS1W-CN625 Datasheet
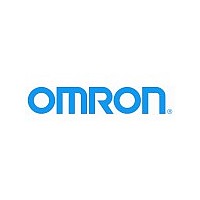
CS1W-CN625
Specifications of CS1W-CN625
Related parts for CS1W-CN625
CS1W-CN625 Summary of contents
Page 1
Cat. No. W445-E1-01 SYSMAC CXONE-AL@@C-E CX-Integrator ...
Page 2
CXONE-AL@@C-E CX-Integrator Operation Manual Produced February 2005 ...
Page 3
iv ...
Page 4
... OMRON. No patent liability is assumed with respect to the use of the information contained herein. Moreover, because OMRON is constantly striving to improve its high-quality products, the information contained in this manual is subject to change without notice ...
Page 5
vi ...
Page 6
Section 1 Overview 1-1 The CX-Integrator ........................................................................................................ 1-2 1-2 Specifications............................................................................................................... 1-8 1-3 Installation.................................................................................................................. 1-13 1-4 PLC Connecting Cables ............................................................................................ 1-14 1-5 Window Descriptions ................................................................................................. 1-21 1-6 Menus ........................................................................................................................ 1-33 Section 2 Basic Operations 2-1 Basic Procedures......................................................................................................... 2-2 2-2 Connecting Online ...
Page 7
Section 6 DeviceNet 6-1 DeviceNet Setting Procedures..................................................................................... 6-2 6-2 Setting Slave Parameters ............................................................................................ 6-4 6-3 Adding Slaves to the Master........................................................................................ 6-8 6-4 Setting Master Properties .......................................................................................... 6-13 6-5 Editing Master Parameters ........................................................................................ 6-15 6-6 Parameter Wizard ...................................................................................................... 6-16 6-7 Master ...
Page 8
About this Manual: This manual describes the installation and operation of CX-Integrator and includes the sections described below. Please read this manual carefully and be sure you understand the information provided before attempting to use the CX-Integrator. Be sure to ...
Page 9
... CXONE-AL@@C-E W446 WS02-CXPC1-E-V60 W447 WS02-CXPC1-E-V60 CS1G-CPU@@H CS1H-CPU@@H CJ1G- CPU@@H CJ1H- CPU@@H CJ1M- CPU@@ Manuals Related to DeviceNet Cat No. W267 --- W380 CS1W-DRM21(-V1) CJ1W-DRM21 W379 C200HW-DRM21-V1 CVM1-DRM21-V1 W381 3G8F7-DRM21 x Models Name CX-Integrator Operation Manual CX-One Setup Manual CX-Programmer Ver. 6.0 Operation Manual CX-Programmer Ver. 6.0 ...
Page 10
... LOSS OF PROFITS OR COMMERCIAL LOSS IN ANY WAY CONNECTED WITH THE PRODUCTS, WHETHER SUCH CLAIM IS BASED ON CONTRACT, WARRANTY, NEGLIGENCE, OR STRICT LIABILITY event shall the responsibility of OMRON for any act exceed the individual price of the product on which liability is asserted EVENT SHALL OMRON BE RESPONSIBLE FOR WARRANTY, REPAIR, OR OTHER CLAIMS ...
Page 11
... Application Considerations OMRON shall not be responsible for conformity with any standards, codes, or regulations that apply to the combination of products in the customer's application or use of the products. At the customer's request, OMRON will provide applicable third party certification documents identifying ratings and limitations of use that apply to the products. This information by itself is not sufficient for a complete determination of the suitability of the products in combination with the end product, machine, system, or other application or use ...
Page 12
... Performance data given in this manual is provided as a guide for the user in determining suitability and does not constitute a warranty. It may represent the result of OMRON's test conditions, and the users must correlate it to actual application requirements. Actual performance is subject to the OMRON Warranty and Limitations of Liability. The information in this manual has been carefully checked and is believed to be accurate ...
Page 13
xiv ...
Page 14
This section provides precautions for using the CX-Integrator. The information contained in this section is important for the safe and reliable application of the CX-Integrator. You must read this section and understand the information contained before attempting to use the ...
Page 15
Intended Audience 1 Intended Audience 2 Safety Precautions !Caution When performing any of the following operations, always check the network !Caution When changing the target PLC to any PLC other than the relay PLC, check Note !Caution When transferring ...
Page 16
Application Precautions General Communications Precautions DeviceNet Observe the following precautions when using the CX-Integrator. • Do not turn OFF the power to the PLC or disconnect the cable connecting the PLC when the CX-Integrator is online with the PLC. ...
Page 17
... Downloaded device parameters will be valid only after the devices are reset unless they are the OMRON CVM1-DRM21-V1, C200HW-DRM21-V1, CS1W-DRM21, or CJ1W-DRM21. • When the devices are reset, communications errors will temporarily occur. For this reason, do not reset the devices while the master-side PLC (CPU Unit) is operating. • ...
Page 18
Operating Environment Precautions !Caution Perform installation properly, according to the procedures described in this !Caution Do not install in the following locations: !Caution Take appropriate and sufficient countermeasures when installing in the 4 manual. • Locations subject to direct ...
Page 19
This section provides an overview of the CX-Integrator and describes CX-Integrator menus and connections. Communications Section 1 Overview ...
Page 20
The CX-Integrator 1-1-1 Overview 1-1 The CX-Integrator 1-1-1 Overview The CX-Integrator is a Programming Device software package that enables reading the PLC's network and serial network configuration from a personal computer via an online connection. This enables easily performing ...
Page 21
The network/serial communications configuration of a PLC other than the one originally connected to online to can be set as the target. The PLC that was originally connected to online (called the relay PLC, see note 1), is relayed through ...
Page 22
The CX-Integrator 1-1-2 Functions According to Network 1-1-2 Functions According to Network The functions for each network are listed in the following table. DeviceNet or CompoWay/F Controller Link or SYSMAC LINK Controller Link NT Link FINS networks, such as ...
Page 23
Accessible Network The network configuration of the target PLC (i.e., either the relay PLC or a PLC connected to the relay PLC) can be uploaded and monitored for each of the following networks. Accessible Networks Network Ethernet Controller Link ...
Page 24
The CX-Integrator 1-1-4 Accessible Network Local Network Table Requirements A local network table must be registered in the target PLC in the following cases. Communications Network communications Serial communications Note exception, local network tables are not required ...
Page 25
... Select Tools – Controller Link tool – Network diagnosis. Right-click the desired NS-series PT in the Network Configuration Window and select Start Special Application from the pop-up menu. Right-click the desired OMRON Temperature Controller in the Network Configuration Window and select Start Special Application from the pop-up menu. 1-1 ...
Page 26
Specifications 1-2-1 CX-Integrator Specifications 1-2 Specifications 1-2-1 CX-Integrator Specifications Item Model Provided in the CX-One FA Integrated Tool Package (CXONE-AL@@C-E). Setup media CD-ROM Applicable Computer IBM PC/AT or compatible computers CPU Pentium 133 MHz or better for Windows 98 ...
Page 27
Item PLCs that are Series Device type accessible as target CS Series CS1H PLCs CS1G/CJ1G CS1G-CPU45/44/43/42(-V1) Note: The target PLC CS1G-H is the PLC actually CS1H-H being accessed, e.g., to upload/download the PLC’s network configurations. CS1D-H CS1D-S CJ Series CS1G/CJ1G ...
Page 28
Specifications 1-2-1 CX-Integrator Specifications Item Communications Ethernet monitoring functions Controller Link SYSMAC LINK DeviceNet CompoWay/F NT Link Setting functions Ethernet Controller Link SYSMAC LINK DeviceNet CompoWay/F NT Link FINS networks, such as Ethernet, Controller Link, SYSMAC LINK, and DeviceNet ...
Page 29
Files Created by the CX-Integrator The following files can be created by the CX-Integrator. Files Contents Project files (.cin) Connection information to relay PLC, all network configurations for target PLC, and parameters for DeviceNet masters, DeviceNet slaves, and CompoWay/F ...
Page 30
... The device parameters of an OMRON DeviceNet Master Unit saved as an Open Network Controller DRM_UNIT (virtual unit) file The device parameters of an OMRON DeviceNet Master Unit saved as a NetX Server (NetX Server for DeviceNet) file The CX-Integrator does not support files created in the DeviceNet Configurator Ver. ...
Page 31
Installation The CX-Integrator is installed from the CX-One Installer. Refer to the CX-One Setup Manual (W444) for details. 1-3 Installation 1-13 ...
Page 32
... Host Link or (SYSWAY) compatible IBM PC/AT or compatible 14-pin 9-pin Built-in RS-232C port on CPU Unit or port on Serial Communications Board/Unit CS1W-CN225 (2.0 m) 9-pin CS1W-CN625 (6.0 m) 25-pin Built-in RS-232C port on CPU Unit or port on Serial Communications Board/Unit 9-pin Model Length Remarks CS1W-CN226/626 2 m/6 m --- XW2Z-200S-CV/500 2 m/5 m Connector ...
Page 33
... CS1W-CIF31 USB-Serial Conversion Cable. The driver software included with the CJ1W-CIF31 must be installed on the computer to use a USB port to connect the CX-Integrator. Refer to the PDF User’s Manual included with the CS1W-CIF31 USB-Serial Conversion Cable for details. 1-4 1-4-1 Direct Serial Connections to a PLC ...
Page 34
... XW2Z-200S-CV female /500S-CV (length: 2 m/5 m) D-sub 9-pin XW2Z-200S-V female /500S-V (length: 2 m/5 m) Connections diagrams are shown below. 1-16 Cable 1 CS1W-N226/626 CS/CJ-series Peripheral Port Programming Device Connecting Cable or CQM1H-CIF02 C-series Peripheral Port Programming + + Device Connecting Cable or XW2Z- @@@ RS-232C Programming Device Connecting Cable ...
Page 35
... Connecting to the Peripheral Port Using the CS1W-CN226/626 Connecting Cable USB A-plug connector, male CS1W-CIF31 D-sub connector (9-pin male) D-sub connector (9-pin female) Recommended cable: CS1W-CN226/626 Using the CQM1-CIF02 Connecting Cable CS1W-CIF31 D-sub connector (9-pin male) D-sub connector (9-pin female) Recommended cable: CQM1-CIF02 Note: Only a Host Link connection is possible for CS/CJ-series PLCs ...
Page 36
... Ethernet Ethernet port 1-18 CS/CJ-series PLCs Customizable Counter Units D-sub connector (9-pin male) or D-sub connector CS/CJ peripheral (9-pin female) connector CS1W-CN118 CS/CJ-series Ethernet Unit Ethernet Peripheral port CS/CJ-series relay PLC DeviceNet network ...
Page 37
... Controller Link Unit PCI Controller Link Support Board (See note.) Controller Link DeviceNet network Type Controller Link PCI-bus Support Board USB A-plug connector, male CS1W-CIF31 D-sub connector CS/CJ-series PLCs (9-pin male) D-sub connector (9-pin male) D-sub connector (9-pin female) Recommended cable: XW2Z-200S-CV/500S-CV or XW2Z-200S-V/500S-V (See note ...
Page 38
... D-sub 9-pin XW2Z-200S-CV female /500S-CV (length: 2 m/5 m) 1-20 Cable 2 Connector Connector Model CS/CJ Not needed. peripheral connector D-sub 9-pin D-sub 9-pin CS1W-CN118 male female (length: 0.1 m) Port Serial communic ations mode Connector (network type) CS/CJ Peripheral peripheral (Toolbus) connector ...
Page 39
Window Descriptions 1-5-1 Starting Methods The CX-Integrator can be started with any of the following three methods. 1) When using the CX-Programmer Ver. 6.0 or later, select Tools − Network Settings. 2) When using the CX-Programmer that was installed ...
Page 40
Window Descriptions 1-5-2 Main Window Window, Component List Window, and Outline Window. Moving a Window and Displaying the Window Separately Drag the window by its top border to move it. Closing a Window Click the X Button (Close Button) ...
Page 41
Online Connection Information Window The Online Connection Information Window displays the online/offline status and the Relay PLC’s communications settings. When online, the target PLC will be displayed in a tree structure with all of the Communications Units and ports that ...
Page 42
Window Descriptions 1-5-2 Main Window Communications Unit and Port Information for Target PLC The following CPU Unit built-in serial ports, Inner Boards, and Communications Units (referred to here as Communications Units/Ports) that are part of the target PLC are ...
Page 43
Online displayed. Online Connection Information Window Target PLC displayed in green. Note online connection is made to the relay PLC, the relay PLC will also be the target PLC by default. The icon will be displayed next to ...
Page 44
Window Descriptions 1-5-2 Main Window Display in Online Connection Information Window Online TargetPLC or TargetComponent *1 To connect the computer (CX-Integrator) directly to a CompoWay/F Slave through a serial connection, select CompoWay/F Device as the PLC model. Offline Displays ...
Page 45
Toolbus (peripheral) SYSMAC WAY (Host Link) SYSMAC LINK Ethernet Ethernet (FINS/TCP) FinsGateway Controller Link Example Toolbus Relay PLC’s CPU Unit Display item model Example [CS1H-CPU67H] Contents Relay PLC’s CPU Unit model 1-5 WAY) The Baud rate is communicatio displayed in ...
Page 46
Window Descriptions 1-5-2 Main Window Workspace Window The Workspace Window lists the networks displayed in the Network Configuration Window. Project name Workspace Window The icon to the left of the network that is currently connected and can be accessed ...
Page 47
Network Configuration Window When the network configuration is uploaded online from the target PLC, the network configuration will be displayed in this window network is inserted offline, the new network will be displayed in the Network Configuration Window. ...
Page 48
Window Descriptions 1-5-2 Main Window With DeviceNet, the node address, product name, and slave allocation status in the master will be displayed as shown below. Later, the component parameters in the virtual network that was created can be downloaded ...
Page 49
... Network Configuration Window. There are lists in the CPS and EDS Tabs. CPS Tab The Parts List shows the OMRON components that have had CPS files installed. The components are organized by component type in the directory tree format. A component can be added by selecting the desired component from the Parts List and then dragging and dropping it in the non-DeviceNet Network Configuration Window ...
Page 50
Window Descriptions 1-5-2 Main Window l DeviceType List The installed devices are organized by device type in this directory. The following device types are available. Device type Generic Purpose Discrete I/O Communications Adapter Human-Machine Interface AC Drives Position Controller ...
Page 51
Menus 1-6-1 Menus Main Sub-menu/command menu File New Open Close Save Save As Import Network Export Network DeviceNet Comment Component list Print Preview Print NewProject.smt Exit Edit Undo Redo Cut Copy Paste Delete Select All Toggle Position View Tool ...
Page 52
Menus 1-6-1 Menus Main Sub-menu/command menu View Zoom 200% 100% 75% 50% Properties Insert Network Component Insert TBranch Network Work Online Communication Settings Auto Online Change connection to the PLC Transfer [PC to Network] Transfer [Network to PC] Compare ...
Page 53
Main Sub-menu/command menu Network Parameter Edit Write Read Transfer [PC to Network] Transfer [Network to PC] Compare Move to upper network Move to lower network Rename Network Change Network Address Update Maintenance Information Compo- Parameter Wizard nent Edit Load Save ...
Page 54
Menus 1-6-1 Menus Main Sub-menu/command menu Compo- IO table nent Error Log Mode Setting Maintenance information Status/Error of Communication Unit Error Log of Communication Unit Resister to No applicable another device devices Change Node address I/O Comment Edit Device ...
Page 55
Main Sub-menu/command menu Close All Next Docked Previous Docked Cascade Tile Horizontally Tile Vertically Help Help Contents Online Registration About CX-Integrator Description Closes all windows. All networks Moves the focus to the next docked window. Moves the focus to the ...
Page 56
Menus 1-6-2 Popup Menus 1-6-2 Popup Menus Online Connection Information Window Popup Menu for the Relay PLC's Communications Settings The following popup menu will be displayed if you right-click the relay PLC’s communications settings line (starting with Offline) in ...
Page 57
Popup Menu for Communications Units/Ports under TargetDevice Online Popup menu Transfer [Network to PC] Uploads the communications configuration of the selected Communications Unit/port. Connect Enables accessing the selected Communications Unit/port. Start Data Link Starts the Data Link Component. (Controller Link ...
Page 58
Menus 1-6-2 Popup Menus Network Configuration Window Popup Menu for Components PLCs Popup menu Parameter Display Error Log Status/Error of Communication Unit Error Log of Communication Unit Connect to this PLC Toggle Position Copy Paste Delete Edit Name Edit ...
Page 59
Other Components Popup menu Parameter Edit Load Save Toggle Position Copy Paste Delete Edit Name Edit Node Address Start Special Start with Application Settings Inherited Start Only DeviceNet Networks Sub-menu/command Parameter Wizard Edit Load Save Upload Download Compare Description Edits ...
Page 60
Menus 1-6-2 Popup Menus Sub-menu/command Monitor Reset Maintenance information Resister to another device Export Comment list NX-Server DDE Setup File NX-Server ONC Setup File ONC DRM Unit Setup File Cut Copy Paste Delete Change Node Address Changes the selected ...
Page 61
Workspace Window Popup Menu for the Project Name or Network Popup menu Selected Open Network Insert Network Project name Delete Network Transfer [PC to Network] Transfer [Network to PC] Compare Connect Rename Network Change Network Address Copy Paste Project name ...
Page 62
Menus 1-6-2 Popup Menus Popup menu Selected Parameter Edit Network Load Save Transfer [PC to Network] Transfer [Network to PC] Compare 1-44 Description Offline Edits the network OK parameters of a virtual Controller Link network on the computer (Controller ...
Page 63
Toolbars The most commonly used functions are provided as icons on toolbars. The following menu commands are allocated to these icons. Icon Creates a new project. Opens a project file. Saves a project. Print. Print Preview. Undo. Redo. Cuts ...
Page 64
Menus 1-6-3 Toolbars Icon Reads parameters from device parameter files. Saves device parameters in files. Uploads device parameters. Downloads device parameters. Maintenance information Monitors supported network devices. Edits I/O comments. Displays device properties. Adds new EDS files. Deletes EDS ...
Page 65
This section describes the basic operations used for the CX-Integrator. Communications Section 2 Basic Operations ...
Page 66
Basic Procedures 2-1 Basic Procedures This section describes the overall procedures used for the CX-Integrator. Uploading Network Configurations Online Uploading Network Configurations from Target PLCs Other than the Relay PLC Reading Network Configurations and Parameters from Actual Networks and ...
Page 67
If the relay PLC has more than one Network Communications Unit (see note 1 normally necessary to create and transfer a local network table (see note 2). Select Tools − Start Routing Table to start the Routing Table ...
Page 68
Basic Procedures The following case is an exception to the rule that a local network table must be regis- Note tered if there are two or more Network Communications Units mounted. Overview: Procedure: Computer running CX-Integrator After connecting online ...
Page 69
Uploading Configurations from Target PLCs other than the Relay Network PLC The network configuration of another PLC can be read via the PLC that was first connected to the computer (known as the relay PLC). To read another PLC’s network ...
Page 70
Basic Procedures Reading Network Configurations and Parameters from Actual Networks and Saving Them to Files Online To simplify maintenance, the target PLC’s actual network configuration and all of the DeviceNet and CompoWay/F component parameters can be uploaded and saved ...
Page 71
Designing DeviceNet and CompoWay/F Networks Offline Networks can be designed on the CX-Integrator even before they have been installed. Parameters for individual DeviceNet masters and slaves can be set. Parameters for individual CompoWay/F slaves can be set. The specified parameters ...
Page 72
Basic Procedures Reading Saved Parameters and Downloading Them Online to DeviceNet or CompoWay/F Components All of the component parameters on a network can be downloaded to the actual components from a previously saved project file (.cin) after the network ...
Page 73
Directly Connecting the Computer Running CX-Integrator to CompoWay/F Components without Going Through a PLC Uploading the CompoWay/F network configuration is possible through a direction connection from the CX-Integrator to CompoWay/F protocol components using RS-232C or RS-485 communications without going through ...
Page 74
Connecting Online to the Relay PLC 2-2-1 Overview 2-2 Connecting Online to the Relay PLC 2-2-1 Overview To use the CX-Integrator, the computer must first connect online to a PLC connected though a direct serial connection or another PLC ...
Page 75
Procedures The online connection to the relay PLC can be established automatically (serial communications only) or manually. Automatic Online Connection (Serial Communications Only) If serial communications are being used, online connection can be performed automatically. For automatic connections, the ...
Page 76
Connecting Online to the Relay PLC 2-2-2 Procedures 3. If automatic connection with the PLC is successful, the online status and information on the connected PLC will be displayed in the Online Connection Information Window. Online displayed. Online Connection ...
Page 77
Item Device Name Relay Device (fixed) Device Type Series Device Type CS Series CS1H CS1G/CJ1G CS1G-H CS1H-H CS1D-H CS1D-S CS1G/CJ1G CJ Series CJ1M CJ1G-H CJ1H-H - CompoWay/F Device Network Type Select one of the following network types. Network type Toolbus ...
Page 78
Connecting Online to the Relay PLC 2-2-2 Procedures Toolbus Click the Driver Tab and set the following settings as required. Port Name: Baud Rate: Baud Rate Auto-Detect: Clear this selection to connect with the baud rate set on the ...
Page 79
Port Name: Select the computer’s COM port from the drop-down list. Baud Rate: Select the baud rate (bits/s) from the drop-down list. Data Format: Select the data length (data bits), parity, and number of stop bits from the pull-down ...
Page 80
Connecting Online to the Relay PLC 2-2-2 Procedures Field name on Item Network Tab Page FINS Source Network Address FINS Destination Network Address Node Frame Length Response Timeout Click the Driver Tab and set the following settings as required. ...
Page 81
... Clear this selection to enable using an IP address table or combined method. The workstation node address on the left can be input when the selection is cleared 254 Default IP address for the CS1W-ETN21/CJ1W-ETN21 Ethernet Unit: 192.168.250.FINS_node_address 1 to 65535 Default: 9600 2-17 ...
Page 82
Connecting Online to the Relay PLC 2-2-3 CPU Unit Troubleshooting For example, the PLC Errors Window above will be displayed when an I/O Table Setting Error has occurred in a CJ-series PLC. In this case, the registered I/O table ...
Page 83
Uploading Network Configurations and Checking for Communications 2-3 Uploading Network Configurations and Check- ing for Communications Unit Errors 2-3-1 Overview With the CX-Integrator, the actual network configuration including component parameters can be uploaded from the target PLC and displayed ...
Page 84
Uploading Network Configurations and Checking for Communications Unit Errors 2-3-2 Procedure NT Link Right-click a CPU Unit under TargetPLC in the Online Connection Information Window and select Connect or NT Link Auto Online Setting from the pop-up menu. NT ...
Page 85
Uploading Network Configurations and Checking for Communications The indicates that the network structure can be uploaded. The network configuration uploaded from the Unit will be displayed in the Network Configuration Window. 3. Check the connection status of the nodes. ...
Page 86
Uploading Network Configurations and Checking for Communications Unit Errors 2-3-2 Checking and Correcting Communications Unit Errors Note: The Communications Unit’s status and error information can be saved as a CSV file by clicking the Save Button, so the Communications ...
Page 87
Switching the Target PLC 2-4-1 Overview When an online connection is made from the CX-Integrator to the relay PLC, initially the same PLC will be both the relay PLC and the target PLC and the Communications Units and ports ...
Page 88
Switching the Target PLC 2-4-2 Procedure 3. Right-click a PLC on the network and select Connect to this PLC from the pop-up menu. Network Structure Window The selected PLC will be set as the target PLC. 4. Right-click a ...
Page 89
Creating Virtual Network Configura- 2-5 tions Offline 2-5-1 Overview For a DeviceNet or CompoWay/F network, the network configuration can be created offline, the component parameters can be set, and both the configuration and parameters can be saved in a network ...
Page 90
Creating Virtual Network Configurations Offline 2-5-2 Procedure For example, when CompoWay/F slaves, such as Temperature Controllers, are dragged and dropped, the communications unit number of the CompoWay/F slave is set. In the following example, a PLC CPU Unit model ...
Page 91
Creating Virtual Network Configurations Offline Connecting CompoWay Serial Port on a Serial Communications Board • Select the model number of the Serial Communications Board and click the OK Button. • The Unit Number Select Dialog Box will ...
Page 92
Creating Virtual Network Configurations Offline 2-5-2 Procedure DeviceNet Networks Adding the Master 1. Offline, select Insert − Network. The Select Network Dialog Box will be displayed. 2. Select DeviceNet and click the OK Button. 3. Select a device (component) ...
Page 93
Adding Slaves Slaves are added just like the master was, by dragging and dropping them from the Component List Window. Example of Devices Registered by Dragging and Dropping Devices can also be added to the network by right-clicking the ...
Page 94
Creating Virtual Network Configurations Offline 2-5-3 Changing Node Addresses 2-5-3 Changing Node Addresses Component − Change Node Address Node address between 0 and 63 will be automatically assigned to devices as they are added to the network. Use the ...
Page 95
Editing Components (Devices) Deleting Components (Devices) Edit - Delete Use the following procedure to delete a component from a network. 1 Select the component to be deleted. (More than one device can be selected.) 2 Select Edit. 3 Select ...
Page 96
Creating Virtual Network Configurations Offline 2-5-4 Editing Components (Devices) DeviceNet Networks Use the following procedure to change the display locations of DeviceNet components in the Network Configuration Window. 1 Right-click the device to be moved and drag it. 2 ...
Page 97
The Change Device Comment Dialog Box will be displayed. 4 Change the device comment and click the OK Button. Device comments can be displayed by moving the mouse pointer to the locations of devices in the Network Configuration Window. ...
Page 98
Manipulating Component Parameters 2-6-1 Overview 2-6 Manipulating Component Parameters 2-6-1 Overview With the CX-Integrator, the parameters on components in the Network Configuration Window can be set. They can also be uploaded from, downloaded to, and compared with the parameters ...
Page 99
The following list will be displayed if the down arrow is clicked in the Displayed Field. The following parameters can be set here: Communications settings for the peripheral and RS-232C ports and FINS protection settings across networks. Select the appropriate ...
Page 100
Manipulating Component Parameters 2-6-2 Procedure Parameter - Upload from the menu bar). The parameters will be uploaded from the actual component. Comparing To compare the component parameters set on the computer to those in the actual component, right-click the ...
Page 101
Uploading, Downloading, and Comparing Network Parameters 2-7 Uploading, Downloading, and Comparing Net- work Parameters 2-7-1 Overview With the CX-Integrator, the parameters of networks in the Workspace Window can be uploaded from, downloaded to, and compared with the parameters of ...
Page 102
Comparing Network Configurations 2-8-1 Overview 2-8 Comparing Network Configurations 2-8-1 Overview The configuration of a virtual network on the computer can be compared to the configuration of an actual network. The model numbers of all nodes are also compared. ...
Page 103
File Operations 2-9-1 Overview The following files can be saved and read by the CX-Integrator. File name Project files Network Network structure configuration files files Controller Link node files Component DeviceNet device parameter parameter files files CompoWay/F component parameter ...
Page 104
File Operations 2-9-2 Procedures 2-9-2 Procedures Saving Files Project Files (.cin) 1. Select File − Save or File − Save as from the menu bar. The Save As Dialog Box will be displayed. 2. Specify the directory and file ...
Page 105
Component Parameter Files DeviceNet Device Parameter Files (.dvf) 1. Select a device in a DeviceNet network in the Network Configuration Window. 2. Select Component – Network – Parameter - Write to file from the menu bar. CompoWay/F Component Parameter Files ...
Page 106
... Exporting Master Unit Device Parameters to Special Files Note Device parameters for OMRON DeviceNet Master Units and DeviceNet Units (CVM1-DRM21-V1, C200HW-DRM21-V1, and CS1W-DRM21(-V1)) can be exported to files for NetXServer for DeviceNet or DRM_UNIT files for Open Network Controllers. Use the following procedure to export device parameters for OMRON DeviceNet Master Units and DeviceNet Units ...
Page 107
Target PLC Online Operations 2-10 2-10-1 Overview With the CX-Integrator, the following operations are possible for the target PLC. • Creating, editing, and transferring I/O tables • Displaying CPU Unit errors • Changing the CPU Unit operating mode 2-10-2 Procedure ...
Page 108
Target PLC Online Operations 2-10-2 Procedure To upload the I/O tables, select Options − Transfer from the PLC from the menu bar. Displaying Current Errors and Error Logs (Online Only) If Error Log is selected, the PLC Errors Dialog ...
Page 109
Printing File − Print This section describes the procedure for printing device parameters and comments from the currently displayed network configuration. Use the following procedure to print print only part of the device parameters or comments, select ...
Page 110
This section describes how to set the routing tables. Communications Section 3 Routing Tables ...
Page 111
Routing Table Overview 3-1-1 Definition of Routing Tables 3-1 Routing Table Overview 3-1-1 Definition of Routing Tables To transfer data between networks necessary to create tables that specify the paths from the local PLC's Communications Units (such ...
Page 112
Relay Network Table The relay network table indicates the network address and node address of the first relay node when data is being sent to a destination network other than a network to which the PLC is connected. The destination ...
Page 113
Routing Table Overview 3-1-2 Network Conditions That Require Routing Tables 3-1-2 Network Conditions That Require Routing Tables Routing tables must be set for the following network conditions. Mounting Two or More Communications Units (See Note Single CPU ...
Page 114
Routing Table File Types Supported by the CX-Integrator The CX-Integrator supports the following two kinds of routing table files. File type FINS local routing table files FINS network routing table files When connecting online through Ethernet, the FINS network ...
Page 115
Routing Table Overview 3-1-5 Operating Procedures Prior to Routing Table Transfer 3-1-5 Operating Procedures Prior to Routing Table Transfer This section describes the operating procedures necessary to create the routing tables for the first time up to the point ...
Page 116
Operating Procedures Prior to Routing Table Transfer Creating the FINS Local Routing Tables Offline Start the Routing Table Component. (Start the PLC routing tables.) Select Tools – Start Routing Table from the CX-Integrator's menu bar. Select the type of ...
Page 117
Routing Table Overview 3-1-5 Operating Procedures Prior to Routing Table Transfer Procedures after Network Configuration Connect the CX-Integrator online to each node (CPU Unit) in the network, and read and edit each node's FINS local routing table in the ...
Page 118
Setting the Routing Tables 3-2-1 Routing Table Setting Example This section explains how to create and transfer the FINS local routing tables for the following network structure. Example: Routing from PLC1 to PLC3 Local node PLC1 Node address 1 ...
Page 119
Setting the Routing Tables 3-2-2 Creating the FINS Local Routing Tables 3-2-2 Creating the FINS Local Routing Tables This section shows how to set the routing tables (FINS local routing tables) for PLC1, which is connected directly to the ...
Page 120
Input the corresponding unit number and network address and click the OK Button. For PLC1, input unit number 0 and local network address 1. Input the appropriate settings in the local network tables for PLC2 and PLC3, as shown ...
Page 121
Setting the Routing Tables 3-2-2 Creating the FINS Local Routing Tables The local network table can also be set using the following procedure. Note 1. Click the Main View Tab and select Edit – Add SIOU. 2. The Enter ...
Page 122
When the local network table is set for the CPU Unit's built-in serial port, the serial port Communications Unit's unit number. Click the SIOU Tab Note: For an Inner Board, the Special I/O Unit number of the Board itself is ...
Page 123
Setting the Routing Tables 3-2-2 Creating the FINS Local Routing Tables The serial port's CPU SIOU value (unit number) is allocated automatically cannot Note be changed. The following FINS unit addresses (decimal) are allocated. Serial Communications Unit ...
Page 124
When the relay network table is set in the PLC Routing Table Window, the display automatically changes to the Main View format. Local node's unit number: 0 The relay network table can also be set using the following procedure. ...
Page 125
Setting the Routing Tables 3-2-2 Creating the FINS Local Routing Tables Offline Operations Creating the Local Network Table Offline Create the local network table for PLC1 offline. 1. Select Tools - Start Routing Table from the menu bar. 2. ...
Page 126
Setting the Gateway Counter Use the following procedure to set the gateway counter in the PLC. To set the gateway counter, the routing tables must be displayed in the PLC Routing Table Window. The gateway counter can be set ...
Page 127
Setting the Routing Tables 3-2-3 Setting the Gateway Counter Setting the Gateway Counter in a FINS Network Routing Table: 1. Click the Network Tab at the bottom of the PLC Routing Table Window, right-click the icon of a PLC ...
Page 128
More than 3 network layer crossings (8 max.) are allowed with CS/CJ-series Units with Note Version 2.0 or later ratings. However network layer crossings are allowed only when the destination of the FINS command is a CPU ...
Page 129
Setting the Routing Tables 3-2-4 Checking Routing Tables for Errors Crossing Network Layers with Version 2.0 and Later CS/CJ-series Units With Version 2.0 and later CS/CJ-series Units, FINS commands can cross over network layers (see note), ...
Page 130
Transferring Routing Tables Use the following procedure to transfer the routing tables that were created online or offline to PLC1. The computer must be directly connected to PLC1 and online. 1. Verify that PLC1 is connected directly to the ...
Page 131
Setting the Routing Tables 3-2-6 Saving Routing Tables 3-2-6 Saving Routing Tables Use the following procedure to save the created FINS local routing tables. The FINS local routing tables are saved in a file with the ".rtg" filename extension. ...
Page 132
Printing Routing Tables Use the following procedure to print the created routing tables. 1. Select File – Print in the PLC Routing Table Window. Example Printout (PLC1 Table View) Example Printout (PLC1 Main View) 3-2 Setting the Routing Tables ...
Page 133
Maintenance after Network Configuration 3-3-1 FINS Network Routing Tables 3-3 Maintenance after Network Configuration 3-3-1 FINS Network Routing Tables When the routing tables have been set and transferred to the nodes (CPU Units of the PLCs) in the network, ...
Page 134
When the PLC is connected online, the display will show green and red indicators on Note the Units that indicate errors with Units registered in the routing tables. Green Indicator: Unit exists in routing tables. Red Indicator: Error with Unit ...
Page 135
Maintenance after Network Configuration 3-3-2 Editing the FINS Local Network Tables Reading Routing Tables through the Network 1. Click the Network Tab in the workspace on the left side of the Window. 2. When each node (in the same ...
Page 136
Editing Routing Tables that Were Read 1. Click the Table View Tab and edit the local network table and relay network table. Transferring Edited Routing Tables 1. Specify each node (in the same network) and select Options – Transfer to ...
Page 137
Maintenance after Network Configuration 3-3-2 Editing the FINS Local Network Tables 3-28 ...
Page 138
Link and SYSMAC LINK) This section describes how to set data links for Controller Link and SYSMAC LINK networks. Communications Section 4 Data Links ...
Page 139
Overview 4-1-1 What Are Data Links? 4-1 Overview 4-1-1 What Are Data Links? Data links automatically exchange data in preset areas between nodes (PLCs and/or computers network. Settings can be made either manually or automatically. CX-Integrator operations ...
Page 140
Overview of Procedure by Data Link Setting Method Step 1: Selecting the Data Link Setting Method Either of the following methods can be used. 1) Select either user-set data links or automatically set data links after selecting Online - ...
Page 141
User Interface Overview 4-2-1 Starting the Data Link Component 4-2 User Interface Overview 4-2-1 Starting the Data Link Component The Data Link Component can be set with either of the following methods. Method 1: While online, right-click the Controller ...
Page 142
Menu Sub-menus /Commands LINK .csv – SYSMAC LINK data link tables (tab-delineated text file) Print Prints data link information. Print Preview Previews the data to be printed. Exit Exits the Datalink Component Window. View Move Right Moves the cursor to ...
Page 143
User Interface Overview 4-2-2 Datalink Component Toolbar (1) (2) (3) (4) No. (1) New (2) Show All Network Nodes (3) Open (4) Save (5) Toggle Network/Single Node Operation (6) Transfer to PLC (7) Transfer from PLC (8) Delete (9) ...
Page 144
Function Bar (1) (2) (3) No. Icon (1) F1: Help (2) F2: Node<->Table (3) F3: Link Start Address (4) F4: Move Up Area (5) F5: Move Down Area (6) F6: Show/Hide Offset (7) F7: Insert Area (8) F8: Delete Node ...
Page 145
Manually Setting Data Links 4-3-1 Procedure through Data Link Startup 4-3 Manually Setting Data Links Follow the procedure described below to create data link tables manually for Controller Link or SYSMAC LINK data links. Note: There is no need ...
Page 146
Creating Data Link Tables Create a data link table for each node registered in the CX-Server file that is read. Make the settings for (1) to (8) below. (3) Area setting (area/start address) (4) Send size (5) Node refresh ...
Page 147
Manually Setting Data Links 4-3-2 Creating Data Link Tables 2. Node Editing Window Settings (7) Set receive sizes from remote nodes. Note possible to add or delete nodes from the participating data link nodes (1) using ...
Page 148
System Configuration Example The procedure is described below, from data link creation through startup, taking a Controller Link data link system as an example. Peripheral Bus or Host Link PLC type CS1G-CPU45 Node address Data Link Setup Example Area ...
Page 149
Manually Setting Data Links 4-3-4 Creating Data Link Tables Offline 4-3-4 Creating Data Link Tables Offline First create manually set data link tables offline. Datalink Wizard Operations 1 While offline, select Tools - Start Data Link. The Select Network ...
Page 150
Select Table - Wizard. If data link tables have already been input, the following dialog box will be displayed. (It will not be displayed if these are the first data link tables being created.) 4 Click the Yes Button. ...
Page 151
Manually Setting Data Links 4-3-4 Creating Data Link Tables Offline No. Item (1) Node (2) PLC (3) Memory area (4) Start Address (5) Size (6) Status (7) Ordered Destination Nodes (8) Make Default (9) Next >> Note: The default ...
Page 152
Set node address 02 as shown in the following table. Item Node address PLC type Area 1 Memory area Start address Send size Area 2 Memory area Start address Send size Ordered destination nodes Data link status Memory area ...
Page 153
Manually Setting Data Links 4-3-4 Creating Data Link Tables Offline Fast Datalink Wizard Settings Note It is possible to generate a table with all nodes set for the same PLC type and the same areas (using Fast Default Table ...
Page 154
Node Editing Window Settings 10 The following Datalink Component Window will be displayed. Data Link Configuratio n window Node Editing window Data Link Configuration Window Participating data link node address Send areas are indicated by ovals in order of the ...
Page 155
Manually Setting Data Links 4-3-4 Creating Data Link Tables Offline Node Editing Window Settings Set the data link details for each node (i.e., send size, receive size, reception offset) in the Node Editing Window. Note: The Node Edit Window ...
Page 156
Node Editing Window (Edited Node Address: Node 01) Address at local node Address at remote node Indicates that the node refresh sequence It is also possible to display the Node Editing Window in list format, as before. Note Select View ...
Page 157
Manually Setting Data Links 4-3-4 Creating Data Link Tables Offline Size modifications and offsets can be set in the Area Specify Dialog Box that is Note displayed by double-clicking on the data link configuration icon (oval for send area ...
Page 158
Changing Node Refresh Sequences The node refresh sequence set for each node by the Datalink Wizard can be changed in the Node Editing Window. In the Node Editing Window, select the node for which the refresh sequence ...
Page 159
Manually Setting Data Links 4-3-4 Creating Data Link Tables Offline The node will be added. Deleting Nodes Added to the Data Links Select the node to be deleted from the Node Editing Window. Delete the node by clicking the ...
Page 160
Procedure Using Setup Example Set Area 1 for each node, based on the data link setup example in the example system configuration. Note: The receive size and reception offset can only be set for Controller Link, and not for ...
Page 161
Manually Setting Data Links 4-3-5 Procedure Using Setup Example Setting Node Address 02 Node address 02 is set in the same way as node address 01. Local node send area Receive area from remote nodes Setting Node Address 03 ...
Page 162
Checking Data Link Tables 1 Select Table - Validate Table in the Data Link Editor (Controller Link or SYSMAC LINK). The results of the check will be displayed as shown in the following illustration. 4-3-7 Printing Data Link Tables ...
Page 163
Manually Setting Data Links 4-3-8 Saving Data Link Tables 4-3-8 Saving Data Link Tables Follow the procedure below to save data link tables that have been generated. Data link tables are saved with a .cl3 file name extension as ...
Page 164
Reading CSV Files Files in CSV format can be read to data link tables. 1 While offline, select Tools - Start Data Link from the CX-Integrator menu bar. The Select Network Dialog Box will be displayed. 2 Select Controller ...
Page 165
Manually Setting Data Links 4-3-9 Creating, Reading, and Writing CSV Files (Saving) 3 Select File - Open menu bar, and then select *.csv from the File of Type Field. Writing CSV Files (Saving) Once data link tables have been ...
Page 166
Tag name (2) <node-p The node No. for the link. <node> aram> (Node No.) The PLC type for the node. <cpu> (PLC type) The CPU model for the node. <cpu-type> (CPU model) The status start address and the memory ...
Page 167
Manually Setting Data Links 4-3-9 Creating, Reading, and Writing CSV Files (Saving) Tag name (3) <area1> <start-type> (Link Area 1 type) <start-ch> (Link Area 1 start address) <link- area> (4) <area2> <start-type> (Link Area 2 type) <start-ch> (Link Area ...
Page 168
Creating, Reading, and Writing CSV Files (Saving) An example text data configuration for a CSV file is shown below. Note: Commas are used for delineation. (They are added when there are blank cells.) 4-3 Manually Setting Data Links 4-31 ...
Page 169
Manually Setting Data Links 4-3-10 Reading and Transferring Data Link Tables 4-3-10 Reading and Transferring Data Link Tables After a data link table has been created, follow the procedure below for reading it and transferring it to all nodes ...
Page 170
The data link tables will be read as shown below. Note: Before selecting Data Link Setup, make sure that the PLC can be connected online. 4-3 Manually Setting Data Links Reading and Transferring Data Link Tables 4-33 ...
Page 171
Manually Setting Data Links 4-3-11 Transferring the Data Link Table 4-3-11 Transferring the Data Link Table There are two methods that can be used to transfer data link tables. • Transfer data link tables to all PLC nodes on ...
Page 172
Operation If Errors Are Displayed OK Button clicked Ignore Errors Button clicked 4-3 Manually Setting Data Links 4-3-11 Transferring the Data Link Table The data link tables will not be transferred. An error message will be displayed if a node ...
Page 173
... The transfer results will be displayed. Changes in Transferring Data Link Tables during Data Link Operation Nodes can be added while data links are running if the following Controller Link Units/Boards and Repeater Units (CS1W-RPT01) are used (CX-Programmer version 3.2 or higher). • CS1W-CLK21-V1 • CS1W-CLK12-V1 • ...
Page 174
Use the following procedure to transfer data link tables while data links are running. 1. Create the new data link tables offline and save them in a file. 2. Place the CX-Integrator online with the PLC. 3. Select Tools - ...
Page 175
Manually Setting Data Links 4-3-11 Transferring the Data Link Table 9. Check the difference to be sure they are appropriate and then click the OK Button. A dialog box will be display to confirm data link table transfer. 10. ...
Page 176
Comparing Data Link Tables 1. In the node list in the Data Link Component, select the node address of the PLC for which data link tables are to be compared with those in the computer sure that Online ...
Page 177
Manually Setting Data Links 4-3-12 Starting and Stopping Data Links (Including Status Displays) 4-3-12 Starting and Stopping Data Links (Including Status Displays) Before performing the operations described below, connect online to a node where the data link table has ...
Page 178
Starting and Stopping Data Links (Including Status Displays) 3 Select Online - Datalink Operation/Status from the menu bar. The Datalink Status Dialog Box will be displayed. As shown below, the status of various items is displayed. The communications cycle ...
Page 179
Automatically Set Data Links 4-4-1 Procedure Through Data Link Startup 4-4 Automatically Set Data Links This section explains how to make the settings for automatically set data links. Make the settings in the Automatic Datalink (Controller Link) or Automatic ...
Page 180
Controller Link Automatic Setup 1 Before executing the following operations, connect online to the PLC that is serving as the startup node (making it the target PLC). Select Network - Work Online or Network - Auto Online from the ...
Page 181
... Chain type Applicable Models: • CS1W-CLK21-V1 • CS1W-CLK12-V1 • CS1W-CLK52-V1 • CJ1W-CLK21-V1 Note: Automatically set 1:N allocations are not possible for any models other than those listed above. Refer to the Controller Link Unit Operation Manual for details. 4-44 Setting Select Automatic ...
Page 182
Equality Layout (Previous Method) This is the previous automatic data link type where all nodes are allocated the same sizes of data links. A G (1) (3) (6) (5) H Equality Layout Settings Area 1 (5) Participating nodes (1) Area ...
Page 183
Automatically Set Data Links 4-4-2 Controller Link Automatic Setup Common Type (1) (4) (8) (7) Area 1 Master node (1) Area and Start Word 1 Area 1 (2) Master size 2 (3) Slave size 3 (Same as (3).) (Same ...
Page 184
Participating nodes Master node (1) Area and Start Word 1a 1a (2) Master, Common Send Words 1b 1b (3) Master, Individual Send Words 1c 2 (Same as (3)). 1d (Same as (3)). (4) Slave, Send Words 2 3 (Same ...
Page 185
Automatically Set Data Links 4-4-3 SYSMAC LINK Automatic Setup 4-4-3 SYSMAC LINK Automatic Setup 1 Before executing the following operations, connect online to the PLC that is serving as the startup node (making it the target PLC). Select Network ...
Page 186
Transferring Automatic Data Link Setup Parameters to the Startup Node Word Allocations for SYSMAC LINK Automatic Setup (Example: CS/CJ Series, CVM1/CV Series) Note CIO Area (words) CIO 1000 to CIO 1003 D00000 to D00007 CIO 1004 to CIO 1007 ...
Page 187
Automatically Set Data Links 4-4-4 Transferring Automatic Data Link Setup Parameters to the Startup Node • The data link mode (manual/automatic) and data link operation are determined by the Note data link setup at the startup node. With automatic ...
Page 188
Monitoring Data Link Status Monitoring Data Link Status, Such as Communications Cycle Time 1 Select Network - Work Online from the menu bar to connect online. 2 Select Tools - Start Data Link. 3 Select Controller Link or SYSMAC ...
Page 189
Automatically Set Data Links 4-4-5 Monitoring Data Link Status Note: Supported for CVM1 and CV-series SYSMAC LINK Units only. The following items can be monitored for a particular SYSMAC LINK Unit. Tag name General Error Information Network Status Data ...
Page 190
Place the CX-Integrator online with the data link start node displayed above. 6. Reconnect the CX-Integrator online and open the Data Link Component. 7. Select Online - Start Data Link from the Data Link Component menu bar. The Automatic ...
Page 191
Automatically Set Data Links 4-4-5 Monitoring Data Link Status 4-54 ...
Page 192
Section 5 Controller Link Network Diagnostic Tool This section explains the operations of the Controller Link Network Diagnostic Tool. Communications ...
Page 193
Diagnostic Functions and Flowcharts 5-1-1 Introduction 5-1 Diagnostic Functions and Flowcharts 5-1-1 Introduction The Controller Link Network Diagnostic Tool can perform a variety of diagnostic operations, such as checking the operating status of a Controller Link network made up ...
Page 194
Operational Flowchart 1. Connect 2. Start Using a CS/CJ-series PLC in a Toolbus network (see note): Note: If the PLC is a CS/CJ-series model and the network type is Toolbus, it isn’t necessary to set the PLC connection. The ...
Page 195
Diagnostic Functions and Flowcharts 5-1-4 Components of the Network Diagnosis Tool Window 5-1-4 Components of the Network Diagnosis Tool Window This section describes the various components of the Controller Link Network Diagnostic Tool Window. Main Window Component Names and ...
Page 196
Diagnosing Network Status 5-2-1 Description of Network Status A list of the nodes participating in the specified network is displayed to show the network status. The operating status of the CPU Unit or Controller Link Unit/Board is diagnosed and ...
Page 197
Diagnosing Network Status 5-2-2 Diagnosing Network Status 5-2-2 Diagnosing Network Status 1. Check that the CX-Integrator is online with the PLC connected through Controller Link ad select Tools – Controller Link tool – Network Diagnosis. 2. The Select Network ...
Page 198
Network Status Diagnosis Example The following window shows the results of an example network status diagnosis. • Nodes are displayed in the order of node addresses, not in the order they are physically connected. • The background of the ...
Page 199
Diagnosing Network Status 5-2-3 Network Status Diagnosis Example Errors shown in the diagnosis results area can be double-clicked to display details on Note the error. When this is done, the contents of the Auxiliary Area or AR and SR ...
Page 200
Node Icons Node address Name that is specified in the node file Displayed Icons The icon that is displayed depends on the model of the PLC, as shown below. Node icon A computer will be displayed when a Controller ...