XW2Z-200J-B1 Omron, XW2Z-200J-B1 Datasheet
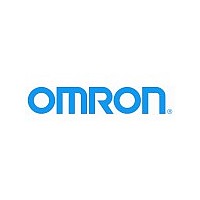
XW2Z-200J-B1
Specifications of XW2Z-200J-B1
XW2Z-200J-B1 Summary of contents
Page 1
Cat. No. O010-E1-01 FQM1 Series FQM1-CM001 FQM1-MMP21 FQM1-MMA21 Flexible Motion Controller OPERATION MANUAL ...
Page 2
FQM1 Series FQM1-CM001 FQM1-MMP21 FQM1-MMA21 Flexible Motion Controller Operation Manual Produced November 2004 ...
Page 3
iv ...
Page 4
... OMRON. No patent liability is assumed with respect to the use of the information contained herein. Moreover, because OMRON is con- stantly striving to improve its high-quality products, the information contained in this manual is subject to change without notice ...
Page 5
vi ...
Page 6
TABLE OF CONTENTS PRECAUTIONS . . . . . . . . . . . . . . . . . . . . . . . . . . . . . . . . . . . xiii ...
Page 7
Power OFF Operation . . . . . . . . . . . . . . . . . . . . . . . . . . . . . . . . . . . . ...
Page 8
TABLE OF CONTENTS SECTION 10 Inspection and Maintenance . . . . . . . . . . . . . . . . . . . . . . . . . 259 10-1 Inspections . . . . ...
Page 9
TABLE OF CONTENTS ...
Page 10
... O011 Describes the ladder diagram programming instruc- tions supported by FQM1-series Flexible Motion Con- troller. Use this manual together with the Operation Manual (Cat. No. O010). W437 Provides information on how to use the CX-Program- mer, a Windows-based programming and monitoring package for OMRON PLCs. xi ...
Page 11
xii ...
Page 12
This section provides general precautions for using the FQM1-series Flexible Motion Controller and related devices. The information contained in this section is important for the safe and reliable application of the FQM1-series Flexible Motion Controller. You must read this section ...
Page 13
... It is extremely important that the FQM1 be used for the specified purpose and under the specified conditions, especially in applications that can directly or indirectly affect human life. You must consult with your OMRON representa- tive before applying a FQM1 System to the above-mentioned applications. 3 ...
Page 14
Safety Precautions !WARNING Fail-safe measures must be taken by the customer to ensure safety in the event of incorrect, missing, or abnormal signals caused by broken signal lines, momentary power interruptions, or other causes. Not doing so may result in ...
Page 15
Safety Precautions !Caution The operating environment of the FQM1 System can have a large effect on the longevity and reliability of the system. Improper operating environments can lead to malfunction, failure, and other unforeseeable problems with the FQM1 System. Make ...
Page 16
Safety Precautions • Outputs may remain ON due to a malfunction in the built-in transistor out- puts or other internal circuits countermeasure for such problems, external safety measures must be provided to ensure the safety of the system. ...
Page 17
Safety Precautions xviii • Do not apply voltages or connect loads to the built-in outputs in excess of the maximum switching capacity. Excess voltage or loads may result in burning. • Disconnect the functional ground terminal when performing withstand voltage ...
Page 18
... EMC Directives • Low Voltage Directive EMC Directives OMRON devices that comply with EC Directives also conform to the related EMC standards so that they can be more easily built into other devices or the overall machine. The actual products have been checked for conformity to EMC standards (see the following note) ...
Page 19
Conformance to EC Directives 4-5 Relay Output Noise Reduction Methods Countermeasures Countermeasure Examples Circuit Current AC DC Yes Yes CR method C R Power supply xx The FQM1-series Flexible Motion Controller conforms to the Common Emis- sion Standards (EN61000-6-4) of ...
Page 20
... XW2B-80J7-1A Controller Connect- XW2Z-050J-A28 ing Cables XW2Z-100J-A28 XW2Z-050J-A30 XW2Z-100J-A30 XW2Z-050J-A31 XW2Z-100J-A31 Required element The reversed dielectric strength value of the diode must be at least 10 times as large as the circuit voltage value. The forward current of the diode must be the same as or larger than the load current ...
Page 21
Data Backup 5 Data Backup Note xxii The user programs, I/O memories, and other data in the Coordinator Module and Motion Control Modules is backed up either by a super capacitor or flash memory, as listed in the following table. ...
Page 22
Data Backup Backing Up DM Area Data in Flash Memory mentary power interruptions. For operating parameters and other long- term data, use the portion of DM Area stored in flash memory in the Coor- dinator Module and transfer it to ...
Page 23
Data Backup xxiv 5 ...
Page 24
This section describes the features of the FQM1 and its system configuration. 1-1 Outline of FQM1 Flexible Motion Controller . . . . . . . . . . . . . . . . . . . . . ...
Page 25
Outline of FQM1 Flexible Motion Controller 1-1 Outline of FQM1 Flexible Motion Controller PT (Monitor parameter or settings) Coordinator Module Power Supply Unit Peripheral port RS-232C port Servo Relay Units CX-Programmer Flexible Configurations Axes High-speed Processing ...
Page 26
Outline of FQM1 Flexible Motion Controller Coordinator Module CX- Programmer Periph- Ladder eral port program RS-232C PT, host computer, etc. Normal I/O Built-in RS-232C Port in A Programmable Terminal (PT) can be connected to the Coordinator Module Coordinator Module to ...
Page 27
FQM1 Configuration Pulse Input Frequency Measurement Function Wide Variety of Interrupt Functions High-speed Analog I/O Supported Writing and Monitoring Ladder Programs Note 1-2 FQM1 Configuration Coordinator Module Power Supply Unit Peripheral port RS-232C port CX-Programmer Note 4 The speed of ...
Page 28
FQM1 Configuration FQM1-CM001 Coordinator One Coordinator Module is required in an FQM1. The Coordinator Module Module provides the following: I/O: Program capacity: 5 Ksteps DM Area capacity: 32 Kwords (DM) FQM1-MMP21/MMA21 Each Motion Control Module provides the following: Motion Control ...
Page 29
... Serial communi- • Peripheral port: Peripheral bus (for CX-Programmer) cations • One RS-232C port: NT Link (for OMRON PTs), Host Link (for host computers pro- tocol (for PLCs) • One RS-422A port (Same connector as general-purpose I/O): 1:N communications with Servo Drivers (for transferring parameters to Servo Drivers) ...
Page 30
Modules Outline of Internal Data Exchange and I/O Coordinator Motion Control Module Module #1 Ladder program Ladder program CX-Programmer DM Peripheral port RS-232C PT 16 inputs 12 inputs 8 outputs 8 outputs RS-422A PLC (for parameter settings) Coordinator • Peripheral ...
Page 31
CX-Programmer 1-4 CX-Programmer The CX-Programmer provides software functions for programming and debugging. FQM1 Patch Software must be installed for the CX-Programmer Ver. 5.0 (Model: WS02-CXPC1-E-V50) to use it to create ladder programs, make set- tings in the System Setup, and ...
Page 32
... High-speed communications with Programmable Terminals via direct access Communications between the CX-Programmer running on a computer and the FQM1 Communications between OMRON PLC and the FQM1 Communications between a PT and W-series or SMARTSTEP Servo Drivers via the FQM1 Section 1-5 Applicable commands and communications ...
Page 33
Expanded System Configuration Host Link System The Host Link System allows the I/O memory of the Modules to be read/writ- ten and the operating mode to be changed from a host computer (personal computer or Programmable Terminal (PT)) by executing ...
Page 34
Expanded System Configuration Note Serial PLC Link Slave Note Set the PT communications settings for a 1:N or Standard NT Link Link System is possible for either the peripheral port or the RS-232C port. NT Link 1:N Mode ...
Page 35
... NS-series PT or computer application running on CX-Server. The serial communications mode for the RS-422A port on the FQM1 Coordinator Mod- ule is set to Serial Gateway to achieve this. OMRON’s W-series or SMARTSTEP Servo Drivers can be connected. Smart Active Parts on an NS-series PT connected via an NT Link can be used to access W-series or SMARTSTEP Servo Drivers. ...
Page 36
Basic Operating Procedure No-protocol (Custom) Communications System via RS-422A Port 1-6 Basic Operating Procedure 1,2,3... NS-series PT Smart Active Parts NT Coordinator Module Link FQM1 Protocol Servo parameters conversion RS-422A W-series or SMART STEP Servo Driver No-protocol communications allow simple ...
Page 37
Basic Operating Procedure 14 Wiring I/O terminals and connectors. Refer to 3-3 Wiring Module Connec- tors for details. 3. Initial Hardware Settings Set the DIP switch on the front of the Coordinator Module as required. Re- fer to 2-3 Coordinator ...
Page 38
Basic Operating Procedure 1-6-1 Examples 1. Installation Connect the Power Supply Unit, Coordinator Module, Motion Control Mod- ules, and End Module to assemble the FQM1. Make sure that the total power consumption of the Modules is less than the maximum ...
Page 39
Basic Operating Procedure 4. Turning ON Power and Checking Initial Operation Note The System Setup and user programs are backed up in built-in flash memory. When the data is being backed up, a message indicating the data is being transferred ...
Page 40
Basic Operating Procedure 7. Transferring the Programs 8. Testing Operation 8-a) I/O Wiring Checks 8-b) Trial Operation 8-c) Monitoring and Debugging When the programs has been created in the CX-Programmer, they must be transferred to the Motion Control Modules through ...
Page 41
Basic Operating Procedure 1,2,3... 1. Select the bit for differential monitoring. 2. Select Differential Monitor from the PLC Menu. The Differential Monitor 3. Select Rising or Falling. 4. Click the Start Button. The buzzer will sound when the specified change ...
Page 42
Function Tables Arranged by Purpose 1-7 Function Tables Arranged by Purpose 1-7-1 Sync Cycles and Synchronized data Purpose Synchronizing 3 Simple control Synchronizing or more axes of all axes oper- all Motion Con- ations from the trol Modules to Coordinator ...
Page 43
Function Tables Arranged by Purpose Purpose Synchronizing 3 Make control or more axes cycle as short as possible with Modules syn- chronized Control opera- tion using pulse and analog data simultaneously Fast control loops 20 Operation Function used Synchronizing Sync ...
Page 44
Function Tables Arranged by Purpose 1-7-2 Position and Speed Control Purpose PTP positioning Using Servo using pulse I/O Driver compati- ble with an incremental encoder or step- ping Servomo- tor/Servo Driver Using Servo Drivers compati- ble with an Absolute Encoder ...
Page 45
... Functions for Servo Drivers Compatible with Absolute Encoders Set counter operation to Absolute Linear (CW−), Absolute Circular, or Absolute Linear (CW+). Uses OMRON W-series Servo Drivers and reads the absolute position from the Servo Driver before operation starts. Once the origin has been set easier to find the origin by reading the absolute position before operation starts ...
Page 46
Function Tables Arranged by Purpose Purpose PTP positioning Simple position- Stepped or using analog I/O ing using invert- sloped analog ers output corre- sponding to the high-speed counter PV Path control Drawing path Executing elec- with linear inter- tronic cam ...
Page 47
Function Tables Arranged by Purpose Purpose Synchronous Slave axis con- control trol synchro- nized to virtual axis. Control of a par- ticular axis oper- ation at a speed with a uniform ratio applied Speed control Creating any trapezoidal speed control ...
Page 48
Function Tables Arranged by Purpose Purpose Speed control Torque control (position + torque control) Individual axis control for mold- ing equipment and similar applications Line control (winding/feed- ing control) Tension control, etc. Simple speed control corre- sponding to time axis ...
Page 49
Function Tables Arranged by Purpose Purpose Detecting speed Detecting speed using rotary and use in out- encoder inputs put control while managing posi- tion using encoder inputs Monitoring speed while managing work- piece position using encoder input 1-7-4 High-speed Analog ...
Page 50
Function Tables Arranged by Purpose Purpose Control using Judgment pro- measurement cessing based results for undu- on measure- lation, distortion, ment results thickness, height, diame- ter, etc object Position control using measure- ment results Responding Changing ana- quickly ...
Page 51
Function Tables Arranged by Purpose 1-7-5 Controlling Timing Purpose Responding Executing pro- Starting inter- quickly to exter- cessing as soon rupt processing nal signals and as change in when an input operate external input bit turns ON signal detected and/or ...
Page 52
Function Tables Arranged by Purpose Purpose Operation with Increasing accu- High-precision highly precise racy of external ON outputs, with timing output ON time. minimum unit of (Feeding, hole 0.01 ms opening, tape winding, gluing, and other appli- cations) Highly accurate ...
Page 53
Function Tables Arranged by Purpose 30 Section 1-7 ...
Page 54
This section provides the specifications of the FQM1 and describes the parts and their functions on the Coordinator Module and Motion Control Modules. 2-1 List of Models . . . . . . . . . . . . . ...
Page 55
List of Models 2-1 List of Models Name Type Coordinator Mod- Standard ule (with built-in I/O) Motion Control Pulse I/O Modules Analog I/O End Module Standard Servo Relay Units --- FQM1 Flexible Set for pulse I/O Motion Controller Set Set ...
Page 56
General Specifications Note Power Supply Unit Specifications Item Power Supply Unit CJ1W-PA205R Supply voltage 100 to 240 V AC (wide-range), 50/60 Hz Operating voltage 85 to 264 V AC and frequency ranges Power consumption 100 VA ...
Page 57
Coordinator Module Note 2-3 Coordinator Module Nomenclature CM001 FLEXIBLE RDY MOTION RUN CONTROLLER ERR PRPHL ON COMM1 COMM2 1 PERIPHERAL Peripheral port PORT RS-232C port 39 Coordinator Module Note Cover the peripheral port and RS-232C port with the supplied covers ...
Page 58
Coordinator Module Switch on Front Panel Peripheral Port Baud Rate Detection/System Setup Switch Function Specifications Item Control method I/O control method Programming Instruction length Ladder instructions Execution time Basic instructions Special instructions 0.3 µs min. Common processing (overhead) time Program ...
Page 59
Coordinator Module Item CIO Area Input Bit Area Output Bit Area Cyclic Refresh Bit Area Synchronous Data Link Bit Area Serial PLC Link Bit Area Work Bit Areas CIO Area Work Area Auxiliary Area Read/Write Error Log Temporary Area Holding ...
Page 60
Motion Control Modules Item RUN output Individual func- Serial communica- tions tions I/O Specifications Built-in General-purpose I/O Inputs 2-4 Motion Control Modules Motion Control Module FQM1-MMP21 (Pulse I/O) Item I/O Pulse I/O Pulse inputs: 2 (compatible with Servo Drivers with ...
Page 61
Motion Control Modules FQM1-MMA21 (Analog I/O) Item I/O Pulse inputs Pulse inputs: 2 (compatible with Servo Drivers with absolute encoders) Analog I/O • Analog inputs: 1 (− ...
Page 62
Motion Control Modules Performance Specifications Item Control method Stored program I/O control method Cyclic scan Programming language Ladder diagram Instruction length steps per instruction Number of instructions Approx. 270 0.1 µs min. Instruction Basic instructions execution Special ...
Page 63
Motion Control Modules Item Power interruption hold function Super capacitor (momentary power interruption) Memory backup Super capacitor backup Flash memory Trace memory 4,000 words Peripheral servicing Event requests from Coordinator Module Self-diagnosis function CPU errors (WDT) and memory errors Program ...
Page 64
Motion Control Modules Pulse I/O Specifications FQM1-MMP21 (Pulse I/O) Item Pulse Number of counters 2 inputs Counter operations Linear counter and circular counter Input signals Two words each for phase A, phase B, and phase Z. Signal levels 24 V ...
Page 65
Motion Control Modules Pulse Inputs and Analog I/O Specifications 42 FQM1-MMA21 (Analog I/O) Item Pulse Number of counters 2 inputs Counter operations Linear counter, circular counter Input signals Two words each for phase A, phase B, and phase Z. Signal ...
Page 66
Dimensions 2-5 Dimensions FQM1-CM001 Coordinator Module 90 mm FQM1-MMP21/MMA21 Motion Control Modules 90 mm FQM1-TER01 End Module 2 CM001 FLEXIBLE RDY MOTION RUN CONTROLLER ERR PRPHL ON OFF COMM1 COMM2 1 2 PERIPHERAL CN1 PORT RS422 ...
Page 67
Dimensions Power Supply Units 44 CJ1W-PA202 65 81.6 CJ1W-PA205R 65 81.6 Section 2-5 PA202 POWER L1 AC100 -240V INPUT L2 PA205R POWER L1 AC100-240V INPUT L2/N 90 RUN OUTPUT AC240V DC24V 80 ...
Page 68
Module Current Consumption XW2B-80J7-1A Servo Relay Unit Signal switches 100 90 41.7 15.9 2-6 Module Current Consumption The amount of current/power that can be supplied to the Modules mounted in the FQM1 is limited. Refer to the following tables when ...
Page 69
Module Current Consumption Motion Control Modules Motion Control Module Current Consumption for 24-V Systems Motion Control Module Analog I/O Example Calculation Example for CJ1W-PA202 Power Supply Unit with the Following Modules of Current and Power Mounted Consumption Coordinator Module Motion ...
Page 70
Memory Block Diagram 2-7 Memory Block Diagram Note Coordinator Module and Motion Control Module memory has the following block configurations. • I/O Memory Area: Memory accessible from user programs. • User Memory (UM): User programs and parameter area (See note ...
Page 71
Memory Block Diagram 48 Section 2-7 ...
Page 72
This section describes how to install and wire the FQM1. 3-1 Installation ...
Page 73
Installation 3-1 Installation 3-1-1 Installation and Wiring Precautions Be sure to consider the following factors when installing and wiring the FQM1 to improve the reliability of the system and make the most of the FQM1’s func- tions. Ambient Conditions Do ...
Page 74
Installation Improving Noise Resistance • The FQM1 will be easiest to install and operate mounted at a height of about 1.0 to 1.6 m. • Do not mount the FQM1 in a control panel containing high-voltage equip- ...
Page 75
Installation FQM1 Orientation PA202 AC100 -240V INPUT 52 • The FQM1 must be mounted in an upright position to provide proper cool- ing. CM001 RDY RDY FLEXIBLE POWER MOTION RUN RUN CONTROLLER ERR ERR PRPHL ON OFF IN OUT COMM1 ...
Page 76
Installation 3-1-2 Installation in a Control Panel The FQM1 must be mounted inside a control panel on DIN Track. L1 AC10 0 -240V INPU T L2 Note The FQM1 must be mounted on DIN Track. It cannot be ...
Page 77
Installation Routing Wiring Ducts Install the wiring ducts at least 20 mm away from the FQM1 and any other objects, (e.g., ceiling, wiring ducts, structural supports, and devices) to pro- vide enough space for air circulation and replacement of Modules. ...
Page 78
Installation Assembled Dimensions PA202 CM001 RDY FLEXIBLE POWER MOTION RUN CONTROLLER ERR PRPHL ON OFF COMM1 COMM2 1 2 PERIPHERAL L1 AC100 -240V INPUT L2/N CN1 PORT NC RS422 × ...
Page 79
Installation Installation Height The installation height of the FQM1 varies from 115 to 165 mm. When a CX-Programmer or connecting cables are connected, however, even greater height is required. Allow sufficient depth in the control panel contain- ing the FQM1. ...
Page 80
Installation 2. Move the yellow sliders at the top and bottom of each Module until they L1 AC10 0 -240V INPU T L2 Note If the locking tabs are not secured properly, the FQM1 may not function prop- ...
Page 81
Installation 2. Fit the back of the FQM1 onto the DIN Track by inserting the FQM1 onto 3. Lock the pins on the backs of the Modules. 4. Install a DIN Track End Plate on each end of the FQM1. ...
Page 82
... Installation DIN Track and Use the DIN Track and DIN Track End Plates shown below. Accessories Secure the DIN Track to the control panel using M4 screws separated by 210 mm (6 holes) or less and using at least 3 screws. The tightening torque is 1.2 N·m. PFP-100N2 DIN Track 4 ...
Page 83
Wiring 3-2 Wiring 3-2-1 Wiring Power Supply Units AC power supply 100 to 240 V Note The RUN output function is provided only for the CJ1W-PA205R Power Sup- ply Unit not provided on the CJ1W-PA202 Power Supply Unit. ...
Page 84
Wiring Terminal Screws and The terminals on the Power Supply Unit use M4, self-raising terminal screws. Crimp Terminals Note !Caution Tighten AC power supply terminal block screws to a torque of 1.2 N·m. Loose screws may cause shorts, malfunctions, or ...
Page 85
Wiring 62 • noise-filtered neutral terminal. If noise is a significant source of errors and to prevent electrical shocks, connect the line ground terminal to the ground terminal and ground both with a ground resistance of less ...
Page 86
Wiring Terminal Screws and The terminals on the Power Supply Unit use M4 self-raising terminal screws. Crimp Terminals Note Crimp Terminals for Ground Wire 7 mm max. FQM1 Other equipment Ground to Ground to 100 Ω or ...
Page 87
Wiring 3-2-2 RS-232C Port Wiring Connector Pin Arrangement Connector hood FG Note Do not connect the 5-V power supply on pin number 6 of the RS-232C port to any devices other ...
Page 88
... Fujikura Ltd.: Hitachi Cable, Ltd.: UL2464-SB (MA) 5P × 28AWG (7/0.127) (UL product) Note Use the special cables provided from OMRON for all connections whenever possible. If cables are produced in-house, be sure they are wired correctly. External devices and the Coordinator Module may be damaged if general-pur- pose (e ...
Page 89
... 9-pin D-sub (male) • Communications Mode: NT Link (1: node only) • OMRON Cables with Connectors: XW2Z200T (2 m) Item Communications method Half duplex Synchronization Asynchronous Baud rate 0.3, 0.6, 1.2, 2.4, 4.8, 9.6, 19.2, 38.4, or 57.6 kbps (See note.) Transmission distance 15 m max. ...
Page 90
Wiring Module Connectors 3-3 Wiring Module Connectors 3-3-1 Connector Pin Arrangement The following tables provide the connector pin arrangement for FQM1 Mod- ules. FQM1-CM001 Coordinator Module General-purpose I/O 40-pin Connector Pin Name No. 1 External input 0 3 External input ...
Page 91
Wiring Module Connectors FQM1-MM@21 Motion Control Modules General-purpose I/O 26-pin Connector Pin Name No. 26 Not used. 24 External input 0 (interrupt input) 22 External input 1 (interrupt input External input 2 (interrupt input) 18 External input ...
Page 92
Wiring Module Connectors Pin No. Name 23 Counter 1 SEN SEN output output signal for absolute Servo Driver 25 SEN_0 V 27 5-V power for SEN output 29 Pulse 1 CW+ 31 CW− 33 CCW+ 35 CCW− 37 One-shot pulse ...
Page 93
Wiring Module Connectors Pin. Name No. 33 Analog input Voltage input (+) 35 Voltage input (−) 37 Analog output 1 Voltage output (+) 39 Voltage output (−) Note Connect the voltage input (+) and the current input when using with ...
Page 94
Wiring Module Connectors 3-3-3 Wiring Examples Connecting Pulse Inputs (FQM1-MMP21/ MMA21) Port 1 Port 2 Signal name Pin number Pin number ( (6) Encoder input (11 (12) ...
Page 95
... Power supply Encoder A+ A− B+ B− Z+ Z− Connecting a Servo Driver (OMRON's W Series) Compatible with an Absolute Encoder (FQM1-MMP21/MMA21) 72 • The wiring for an encoder with a line-driver output (Am26LS31 or equiva- lent) is shown below. FQM1 Differential phase input mode A+ Black ...
Page 96
Wiring Module Connectors Connecting Pulse Outputs (FQM1-MMP21) FQM1-MMP21 5-V DC power supply for output CW pulse output CCW pulse output Example Connections with a Servo Driver are given below example. FQM1-MMP21 5-V DC power supply for outputs CW ...
Page 97
... Shield Either make a cable using the special connector (purchased separately), or connect to a terminal block using an OMRON special cable with a connector. (1) Do not apply voltages that exceed the maximum switching capacity of output circuits and the input voltage of I/O circuits. (2) Do not mistake positive and negative when wiring power supply, where there are positive and negative terminals ...
Page 98
... Wiring Servo Relay Units Applicable Connector-Terminal Block Conversion Units XW2Z-@@@K XW2Z-@@@J-A28 Recommended Wire The recommended size for cable wires is AWG24 to AWG26 (0.2 to Size 0.13 mm 3-4 Wiring Servo Relay Units XW2B-80J7-1A Servo Relay Units can be used to connect Motion Control Modules and Servo Drivers. ...
Page 99
... Servo Driver # 1 phase B switch 3. Servo Driver #2 connector 3. Servo Driver #1 connector Mounting hole (Can be mounted to DIN Track.) Servo Driver Servo Driver cable XW2Z-@@@J-B9 W-series Servo Driver XW2Z-@@@J-B10 SMARTSTEP XW2Z-@@@J-B13 W-series Servo Driver Signal TXD− TXD+ --- --- --- RXD− --- RXD+ --- FG ...
Page 100
Wiring Servo Relay Units Upper terminal block Lower terminal block Upper Terminal Block Pin Arrangement Lower Terminal Block Pin Arrangement Note ...
Page 101
Wiring Servo Relay Units 6. Signal Switches 7. Terminating Resistance Switch 8. Servo Driver Phase B Switches 78 TER_A R_B TER_Z X axis CUR TE SER_A SER_B SER_Z Y axis CNT1 CNT1 CNT1 DA2 Switch CNT1 SER_A Connects the Servo ...
Page 102
Wiring Servo Relay Units External Dimensions Signal switches 100 90 41.7 15.9 Wiring Screw-less Screw-less clamp terminal blocks use clamps to attach wires, and do not Clamp Terminal require screws. In addition to control signal wiring to Servo Drivers, clamp ...
Page 103
Wiring Servo Relay Units Recommended Screwdriver SZF1 0 Model Manufacturer Phoenix Contact Inc. Side Front 3.5 mm Section 3-4 ...
Page 104
... Peripheral Port Cable PA202 FLEXIBLE MOTION POWER CONTROLLER Power Supply Unit L1 AC100 -240V INPUT L2 Coordinator Module XW2Z-@@@K Connector- Terminal Block Conversion Unit Cable XW2D-40G6 or other Connecter-Terminal Block Conversion Unit RS-422A Cable (Modified by user) Programmable Terminal (PT) RS-232C connection or RS-422A/485 connection via CJ1W-CIF11 CM001 MMP21 ...
Page 105
Wiring Servo Relay Units Example Servo Relay When Servo Relay Units for the FQM1 are used, the I/O power supply is pro- Unit Wiring vided from terminals 20-0, 21-1, and 60-40. The only additional wiring required are the connections between ...
Page 106
... Connector-Terminal Block Conversion Unit. MIL Connector) Specifications Connects FQM1-MMP21 and Servo Relay Unit. Section 3-5 2. Servo Relay Unit Cable 3. Servo Relay Unit Cable 4. RS-422A Cable 5. Servo Driver Cables Model 1 m XW2Z-100K 1.5 m XW2Z-150K 2 m XW2Z-200K 3 m XW2Z-300K 5 m XW2Z-500K Model 0.5 m XW2Z-050J-A28 1 m XW2Z-100J-A28 83 ...
Page 107
... Cut off one end of the RS-422A cable listed above (4.) and attach crimp terminals. Section 3-5 Model 0.5 m XW2Z-050J-A30 1 m XW2Z-100J-A30 0.5 m XW2Z-050J-A31 1 m XW2Z-100J-A31 Model 1 m XW2Z-100J- XW2Z-200J-C1 Model 1 m XW2Z-100J- XW2Z-200J- XW2Z-100J-B10 2 m XW2Z-200J-B10 1 m XW2Z-100J-B13 2 m XW2Z-200J-B13 Pin No. Signal 1 TXD− 2 TXD+ 3 --- 4 --- 5 --- 6 RXD− 7 --- 8 RXD+ 9 --- Case FG ...
Page 108
... RS-422A Connecting Cable No. Signal 2 SDB+ 1 SDA− 8 RDB+ 6 RDA− Suspended ducts Section 3-6 XW2D-40G6 Connector- Terminal Block Conversion Unit XW2Z-100J-C1 or XW2Z-200J-C1 RS-422A Cable Connector-Terminal Block Conversion Unit terminal number A18 A17 B18 B17 1 = I/O cables 2 = Power cables 2 1 Conduits In-floor ducts 2 85 ...
Page 109
Wiring Precautions Inductive Loads When an inductive load is connected to I/O, connect a surge suppressor or diode in parallel with the load as shown below. Note Use surge suppressors and diodes with the following specifications. External Wiring Observe the ...
Page 110
Wiring Precautions 3-6-2 Connecting I/O Devices Input Devices Use the following information for reference when selecting or connecting input devices. DC Inputs The following types of DC input devices can be connected. Contact output Two-wire DC output NPN open-collector output ...
Page 111
Wiring Precautions Current regulator Precautions when When using a two-wire sensor with a 24-V DC input device, check that the fol- Connecting a Two-wire DC lowing conditions have been met. Failure to meet these conditions may result Sensor in operating ...
Page 112
... Programming Example In this example, the sensor’s power supply voltage is used as the input to CIO 0000.00 and a 100-ms timer delay (the time required for an OMRON Proximity Sensor to stabilize) is created in the program. After the Completion Flag for the timer turns ON, the sensor input on CIO 0000.01 will cause output bit CIO 0001 ...
Page 113
Wiring Precautions Output Surge Current When connecting a transistor or triac output to an output device having a high surge current (such as an incandescent lamp), steps must be taken to avoid damage to the transistor or triac. Use either ...
Page 114
This section describes the operation of the FQM1. 4-1 Coordinator Module . . . . . . . . . . . . . . . . . . . . . . . . . . . . . ...
Page 115
Coordinator Module 4-1 Coordinator Module The FQM1 Coordinator Module and each Motion Control Module have sepa- rate ladder programming. Each Module independently processes the ladder programming, I/O, and peripheral servicing to achieve high-speed I/O response somewhat like a system of ...
Page 116
Coordinator Module System Setup The System Setup contains software switches used to make initial settings and other settings. As shown in Appendix C System Setup, Auxiliary Area Allocations, and Built-in I/O Allocations, addresses (words and bits) are allo- cated for ...
Page 117
Coordinator Module 4-1-3 I/O Refreshing and Peripheral Servicing I/O Refreshing I/O refreshing updates general-purpose I/O status. All I/O is refreshed in the same cycle (i.e., time slicing is not used). I/O refreshing is always performed after program execution. Cyclic Refreshing ...
Page 118
Motion Control Modules 4-2 Motion Control Modules 4-2-1 Outline Motion Control Modules each have independent ladder programming, which perform processing independently from other Modules. The following diagram shows the internal structure of Motion Control Modules. Note 4-2-2 Description of Each ...
Page 119
Motion Control Modules Broadly speaking, the user program consists of a cyclic task and interrupt tasks, which are executed for interrupts. The cyclic task is executed every cycle. The user program is stored in RAM and flash memory. Data is ...
Page 120
Motion Control Modules Basic inputs (12) Basic outputs (8) Pulse inputs (2) or analog input (1) Pulse or analog outputs (2) Sync Mode Operation In Sync Mode, the Motion Control Module's cyclic scan is synced with the Coordinator Module's cyclic ...
Page 121
Motion Control Modules Coordinator Module Motion Control Module Initialization at At Internal Module initialization (determining the operating mode, initializing user power ON memory, clearing specified memory areas, checking for memory corruption, reading the System Setup, etc.) is performed and the ...
Page 122
Operating Modes 4-3 Operating Modes 4-3-1 Operating Modes Coordinator and Motion Control Modules have three operating modes that control the user program. PROGRAM Programs are not executed and preparations, such as initializing the System Setup and other settings, transferring programs, ...
Page 123
Power OFF Operation 4-3-3 Operating Mode Changes and I/O Memory RUN or MONITOR to PROGRAM PROGRAM to RUN or MONITOR RUN to MONITOR or MONITOR to RUN Note 4-4 Power OFF Operation 4-4-1 Power OFF Operation The following processing is ...
Page 124
Power OFF Operation Power supply voltage Power supply voltage Power supply voltage Note The above timing chart shows an example when the User-set Power OFF Detection Time is set to 0 ms. The following timing chart shows the Coordinator Module ...
Page 125
Power OFF Operation Description of Operation Power OFF will be detected if the 100 to 240 V AC power supply stays below 85% of the minimum rated voltage for the Fixed Power OFF Detection Time (variable between ...
Page 126
This section describes the functions common to both the Coordinator Module and Motion Control Modules and the methods to transfer data between the Coordinator Module and Motion Control Modules. 5-1 Synchronous Operation between Modules . . . . . . ...
Page 127
Synchronous Operation between Modules 5-1 Synchronous Operation between Modules Sync and ASync Modes Sync Mode The Coordinator Module and Motion Control Modules are normally set to operate using the same cycle time, i.e., synchronously. Synchronous opera- tion is the default ...
Page 128
Data Exchange between Modules 5-2 Data Exchange between Modules The three methods for data exchange between Coordinator and Motion Con- trol Modules are outlined in the following table. These methods can be used simultaneously. Method Outline 1. Cyclic refresh Exchanges ...
Page 129
Cyclic Refresh 5-3 Cyclic Refresh 5-3-1 Outline Status information, general-purpose I/O, and other information for each Motion Control Module in the Cyclic Refresh Area of the Coordinator Module are refreshed every Coordinator Module cycle (asynchronous to the Motion Control Module ...
Page 130
Cyclic Refresh 5-3-3 Cyclic Refresh Area Details Coordinator Module CIO 0100 to CIO 0109 in each Motion Control Module is allocated to ten Cyclic Refresh Area words between CIO 0100 to CIO 0139 in the Coordinator Module according to the ...
Page 131
Cyclic Refresh Word Bits address CIO 0105 Output Refresh Area (This MM to CM) 08 Data from this area is allo- 09 cated to the Coordinator Mod- ule's CM Input Refresh Area (MM to CM). 10 ...
Page 132
Synchronous Data Refresh 5-4 Synchronous Data Refresh 5-4-1 Outline If Sync is set under Synchronization between Modules in the System Setup, each Module will broadcast the specified data (2 types data, 4 words max.) to the Synchronous Data Link Bit ...
Page 133
Synchronous Data Refresh Synchronous Data Normal (via Ladder) Counter 1 values Counter 2 values Pulse output 1 Pulse output 2 Analog input Analog output 1 Analog output 2 Inner I/O input (Built-in input) Note 5-4-3 Synchronous Data Link Bit Area ...
Page 134
Synchronous Data Refresh Synchronous Data Word Link Bit Areas in address Coordinator and (See note Motion Control 1.) Modules Sent from Motion CIO 0216 Control Module #4 CIO 0217 CIO 0218 CIO 0219 Note 5-4-4 Settings System Setup (Coordinator Module) ...
Page 135
DM Data Transfer System Setup (Motion Control Modules) Selecting Synchronous Data Tab page Function Module Select Syn- Upper 2 words Settings chronous (+0 and +1) Data Lower 2 words (+2 and +3) Note Prohibit System Interruption of the Sync Mode ...
Page 136
DM Data Transfer 5-5-2 Settings Details The settings for using the DM data transfer function are made in the Auxiliary Area. Name DM Write Request Bit (Coordinator A530.00 Module to Motion Control Module) DM Read Request Bit (Motion A530.01 Control ...
Page 137
Cycle Time Settings Step 2: Turn ON Request Bit Programming Example Note 5-6 Cycle Time Settings 5-6-1 Constant Cycle Time Function 114 • Transferring DM Data from the Coordinator Module to a Motion Control Module: Turn ON the DM Write ...
Page 138
Cycle Time Settings System Setup Constant Cycle Time Exceeded Flag Constant Cycle Time Exceeded Error Clear Bit Constant Cycle Time When in Sync Mode with a Sync Cycle Time set for the Coordinator Module Function in Sync cycle time (default), ...
Page 139
Cycle Time Settings Coordinator Module Waiting for I/O refresh to become constant Motion Processing Control Module Constant I/O refresh timing Note When the constant cycle time function is enabled for the Motion Control Mod- ule in ASync Mode, the Motion ...
Page 140
Cycle Time Settings 5-6-4 Clearing Constant Cycle Time Exceeded Errors Auxiliary Area Bits When using the constant cycle time function, normally the cycle time will no longer stay constant (i.e., will vary depending on the real cycle time) if the ...
Page 141
Operation Settings at Startup and Maintenance Functions 5-7 Operation Settings at Startup and Maintenance Functions This section describes the following operation settings at startup and mainte- nance functions. 5-7-1 Specifying the Startup Mode The operating mode when the power is ...
Page 142
Operation Settings at Startup and Maintenance Functions Password Protection 1,2,3... 5-7-3 Flash Memory Automatic Backup to Flash Memory Note 1. Register a password either online or offline. a. Select the Module in the Device Type drop-down menu and select Properties ...
Page 143
Diagnostic Functions in the PLC properties and Window/PLC Memory Backup Status must be selected from the View Menu. For normal transfer operations (PLC/Transfer), the backup status will be displayed in the transfer window after the transfer status for the program ...
Page 144
Diagnostic Functions Note 5-8-2 Failure Alarm Functions 1,2,3... Operation of FAL(006) Order of Error code occurrence Error Log Area 4102 1 A100 A101 A102 C101 A103 2 A104 A105 A106 A107 A108 A109 80C0 20 A195 A196 A197 A198 A199 ...
Page 145
Diagnostic Functions Operation of FALS(007) 122 Errors generated by FAL(006) can be cleared by executing FAL(006) with FAL number 00 or performing the error read/clear operation from the CX-Program- mer. B When input condition B goes ON, an error with ...
Page 146
This section describes the serial communications functions, which are supported only by the Coordinator Module. 6-1 Serial Communications . . . . . . . . . . . . . . . . . . . . . . ...
Page 147
... Serial Communications 6-1 Serial Communications Protocol Connections Host Link Host computer or OMRON PT (Programmable Terminal) OMRON PT (Programmable Host computer Terminal) Monitor and or set parameters No-protocol General-purpose external device 1:N NT Link OMRON PT (The 1:N NT (Programmable Terminal) Link commu- nications are used even for 1:1 con- nections ...
Page 148
... Serial Communications Protocol Connections Peripheral Programming Device Bus (CX-Programmer) Serial Gate- OMRON PT way (Programmable Host computer Terminal) or Servo Drivers No-protocol FQM1 Servo Drivers Note The CJ1W-CIF11 is not insulated and the total transmission distance is 50 meters max. If the total transmission distance is greater than 50 meters, use the insulated NT-AL001 and do not use the CJ1W-CIF11 ...
Page 149
Serial Communications 6-1-1 Host Link Communications The following table shows the Host Link communication functions available in FQM1. Select the method that best suits your application. Command Command type flow Host computer C-mode (Host Link) to FQM1 commands Host Link ...
Page 150
Serial Communications Host Link Commands Type Header code Reading I/O RR CIO AREA READ memory RC PV READ RG T/C STATUS READ RD DM AREA READ RJ AR AREA READ Writing I/O WR CIO AREA WRITE memory WC PV WRITE ...
Page 151
Serial Communications Type Header code Program area RP PROGRAM READ access com- mands WP PROGRAM WRITE Compound QQMR COMPOUND COMMAND reading of I/O QQIR COMPOUND READ memory Processing Host XZ ABORT (command only) Link communi- cations ** INITIALIZE (command only) ...
Page 152
Serial Communications Type Command code Forced Status 23 01 FORCED SET/RESET 23 02 FORCED SET/RESET CANCEL Cancels the forced status of all force-set and force-reset 6-1-2 No-protocol Communications (RS-232C Port) No-protocol Mode is used to send and receive data using ...
Page 153
Serial Communications Procedure Data can be placed between a start code and end code for transmission by Message Frame TXD(236) and frames with that same format can be received by RXD(235). Formats When transmitting with TXD(236), just the data from ...
Page 154
Serial Communications TXD(236) instruction Refer to the Instructions Reference Manual (Cat. No. O011) for more details on the TXD(236) and RXD(235) instructions. System Setup RS-232C Settings (Host Link Port Settings) Note The settings are made using CX-Programmer Ver. 5.0@ menus. ...
Page 155
Serial Communications 6-1-4 Serial PLC Links Overview The FQM1 can be connected to a Serial PLC Link by linking to a Serial PLC Master. (It cannot be connected by the Complete Link Method.) Program-free data exchange can be achieved between ...
Page 156
Serial Communications Direction of Data Transfer For example, if the number of link words is set to 10, the CJ1M CPU Unit (master) will broadcast CIO 3100 to CIO 3109 from its I/O memory and to CIO 0080 to CIO ...
Page 157
... Drivers that are connected to the FQM1 Coordinator Module's RS-422A port. This function can be executed by setting the FQM1 Coordinator Module’s RS- 422A serial communications mode to Serial Gateway. RS-422A-compatible OMRON W-series and OMRON SMARTSTEP Servo Drivers. Servo Drivers System Configuration Example: Accessing a W-series or SMARTSTEP Servo Driver from Smart ...
Page 158
Serial Communications Note When the Serial Gateway function is used, the FQM1 receives FINS com- mands (encapsulated W-series or SMARTSTEP commands) via the RS-422A port from NT-series PTs or personal computers and converts them to W- series or SMARTSTEP Servo ...
Page 159
Serial Communications 6-1-6 No-protocol Communications (RS-422A Port) RS-232C port RS-422A Settings Note The settings are made using CX-Programmer Ver. 5.0@ menus. 136 Coordinator Module FQM1 RS-422A port No-protocol No-protocol RS-232C General- purpose external device Item Settings Mode No-protocol Delay 0 ...
Page 160
This section describes the various functions supported by the Motion Control Module. 7-1 Overview . . . . . . . . . . . . . . . . . . . . . . . . . . ...
Page 161
... Timing Chart of the Functions for Servo Drivers Compatible with Absolute Encoders . . . . . . . . . . . . . . . . . . . . . . . . . . . . . . . . . . 7-7-12 Sample Programs (Connecting an OMRON W-series Servo Driver) 7-8 Virtual Pulse Output Function . . . . . . . . . . . . . . . . . . . . . . . . . . . . . . . . . . . . . ...
Page 162
Overview 7-1 Overview The FQM1 Modules have the following functions. Main function (Applicable Modules) Basic interrupt functions Input Interrupts (4 points) (Input Interrupt Mode or Counter Mode) (FQM1-MMP21/MMA21) Interval Timer Interrupt (1 point) Setting range: 0.5 to 99,990 ms Unit: ...
Page 163
Interrupt Functions 7-2 Interrupt Functions 7-2-1 Overview The Motion Control Modules support the following interrupts. Executing Interrupt The programming routines that are executed for all of the following interrupts Programs in the are programmed as interrupt tasks. FQM1 Input Interrupts ...
Page 164
Interrupt Functions Method 1: Disabling all interrupts in the main program MSKS 0100 0000 0000 @PLS2 0001 0000 D00010 MSKS 0200 0000 0000 Note 7-2-3 Disabling and Enabling All Interrupts Disabling All Interrupts Note Enabling All Interrupts Note This situation ...
Page 165
Input Interrupts Clearing Recorded Interrupts 7-3 Input Interrupts 7-3-1 Applicable Models 7-3-2 Overview of the Input Interrupt Function Note 7-3-3 Interrupt Modes 7-3-4 Input Interrupt Specifications Input Interrupt Mode 142 The EI(694) instruction does not enable all interrupts ...
Page 166
Input Interrupts Counter Mode 7-3-5 Using Input Interrupts Input Interrupt Mode Procedure 1,2,3... 1. Determine which input interrupt number will be used. 2. Wire the input. 3. Make the necessary System Setup settings. 4. Create the necessary ladder programming. Interrupt ...
Page 167
Input Interrupts Counter Mode Procedure 1,2,3... Interrupt 0 CIO 0000.00 input 1 CIO 0000.01 2 CIO 0000.02 3 CIO 0000.03 144 1. Determine which input interrupt number will be used. 2. Determine the initial SV for the decrementing counter. 3. ...
Page 168
Input Interrupts 7-3-6 Application Example This example shows input interrupt 0 and input interrupt 1 used in interrupt input mode and counter mode, respectively. Before executing the program, verify that the following System Setup settings have been made: input 0 ...
Page 169
Interval Timer Interrupts The following timing chart shows the operation of the program exe- cuted. CIO 0000.00 Interrupt task 000 CIO 0000.01 Interrupt task 001 CIO 0002.00 Note 7-4 Interval Timer Interrupts 7-4-1 Applicable Models 7-4-2 Overview ...
Page 170
Interval Timer Interrupts 7-4-5 Application Example CIO 0002.00 Interrupt task Interval timer Ladder Program STIM INTERVAL TIMER • Start timer. One-shot mode Scheduled interrupt mode • Read elapsed time. In this example, the interval timer is used to generate an ...
Page 171
Pulse Inputs 7-5 Pulse Inputs 7-5-1 Applicable Models Model FQM1-MMP21 FQM1-MMA21 7-5-2 Outline The FQM1-MMP21 and FQM1-MMA21 Motion Control Modules can receive pulse inputs. The following table shows the processes that can be performed by combining the pulse input function ...
Page 172
Pulse Inputs Item Counter values High-speed counter PV storage locations Latch inputs Control Target value comparison method Range comparison Counter reset Mea- Counter movements sure- (mode 1) ment mode Counter frequency (mode 2) Measurement storage location for above measurements • ...
Page 173
Pulse Inputs 7-5-4 Pulse Input Specifications Item Number of 2 inputs pulse inputs Note High-speed counter 1 can be an RS-422A line-driver input or an input with a voltage of 24 VDC. High-speed counter 2 can be an RS-422A line-driver ...
Page 174
Pulse Inputs Item Minimum response pulse At 50 kHz Encoder Inputs A and B Waveform of Encoder Inputs A and B Signal rise and fall must be 3 µs max. 50-kHz pulse with 50% duty ratio ON 50% OFF 3 ...
Page 175
Pulse Inputs 7-5-5 Latch Input Specifications 7-5-6 Applicable Instructions Instruction Control (@)CTBL(882) Range comparison Target value comparison table regis- tration and starting comparison Target value comparison table regis- tration (@)INI(880) Starting comparison Stopping comparison Changing PV Changing circular value (@)PRV(881) ...
Page 176
Pulse Inputs 7-5-8 Pulse Input Function Description The pulse input function uses the high-speed counters. The pulse input func- tion can be used to monitor changes (movement) in the high-speed counter PV (mode 1) or changes in the high-speed counter ...
Page 177
Pulse Inputs Increment/Decrement Pulse Inputs Encoder Input A (UP input) Encoder Input B (DOWN input Increment Counter Operation The following two counter operations are available for high-speed counters 1 (Numeric Ranges) and 2, with the specified counting ...
Page 178
Pulse Inputs ■ Phase-Z Signal (Reset Input) and Software Reset The PV of the high-speed counter is reset on the first rising edge of the phase-Z signal after the corresponding High-speed Counter Reset Bit (see below) turns ON. Reset Bit ...
Page 179
Pulse Inputs Counter PV Target value 3 Target value 2 Target value 4 Target value 1 Target value 5 0 Target values 1 2 for comparison ■ Range Comparison Method comparison ranges (lower and upper limit values) ...
Page 180
Pulse Inputs Monitoring High-speed This function monitors the change in a high-speed counter’s PV (travel dis- Counter Movement tance) regularly at the preset sampling period. The sampling period can be (Mode 1) set between 1 and 9,999 ms. If the ...
Page 181
Pulse Inputs High-speed Counter Movement (Mode 1) Specifications Note Monitoring a High-speed Mode 2 is supported by high-speed counter 1 only. Counter’s Frequency This function monitors the input pulse’s frequency from the high-speed (Mode 2) counter movement value. The frequency ...
Page 182
Pulse Inputs Frequency Measurement (Mode 2) Specifications Latching a High-speed The present counter value can be latched at the rising edge of the latch signal Counter’s PV input and stored as the latch register value. Each time the counter value ...
Page 183
Pulse Inputs 7-5-9 Pulse Input Function Procedures High-speed Counter Procedure 1,2,3... 1. Determine the Input Mode, reset method, and Numeric Range. 2. Wire the input. 3. Make the necessary System Setup settings the count check is being used, ...
Page 184
Pulse Inputs A Pulse input 1 B Input Mode Reset Method Z Phase differential Phase-Z /software reset Pulse + Direction Software reset Increment/Decrement A Pulse input System Setup Input Target-value comparison interrupt A Ladder Program CTBL INI ...
Page 185
Pulse Inputs Procedure 1,2,3... 1. Set Counter movements (mode 1) in the System Settings (Pulse Input, 2. Turn ON the Measurement Start Bit (A610.02 or A611.02). 3. Monitor the high-speed counter movement value in A604 and A605 Mode 2 Procedure ...
Page 186
Pulse Inputs High-speed Counter PV Target value 3 10000 Target value 2 7500 Target value 1 2500 Interrupt tasks Task 10 starts Example When the PV reaches 2,500 hex, interrupt task 10 is started. When the PV reaches 7,500 hex, ...
Page 187
Pulse Inputs P_On A610.00 (Always ON) Start high-speed counter. A610.01 Reset Bit 0002.00 @CTBL #0001 #0000 D00000 END Control program 1 END Control program 2 END Control program 3 END Example 2: In this example, pulse input 1 operates a ...
Page 188
Pulse Inputs High-speed Counter PV 10000 Range 3 7500 Range 2 2500 Range 1 0 A612: 0001 hex 0002 hex 0004 hex 0008 hex P_On A610.00 Starts high-speed counter 1. (Always ON) Start high-speed counter. A610.01 Turns ON the High-speed ...
Page 189
Pulse Inputs Example 3: In this example, pulse input 1 operates a high-speed counter, the high-speed Latching High-speed counter PV is latched, and the captured high-speed counter PV is read. When the Latch Input 1 Enable Bit is ON and ...
Page 190
Pulse Outputs 7-6 Pulse Outputs 7-6-1 Applicable Models FQM1-MMP21 7-6-2 Outline The FQM1-MMP21 Motion Control Module provides 2 pulse outputs. The pulse outputs can be used for the following functions. Note Set the pulse output operation mode for each output ...
Page 191
Pulse Outputs 7-6-3 Specifications Item Acceleration/ decelera- None tion Trapezoid None Instructions for inde- PULS(886) + pendent-mode posi- SPED(885) tioning Instructions for contin- SPED(885) uous-mode speed con- trol Output frequencies Constant specified for SPED(885 MHz Word ...
Page 192
Pulse Outputs Item Number of output 1) Relative pulse output: pulses 2) Absolute linear pulse output: 3) Absolute circular pulse output: 4) Electronic cam control (linear) (output with absolute position specification): 5) Electronic cam control (circular) (output with absolute position ...
Page 193
Pulse Outputs 7-6-5 Applicable Instructions The following seven instructions can be used to control pulse outputs. The relationship between the instruction and the types of pulse output that is pos- sible is also listed in the following table. Instruction Control ...
Page 194
Pulse Outputs 7-6-6 Pulse Output Function Details Overview Note Pulses are output in independent mode or continuous mode. In independent mode, the number of output pulses is specified in advance. In continuous mode, the number of output pulses is not ...
Page 195
Pulse Outputs Pulse output operation mode (Only in Independent Mode) (1) Positions to a relative position from the present position. Relative pulse output The number of output pulses (actual output amount) in the specified direction is the target number of ...
Page 196
Pulse Outputs Pulse Output The following table shows the operations that can be performed with the pulse Operations output function. Mode Frequency changes Continu- Frequency ous mode Target (Speed frequency control) Present frequency SPED executed. Frequency Target frequency Acceleration rate ...
Page 197
Pulse Outputs Mode Frequency changes Indepen- Frequency dent Specified no. of pulses (Specified with PULS) mode Target (Position- frequency ing) SPED executed. Stops after specified no. of pulses are output. Frequency Specified no. of pulses (Specified with PULS) Target frequency ...
Page 198
Pulse Outputs Mode Frequency changes Stop Frequency Present frequency INI executed. Frequency Present frequency SPED executed. Frequency Present frequency Target frequency = 0 ACC executed. Note With ACC(888) and PLS2(887), the acceleration/deceleration rate’s speed-change cycle can be set to 2ms ...
Page 199
Pulse Outputs Formula: Actual frequency = Clock frequency ÷ INT (clock frequency/target frequency) The difference between the target frequency and the actual frequency increases at higher frequencies. The following tables shows examples for a clock frequency of 20 MHz. 7-6-7 ...
Page 200
Pulse Outputs Note One-shot Pulse Output Specifications Turned ON by STIM instruction execution. ON One-shot pulse output OFF Setting units: Select 0.01 ms, 0.1 ms ms. Setting range: 0001 to 270F Hex (1 to 9,999) Set the pulse ...