Z8FMC160100KIT Zilog, Z8FMC160100KIT Datasheet - Page 2
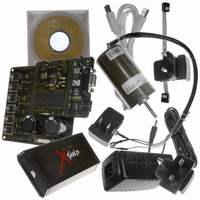
Z8FMC160100KIT
Manufacturer Part Number
Z8FMC160100KIT
Description
KIT DEV FOR Z8 ENCORE Z8FMC16100
Manufacturer
Zilog
Series
Z8 Encore! MC™r
Datasheets
1.Z8FMC160100KIT.pdf
(7 pages)
2.Z8FMC160100KIT.pdf
(383 pages)
3.Z8FMC160100KIT.pdf
(20 pages)
Specifications of Z8FMC160100KIT
Main Purpose
Power Management, Motor Control
Embedded
Yes, MCU, 8-Bit
Utilized Ic / Part
Z8FMC16100
Primary Attributes
3-Ph DC Motors
Secondary Attributes
Graphic User Interface
Processor To Be Evaluated
Z8FMC16100
Data Bus Width
8 bit
Interface Type
USB
For Use With
269-4664 - KIT ACC OPTO-ISO USB SMART CABLE269-4661 - KIT ACC ETHERNET SMART CABLE269-4539 - KIT ACCESSORY USB SMART CABLE
Lead Free Status / RoHS Status
Contains lead / RoHS non-compliant
Other names
269-3639
Discussion
The use of BLDC motors has steadily increased over the last several years as the cost of these motors and the
technology to control these motors has decreased and the benefits of these motors over other motor types has
become more important than just the initial cost. Variable speed motor applications in industries such as White
Goods, Automotive, Aerospace, Medical, and Industrial Automation are now using the BLDC motor over
other types of motors, such as Brushed DC and AC Induction.
The construction of a BLDC motor gives it several advantages when compared to other electric motors. First,
since the BLDC uses electronic commutation it has a longer life when compared with brushed DC motors and
requires less maintenance since the brushes on the motor do not require cleaning and replacement. They also
run much quieter, both electrically and audibly, because the motor does not have brush arcing and the
mechanical commutation of other types of motors. A BLDC motor will generally have a higher output per
frame size since the windings are connected to the stator and the heat generated from running can be
transferred directly to the motor housing allowing cooler operation. Finally, a BLDC motor will have much
lower electrical and friction losses because they don’t need to transfer power from the brushes. These losses
are most prevalent at lower loads. The data has shown that a standard BLDC motor will have 5-10% better
efficiency than typical AC induction motors and 8-12% better efficiency than brushed DC motors.
Multiple control methods exist for BLDC motor, and the selection is based on the requirements of the
applications. The most cost effective is sensorless control. When using this method, the back EMF of the un-
energized coil is used to determine the rotor position. However, when starting the motor, no back EMF is
generated when the rotor is not in motion, so the motor can move in the wrong direction for a small period of
time until the rotor position is determined. Sensorless control can be implemented with a few discrete
components and a small amount of firmware, which make it very attractive from a cost standard point when
some small initial movement of the motor is not a safety issue.
Theory of Operation
In a Brushless DC motor, the rotor uses permanent magnets, while the stator windings are similar to those in
AC induction motors. For a detailed discussion of the BLDC motor fundamentals, as well as closed-loop
control using sensorless techniques, refer to the Motor Control Electronics Handbook by Richard Valentine,
McGraw-Hill, NY, 1998.
In a Brushed DC motor, commutation is controlled by brush position. In a BLDC motor, however,
commutation is controlled by the supporting circuitry. The rotor's position must therefore be fed back to the
supporting circuitry to enable proper commutation.
Two different techniques can be used to determine rotor position:
•
AN022602-0810
Hall Sensor-based commutation–In the Hall sensor technique, three Hall sensors are placed inside the
motor, spaced 120 degrees apart. Each Hall sensor provides either a High or Low output based on the
polarity of magnetic pole close to it. Rotor position is determined by analyzing the outputs of all three Hall
sensors. Based on the output from Hall sensors, the voltages to the motor's three phases are switched.
The advantage of Hall sensor-based commutation is that the control algorithm is simple and easy to
understand. Hall sensor-based commutation can also be used to run the motor at very low speeds. The
disadvantages are that its implementation requires both separate Hall sensors inside the motor housing and
Sensorless Brushless DC Motor Control with Z8 Encore! MC
TM
Microcontrollers
Page 2 of 20