LMD18201T/NOPB National Semiconductor, LMD18201T/NOPB Datasheet - Page 7
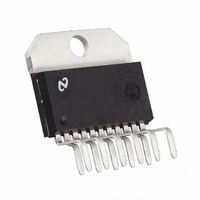
LMD18201T/NOPB
Manufacturer Part Number
LMD18201T/NOPB
Description
IC H BRIDGE 3A 55V TO220-11
Manufacturer
National Semiconductor
Specifications of LMD18201T/NOPB
Applications
DC Motor Driver, Stepper Motor Driver, H Bridge
Number Of Outputs
1
Current - Output
3A
Voltage - Supply
12 V ~ 55 V
Operating Temperature
-40°C ~ 125°C
Mounting Type
Through Hole
Package / Case
TO-220-11 (Bent and Staggered Leads)
Lead Free Status / RoHS Status
Lead free / RoHS Compliant
Voltage - Load
-
Lead Free Status / Rohs Status
RoHS Compliant part
Electrostatic Device
Other names
*LMD18201T
*LMD18201T/NOPB
LMD18201T
*LMD18201T/NOPB
LMD18201T
SIGNAL TRANSITION REQUIREMENTS
To ensure proper internal logic performance, it is good prac-
tice to avoid aligning the falling and rising edges of input
signals. A delay of at least 1 µsec should be incorporated be-
tween transitions of the Direction, Brake, and/or PWM input
signals. A conservative approach is be sure there is at least
500ns delay between the end of the first transition and the
beginning of the second transition. See
USING THE THERMAL WARNING FLAG
The THERMAL FLAG output (pin 9) is an open collector tran-
sistor. This permits a wired OR connection of thermal warning
flag outputs from multiple LMD18201's, and allows the user
to set the logic high level of the output signal swing to match
system requirements. This output typically drives the interrupt
input of a system controller. The interrupt service routine
would then be designed to take appropriate steps, such as
reducing load currents or initiating an orderly system shut-
down. The maximum voltage compliance on the flag pin is
12V.
SUPPLY BYPASSING
During switching transitions the levels of fast current changes
experienced may cause troublesome voltage transients
across system stray inductances.
It is normally necessary to bypass the supply rail with a high
quality capacitor(s) connected as close as possible to the
V
1 μF high-frequency ceramic capacitor is recommended.
Care should be taken to limit the transients on the supply pin
below the Absolute Maximum Rating of the device. When op-
erating the chip at supply voltages above 40V a voltage
suppressor (transorb) such as P6KE62A is recommended
from supply to ground. Typically the ceramic capacitor can be
eliminated in the presence of the voltage suppressor. Note
that when driving high load currents a greater amount of sup-
ply bypass capacitance (in general at least 100 μF per Amp
of load current) is required to absorb the recirculating currents
of the inductive loads.
S
Power Supply (Pin 6) and POWER GROUND (Pin 7). A
FIGURE 4. Transitions in Brake, Direction, or PWM Must be Separated by At Least 1 μsec
Figure
4.
7
CURRENT LIMITING
Current limiting protection circuitry has been incorporated into
the design of the LMD18201. With any power device it is im-
portant to consider the effects of the substantial surge cur-
rents through the device that may occur as a result of shorted
loads. The protection circuitry monitors the current through
the upper transistors and shuts off the power device as quickly
as possible in the event of an overload condition (the thresh-
old is set to approximately 10A). In a typical motor driving
application the most common overload faults are caused by
shorted motor windings and locked rotors. Under these con-
ditions the inductance of the motor (as well as any series
inductance in the V
nitude of a current surge to a safe level for the LMD18201.
Once the device is shut down, the control circuitry will peri-
odically try to turn the power device back on. This feature
allows the immediate return to normal operation once the fault
condition has been removed. While the fault remains howev-
er, the device will cycle in and out of thermal shutdown. This
can create voltage transients on the V
therefore proper supply bypassing techniques are required.
The most severe condition for any power device is a direct,
hard-wired (“screwdriver”) long term short from an output to
ground. This condition can generate a surge of current
through the power device on the order of 15 Amps and require
the die and package to dissipate up to 500W of power for the
short time required for the protection circuitry to shut off the
power device. This energy can be destructive, particularly at
higher operating voltages (>30V) so some precautions are in
order. Proper heat sink design is essential and it is normally
necessary to heat sink the V
inch of copper on the PC board.
INTERNAL CHARGE PUMP AND USE OF
BOOTSTRAP CAPACITORS
To turn on the high-side (sourcing) DMOS power devices, the
gate of each device must be driven approximately 8V more
positive than the supply voltage. To achieve this an internal
charge pump is used to provide the gate drive voltage. As
CC
supply line) serves to reduce the mag-
CC
supply pin (pin 6) with 1 square
1079324
CC
supply line and
www.national.com