ADM1024ARUZ ON Semiconductor, ADM1024ARUZ Datasheet - Page 14
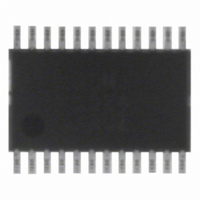
ADM1024ARUZ
Manufacturer Part Number
ADM1024ARUZ
Description
IC MONITOR SYS TEMP/VOLT 24TSSOP
Manufacturer
ON Semiconductor
Datasheet
1.ADM1024ARUZ.pdf
(29 pages)
Specifications of ADM1024ARUZ
Applications
PC's, PDA's
Interface
Serial
Voltage - Supply
2.8 V ~ 5.5 V
Package / Case
24-TSSOP
Mounting Type
Surface Mount
Temperature Sensor Function
Temp Sensor
Output Type
Digital
Package Type
TSSOP
Operating Temperature (min)
0C
Operating Temperature (max)
100C
Operating Temperature Classification
Commercial
Operating Supply Voltage (typ)
3.3V
Operating Supply Voltage (max)
5.5V
Full Temp Accuracy
+/- 2 C , +/- 3 C
Digital Output - Bus Interface
SMBus
Digital Output - Number Of Bits
10 bit
Supply Voltage (max)
12 V
Supply Voltage (min)
2.5 V
Maximum Operating Temperature
+ 100 C
Minimum Operating Temperature
0 C
Supply Current
1.4 mA
Lead Free Status / RoHS Status
Lead free / RoHS Compliant
Available stocks
Company
Part Number
Manufacturer
Quantity
Price
Part Number:
ADM1024ARUZ
Manufacturer:
ADI/亚德诺
Quantity:
20 000
current sources, excessive cable and/or filter capacitance
can affect the measurement. When using long cables, the
filter capacitor may be reduced or removed.
resistance introduces about 0.5°C error.
Limit Values
appropriate limit registers. In the case of voltage
measurements, high and low limits can be stored so that an
interrupt request will be generated if the measured value
goes above or below acceptable values. In the case of
temperature, a Hot Temperature or High Limit can be
programmed, and a Hot Temperature Hysteresis or Low
Limit, which will usually be some degrees lower. This can
be useful as it allows the system to be shut down when the
hot limit is exceeded, and restarted automatically when it has
cooled down to a safe temperature.
Because the measurement technique uses switched
Cable resistance can also introduce errors. A 1 W series
Limit values for analog measurements are stored in the
3. Use wide tracks to minimize inductance and
4. Try to minimize the number of copper/solder joints,
5. Place 0.1 mF bypass and 2200 pF input filter
6. If the distance to the remote sensor is more than
7. For really long distances (up to 100 feet) use
GND
GND
reduce noise pickup. A 10 mil track minimum
width and spacing is recommended.
which can cause thermocouple effects. Where
copper/solder joints are used, make sure that they
are in both the D+ and D– path and at the same
temperature. Thermocouple effects should not be a
major problem as 1°C corresponds to about 240 mV,
and thermocouple voltages are about 3 mV/°C of
temperature difference. Unless there are two
thermocouples with a big temperature differential
between them, thermocouple voltages should be
much less than 200 mV.
capacitors close to the ADM1024.
8 inches, the use of twisted pair cable is
recommended. This will work up to about 6 feet to
12 feet.
shielded twisted pair such as Belden #8451
microphone cable. Connect the twisted pair to D+
and D– and the shield to GND close to the
ADM1024. Leave the remote end of the shield
unconnected to avoid ground loops.
Figure 18. Arrangement of Signal Tracks
D+
D–
10MIL
10MIL
10MIL
10MIL
10MIL
10MIL
10MIL
10MIL
10MIL
10MIL
10MIL
http://onsemi.com
14
Monitoring Cycle Time
Start Bit (Bit 0), and a 0 to the INT_Clear Bit (Bit 3) of the
Configuration Register. INT_Enable (Bit 1) should be set to
1 to enable the INT output. The ADC measures each analog
input in turn; as each measurement is completed, the result
is automatically stored in the appropriate value register. This
“round robin” monitoring cycle continues until it is disabled
by writing a 0 to Bit 0 of the Configuration Register.
manner, the time taken to monitor all the analog inputs will
normally not be of interest, as the most recently measured
value of any input can be read out at any time.
important, it can be calculated as follows:
m
internal V
t
6.044 ms.
n
inputs.
t
33.24 ms.
response in the event of any input going out of limits, unlike
other monitoring chips that employ slower ADCs.
Fan Monitoring Cycle Time
speed inputs begins at the same time as monitoring of the
analog inputs. However, the two monitoring cycles are not
synchronized in any way. The monitoring cycle time for the
fan inputs is dependent on fan speed and is much slower than
for the analog inputs. For more details, see the Fan Speed
Measurement section.
Input Safety
external attenuators are normally not required. However,
since the power supply voltages will appear directly at the
pins, it is advisable to add small external resistors in series
with the supply traces to the chip to prevent damaging the
traces or power supplies should an accidental short such as
a probe connect two power supplies together.
they will affect the accuracy of the analog measurement if
their value is too high. The analog input channels are
calibrated assuming an external series resistor of 500 W, and
the accuracy will remain within specification for any value
from 0 kW to 1 kW, so a standard 510 W resistor is suitable.
+12 V, a total of 24 V difference. With the series resistors, this
would draw a maximum current of approximately 24 mA.
1 ⎯
2 ⎯
⎯
The monitoring cycle begins when a 1 is written to the
As the ADC will normally be left to free−run in this
For applications where the monitoring cycle time is
This rapid sampling of the analog inputs ensures a quick
When a monitoring cycle is started, monitoring of the fan
Scaling of the analog inputs is performed on−chip, so
As the resistors will form part of the input attenuators,
The worst such accident would be connecting −2.0 V to
⎯
where:
the number of inputs configured as external temperature
the time taken for an analog input conversion, nominally
the number of inputs configured as analog inputs, plus the
the time taken for a temperature conversion, nominally
CC
measurement and internal temperature sensor.
m
t
1
) n
t
2
(eq. 6)