LM22677TJ-ADJ National Semiconductor, LM22677TJ-ADJ Datasheet - Page 9
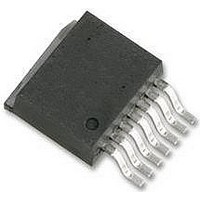
LM22677TJ-ADJ
Manufacturer Part Number
LM22677TJ-ADJ
Description
REGULATOR, ADJ. VOLTAGE, 5A 7TO263
Manufacturer
National Semiconductor
Datasheet
1.LM22677TJ-ADJ.pdf
(16 pages)
Specifications of LM22677TJ-ADJ
Primary Input Voltage
42V
No. Of Outputs
1
Output Current
5A
Voltage Regulator Case Style
TO-263
No. Of Pins
7
Operating Temperature Range
-40°C To +125°C
Svhc
No SVHC (15-Dec-2010)
Package
RoHS Compliant
Available stocks
Company
Part Number
Manufacturer
Quantity
Price
Part Number:
LM22677TJ-ADJ
Manufacturer:
NS/国半
Quantity:
20 000
Company:
Part Number:
LM22677TJ-ADJ/NOPB
Manufacturer:
TI
Quantity:
2 513
Part Number:
LM22677TJ-ADJ/NOPB
Manufacturer:
TI/德州仪器
Quantity:
20 000
of 5V or higher is needed, the -5.0 option with an additional
external resistor divider may also be used.
The typical location of the internal compensation poles and
zeros as well as the DC gain is given in Table 1. The LM22677
has internal type III compensation allowing for the use of most
output capacitors including ceramics.
This information can be used to calculate the transfer function
from the FB pin to the internal compensation node (input to
the PWM comparator in the block diagram).
For the power stage transfer function the standard voltage
mode formulas for the double pole and the ESR zero apply:
The peak ramp level of the oscillator signal feeding into the
PWM comparator is V
this modulator stage of the IC. The -5.0 fixed output voltage
option has twice the gain of the compensation transfer func-
tion compared to the -ADJ option which is 43.5dB instead of
37.5dB.
Generally, calculation as well as simulation can only aid in
selecting good power stage components. A good design prac-
tice is to test for stability with load transient tests or loop
measurement tests. Application note AN-1889 shows how to
easily perform a loop transfer function measurement with only
an oscilloscope and a function generator.
Application Information
EXTERNAL COMPONENTS
The following design procedures can be used to design a non-
synchronous buck converter with the LM22677.
Inductor
The inductor value is determined based on the load current,
ripple current, and the minimum and maximum input voltage.
To keep the application in continuous current conduction
mode (CCM), the maximum ripple current, I
less than twice the minimum load current.
The general rule of keeping the inductor current peak-to-peak
ripple around 30% of the nominal output current is a good
compromise between excessive output voltage ripple and ex-
cessive component size and cost. Using this value of ripple
current, the value of inductor, L, is calculated using the fol-
lowing formula:
Corners
DC gain
Zero 1
Zero 2
Pole 1
Pole 2
Pole 3
IN
/10 which equals a gain of 20dB of
TABLE 1.
Frequency
150 kHz
250 kHz
37.5 dB
1.5 kHz
100 Hz
15 kHz
RIPPLE
, should be
9
where F is the switching frequency which is 500 kHz without
an external frequency set resistor or external sync signal ap-
plied to the RT/SYNC pin. If the switching frequency is set
higher than 500kHz, the inductance value may not be reduced
accordingly due to stability requirements. The internal com-
pensation is optimized for circuits with a 500 kHz switching
frequency. See the internal compensation section for more
details. This procedure provides a guide to select the value of
the inductor L. The nearest standard value will then be used
in the circuit.
Increasing the inductance will generally slow down the tran-
sient response but reduce the output voltage ripple amplitude.
Reducing the inductance will generally improve the transient
response but increase the output voltage ripple.
The inductor must be rated for the peak current, I
vent saturation. During normal loading conditions, the peak
current occurs at maximum load current plus maximum ripple.
Under an overload condition as well as during load transients,
the peak current is limited to 7.1A typical (8.75A maximum).
This requires that the inductor be selected such that it can run
at the maximum current limit and not only the steady state
current.
Depending on inductor manufacturer, the saturation rating is
defined as the current necessary for the inductance to reduce
by 30% at 20°C. In typical designs the inductor will run at
higher temperatures. If the inductor is not rated for enough
current, it might saturate and due to the propagation delay of
the current limit circuitry, the power supply may get damaged.
Input Capacitor
Good quality input capacitors are necessary to limit the ripple
voltage at the VIN pin while supplying most of the switch cur-
rent during on-time. When the switch turns on, the current into
the VIN pin steps to the peak value, then drops to zero at turn-
off. The average current into VIN during switch on-time is the
load current. The input capacitance should be selected for
RMS current, I
proximation for the required ripple current rating necessary is
I
Quality ceramic capacitors with a low ESR should be selected
for the input filter. To allow for capacitor tolerances and volt-
age effects, multiple capacitors may be used in parallel. If step
input voltage transients are expected near the maximum rat-
ing of the LM22677, a careful evaluation of ringing and pos-
sible voltage spikes at the VIN pin should be completed. An
additional damping network or input voltage clamp may be
required in these cases.
Usually putting a higher ESR electrolytic input capacitor in
parallel to the low ESR bypass capacitor will help to reduce
excessive voltages during a line transient and will also move
the resonance frequency of the input filter away from the reg-
ulator bandwidth.
Output Capacitor
The output capacitor can limit the output ripple voltage and
provide a source of charge for transient loading conditions.
Multiple capacitors can be placed in parallel. Very low ESR
capacitors such as ceramic capacitors reduce the output rip-
ple voltage and noise spikes, while larger higher ESR capac-
itors in parallel provide large bulk capacitance for transient
loading conditions. An approximation for the output voltage
ripple is:
RMS
> I
OUT
/ 2.
RMS
, and minimum ripple voltage. A good ap-
www.national.com
PK+
, to pre-