AS5040 PB austriamicrosystems, AS5040 PB Datasheet
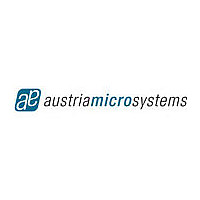
AS5040 PB
Specifications of AS5040 PB
AS5140H PB
AS5145 PB
Related parts for AS5040 PB
AS5040 PB Summary of contents
Page 1
... Ideal for applications in harsh environments due to contactless position sensing Tolerant to magnet misalignment and airgap variations No temperature compensation necessary No calibration required www.austriamicrosystems.com 2 Key Features Contactless high resolution rotational position encoding over a full turn of 360 degrees Two digital 10bit absolute outputs: - Serial interface and ...
Page 2
... Configures pin 3 to deliver up to 512 pulses (up to 1024 state changes) per revolution equivalent to the LSB (least significant bit) of the absolute position value. Pin 4 provides the information of the rotational direction. Both modes (mode 1.x and mode 2.x) provide an index signal (1 pulse/revolution) with an adjustable width of one LSB or three LSB’s. www.austriamicrosystems.com ...
Page 3
... A logic high at CSn puts the data output pin (DO) to tri-state and terminates serial data transfer. This pin is also used for alignment mode (page 21) and programming mode (page 16). www.austriamicrosystems.com Magnet Field Magnitude INCrease; active low, indicates a distance reduction between the magnet and the device surface. ...
Page 4
... VDD5V = 3.0-3.6V (3V operation) VDD5V = 4.5-5.5V (5V operation) amb unless otherwise noted) Parameter High level input voltage Low level input voltage Schmitt Trigger hysteresis Input leakage current Pull-up low level input current www.austriamicrosystems.com Symbol Min Max VDD5V -0.3 7 VDD3V3 -0 ...
Page 5
... VDD5V = 3.0-3.6V (3V operation) VDD5V = 4.5-5.5V (5V operation) unless otherwise amb noted) Two-pole cylindrical diametrically magnetised source: Parameter Symbol Diameter d mag Thickness t mag Magnetic input field B pk amplitude www.austriamicrosystems.com Symbol Min V 0.7 * VDD5V IH V See “programming conditions” PROG V 0.3 * VDD5V Symbol Min ...
Page 6
... Integral non-linearity (optimum) Integral non-linearity (optimum) Integral non-linearity Differential non-linearity Transition noise Hysteresis Power-on reset thresholds On voltage; 300mV typ. hysteresis Off voltage; 300mV typ. hysteresis Power-up time System propagation delay absolute output www.austriamicrosystems.com Min Typ Max Unit ± 500 Hz 0.25 mm 0.485 ±0.23 ...
Page 7
... First data shifted to output t CLK FE register Start of data output T CLK / 2 Data output valid t DO valid Data output tristate t DO tristate Pulse width of CSn t CSn www.austriamicrosystems.com Min Typ Max 192 9.90 10.42 10.94 f 9.38 10.42 11.46 S CLK 1 Actual curve TN Ideal curve ...
Page 8
... PROG CLK pulse width Hold time of Vprog after t programming Programming voltage Programming voltage off level Programming current Analog read CLK Programmed zener voltage (log.1) Unprogrammed zener voltage V (log. 0) www.austriamicrosystems.com Min Typ Max >0 1 Min Typ Max Unit 0.927 0.976 1.024 KHz ...
Page 9
... Figure 15). The default setting is a quadrature A/B mode including the Index signal with a pulse width of 1 LSB. The Index signal is logic high at the user programmable zero position. The AS5040 is tolerant to magnet misalignment and magnetic stray fields due to differential measurement technique and Hall sensor conditioning circuitry. Figure 4: AS5040 Block Diagram www.austriamicrosystems.com Revision 2. ...
Page 10
... MagINCn, (Magnitude Increase) becomes HIGH, when the magnet is pushed towards the IC, thus the magnetic field strength is increasing. MagDECn, (Magnitude Decrease) becomes HIGH, when the magnet is pulled away from the IC, thus the magnetic field strength is decreasing. Both signals HIGH indicate a magnetic field that is out of the allowed range (see Table 3). www.austriamicrosystems.com ...
Page 11
... The last data bit of the first device (Parity) is followed by a logic low bit and the first data bit of the second device (D9), etc… (see Figure 7). www.austriamicrosystems.com Mag Mag Parity ...
Page 12
... In both modes (quad A/B, step/direction) the resolution and the index output are user programmable. The index pulse indicates the zero position and is by default one angular step (1LSB) wide. However, it can be set to three LSBs by programming the Index-bit of the OTP register accordingly (see Table 6). www.austriamicrosystems.com CSn CLK ...
Page 13
... A change of the magnet’s rotational direction back to position „x+3“ means, that the incremental output still remains unchanged for the duration of 2 LSB, until position „x+2“ is reached. Following this direction, the incremental outputs will again be updated with every change of the magnet position. www.austriamicrosystems.com M echanical Rotation Direction ...
Page 14
... The PWM frequency is internally trimmed to an accuracy of ±5% (±10% over full temperature range). This tolerance can be cancelled by measuring the complete duty cycle as shown above. Figure 10: PWM Output Signal Angle 0 deg (Pos 0) 359.65 deg (Pos 1023) www.austriamicrosystems.com Hysteresis: 0.7° ...
Page 15
... In this case the pulse width is 256 positions, equal to 90 degrees. The precise physical angle at which the U, V and W signals change state (“Angle” in Figure 12 and Figure 13) is calculated by multiplying each transition position by the angular value of 1 count: Angle [deg] = Position x (360 degree / 1024) www.austriamicrosystems.com Typ Unit 0.9756 kHz Signal period: 1025µ ...
Page 16
... The specified programming voltage at pin Prog is 7.3 – 7.5V (see section 0). To compensate for the voltage drop across the V switching transistor, the applied programming voltage may be set slightly higher (7.5 - 8.0V, see PROG Figure 16). www.austriamicrosystems.com (One-pole-pair) Width: 512 Steps 341 512 119 ...
Page 17
... Div0,Div1 : 00 = incremental resolution = 10bit Md0, MD1 incremental mode = quadrature Figure 14: Programming Access – Write Data (section of Figure 15) Figure 15: Complete Programming Sequence Write Data CSn Prog CLK PROG t www.austriamicrosystems.com Programming Mode Data 1 t PrgH Load PROG t PrgR t PROG Revision 2.10 Power Off 7 ...
Page 18
... Md1 = Md0 = 1 changes the incremental output pins 3, 4 and 3-phase commutation signal. Div1 defines the number of pulses per revolution for either a two-pole (Div1=0) or four-pole (Div1=1) rotor. In addition, the LSB is available at pin 12 (the LSB signal replaces the PWM signal), which allows for high rotational speed measurement 30,000 rpm. www.austriamicrosystems.com Revision 2. ...
Page 19
... Note: The zero position value may also be modified before programming, e.g. to program an electrical zero position that is 180° (half turn) from the mechanical zero position, just add 512 to the value read at the mechanical zero position and program the new value into the OTP register. www.austriamicrosystems.com Div1 Div0 ...
Page 20
... A reading between 100mV and 1V indicates a faulty bit, which may result in an undefined digital value, when the OTP is read at power-up. th Following the 16 clock (after reading bit “ccw”), the chip must be reset by disconnecting the power supply. Figure 17: OTP Register Analog Read ita www.austriamicrosystems.com iv1 Revision 2.10 ref ...
Page 21
... The VDD3V3 output is intended for internal use only It must not be loaded with an external load. The output voltage of the digital interface I/O’s corresponds to the voltage at pin VDD5V, as the I/O buffers are supplied from this pin (see Figure 19). www.austriamicrosystems.com Read-out AlignMode enable via SSI 2µ ...
Page 22
... The magnet’s field strength perpendicular to the die surface should be verified using a gauss-meter. The magnetic field given distance, along a concentric circle with a radius of 1.1mm (R1), should be in the range of v ±45mT…±75mT. (see Figure 20). www.austriamicrosystems.com 3.3V Operation 2.2...10µF VDD5V Internal ...
Page 23
... The magnet’s center axis should be aligned within a displacement radius R IC with reference to the edge of pin #1 (see Figure 21). This radius includes the placement tolerance of the chip within the SSOP-16 package (+/- 0.235mm). The displacement radius R (see section 13: Alignment Mode) www.austriamicrosystems.com typ. 6mm diameter S Vertical field ...
Page 24
... The Hall sensors in the area of magnetic sensitivity are grouped and configured such that orthogonally related components of the magnetic fields are sampled differentially. The differential signal Y1-Y2 will give a sine vector of the magnetic field. The differential signal X1-X2 will give an orthogonally related cosine vector of the magnetic field. www.austriamicrosystems.com Package surface 0.576mm ± ...
Page 25
... CSn is pulled low. If CSn is already tied to VSS during power-up, the incremental outputs will all be high until the internal offset compensation is finished (within t ). PwrUp www.austriamicrosystems.com ° Revision 2. ±75mT at the surface of ...
Page 26
... The total nonlinearity error over process tolerances, temperature and a misalignment circle radius of 0.25mm is specified better than ±1.4 degrees. The magnet used for this measurement was a cylindrical NdFeB (Bomatec® BMN-35H) magnet with 6mm diameter and 2.5mm in height. www.austriamicrosystems.com max Linearity Error over XY-misalignment [°] 6 ...
Page 27
... B and Index. However, the algorithm used to generate the incremental outputs guarantees no missing or additional pulses even at high speeds (up to 30,000 rpm and higher statistically, 1 sigma represents 68.27% of readings, 3 sigma represents 99.73% of readings. www.austriamicrosystems.com linearity error with centered magnet [degrees] Err max Err mi Revision 2.10 ...
Page 28
... This delay is 48µs for the absolute interface and 192µs for the incremental interface. Using the SSI interface for absolute data transmission, an additional delay must be considered, caused by the asynchronous sampling (t= 0…1/f www.austriamicrosystems.com Incremental Output Mode @ 10 bit resolution (512ppr): max ...
Page 29
... Accuracy over Temperature The influence of temperature in the absolute accuracy is very low. While the accuracy is ≤ ±0.5° at room temperature, it may increase to ≤±0.9° due to increasing noise at high temperatures. www.austriamicrosystems.com and T also have the same tolerance as the internal oscillator. on off ...
Page 30
... Generally, the timing tolerance has no influence in the accuracy or resolution of the system used mainly for internal clock generation. The only concern to the user is the width of the PWM output pulse, which relates directly to the timing tolerance of the internal oscillator. This influence however can be cancelled by measuring the complete PWM duty cycle (see Internal Timing Tolerance). www.austriamicrosystems.com Revision 2. ...
Page 31
... E 7.65 7.8 7.9 E1 5.2 5.3 5.38 e 0.65 K 0° - 8° L 0.63 0.75 0.95 www.austriamicrosystems.com AYWWIZZ AS5040 Marking: AYWWIZZ inch A: Pb-free Identifier Y: Last Digit of Manufacturing Year Min Typ Max WW: Manufacturing Week .068 .073 .078 I: Plant Identifier .002 .005 .008 ZZ: Traceability Code ...
Page 32
... Data Sheet 20 Packing Options Delivery: Tape and Reel (1 reel = 2000 devices) Tubes (1 box = 100 tubes à 77 devices) Order # AS5040ASSU for delivery in tubes Order # AS5040ASST for delivery in tape and reel 21 Recommended PCB Footprint www.austriamicrosystems.com Recommended Footprint Data mm inch A 9.02 0.355 B 6.16 0.242 C 0 ...
Page 33
... AG for each application. The information furnished here by austriamicrosystems AG is believed to be correct and accurate. However, austriamicrosystems AG shall not be liable to recipient or any third party for any damages, including but not limited to personal injury, property damage, loss of profits, loss of use, interruption of business or indirect, special, incidental or consequential damages, of any kind, in connection with or arising out of the furnishing, performance or use of the technical data herein ...