3059Y-1-500LF Bourns Inc., 3059Y-1-500LF Datasheet - Page 159
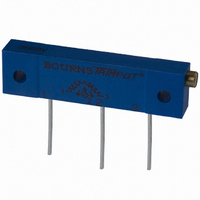
3059Y-1-500LF
Manufacturer Part Number
3059Y-1-500LF
Description
TRIMPOT 50 OHM 1.25"REC CER MT
Manufacturer
Bourns Inc.
Series
3059 - Sealedr
Specifications of 3059Y-1-500LF
Temperature Coefficient
±100ppm/°C
Resistance (ohms)
50
Termination Style
PC Pin
Power (watts)
1W
Tolerance
±10%
Number Of Turns
22
Adjustment Type
Side Adjustment
Resistive Material
Cermet
Mounting Type
Chassis Mount
Package / Case
Rectangular - 1.250" L x 0.190" W x 0.315" H (31.75mm x 4.83mm x 8.00mm)
Track Resistance
50ohm
No. Of Turns
22
Resistance Tolerance
± 10%
Power Rating
1W
Potentiometer Mounting
Through Hole
Resistance
50 Ohms
Operating Temperature Range
- 55 C to + 150 C
Element Type
Cermet
Dimensions
6.10 mm W x 31.75 mm L
Product
Trimmers
Taper
Linear
Rohs Compliant
Yes
Lead Free Status / RoHS Status
Lead free / RoHS Compliant
Lead Free Status / RoHS Status
Lead free / RoHS Compliant, Lead free / RoHS Compliant
- Current page: 159 of 172
- Download datasheet (7Mb)
Standard Soldering and Cleaning Processes
Solder
6
Reflow; Hot Air,
IR and Vapor
Phase
GENERAL
Preheat sufficiently
using both time
and temperature
to vaporize all
solder paste
solvents and
moisture, leaving
only solder and
flux as component
enters solder
reflow phase.
RECOMMENDED
Solder zone profile
of 230 °C for 20
seconds.
CAUTION
Do not exceed time
and temperature
reflow profile of
235 °C for 45 ±5
seconds for hot air/IR
reflow and 215 °C
for 3 minutes for
vapor phase reflow.
Use 215 °C as
minimum reflow
temperature.
Minimize thermal
shock by limiting
temperature rise
rate to 3 °C/sec
and by stabilizing
board and compo-
nents temperature
during preheating.
Solder
7
Flow (Wave)
GENERAL
For maximum com-
ponent reliability
and performance,
minimize the time
of temperature
exposure above
200 °C.
RECOMMENDED
Use SN 63 %
Pb 37 % solder.
Solder zone profile
of 245 °C for
5 seconds.
CAUTION
Do not exceed
260 °C peak temp-
erature for dual
wave solder
process with a flow
zone totaling 5
seconds.
Minimize thermal
shock by limiting
temperature rise
rate to 3 °C/sec
and by stabilizing
board and compo-
nents temperature
during preheating.
8
Wash
Solvent
GENERAL
Use solvent clean-
ing primarily for
nonpolar contam-
inants such as
rosin based flux
residues.
RECOMMENDED
Use any suitable
washing solvents
that meet ODC
requirements.
CAUTION
Limit excessive
direct spray
pressure to 60 psi
or below for opti-
mum reliability.
9
Wash
Semi-Aqueous
GENERAL
Use semi-aqueous
for nonpolar
contaminants such
as rosin based flux
residues.
RECOMMENDED
Use terpene or
hydrocarbon
based for pre-
wash. Use water
for final wash.
CAUTION
Limit excessive
direct spray
pressure to 60 psi
or below for opti-
mum reliability.
GENERAL
Excessive and/or repeated
high temperature heat
exposure may affect
component performance
and reliability.
Board Rework Technique
10
Wash
Aqueous
GENERAL
Use aqueous cleaning
primarily for polar
contaminants such as
organic flux residues.
RECOMMENDED
Use any of these
aqueous wash
materials:
• Deionized water
• Surfactants
• Saponifiers
CAUTION
Limit excessive
direct spray pressure
to 60 psi or below for
optimum reliability.
Ultrasonics may
cause component
damage or failure.
RECOMMENDED
Hot air reflow technique
is preferred.
CAUTION
Avoid use of a soldering
iron or wave soldering as
a rework technique.
11
No-Wash
GENERAL
No-wash is an
option when
no-clean (low
solids) flux is
used for solder
operations.
157
Related parts for 3059Y-1-500LF
Image
Part Number
Description
Manufacturer
Datasheet
Request
R

Part Number:
Description:
POT 500K OHM 1-1/4" RECT CERM MT
Manufacturer:
Bourns Inc.
Datasheet:

Part Number:
Description:
POT 100 OHM 1-1/4" RECT CERM MT
Manufacturer:
Bourns Inc.
Datasheet:

Part Number:
Description:
POT 10K OHM 1-1/4" RECT CERM MT
Manufacturer:
Bourns Inc.
Datasheet:

Part Number:
Description:
POT 100K OHM 1-1/4" RECT CERM MT
Manufacturer:
Bourns Inc.
Datasheet:

Part Number:
Description:
POT 1.0K OHM 1-1/4" RECT CERM MT
Manufacturer:
Bourns Inc.
Datasheet:

Part Number:
Description:
POT 50K OHM 1-1/4" RECT CERM MT
Manufacturer:
Bourns Inc.
Datasheet:

Part Number:
Description:
POT 2.0K OHM 1-1/4" RECT CERM MT
Manufacturer:
Bourns Inc.
Datasheet:

Part Number:
Description:
POT 200K OHM 1-1/4" RECT CERM MT
Manufacturer:
Bourns Inc.
Datasheet:

Part Number:
Description:
POT 20K OHM 1-1/4" RECT CERM MT
Manufacturer:
Bourns Inc.
Datasheet:

Part Number:
Description:
POT 1.0M OHM 1-1/4" RECT CERM MT
Manufacturer:
Bourns Inc.
Datasheet:

Part Number:
Description:
Manufacturer:
Bourns, Inc.
Datasheet:

Part Number:
Description:
11mm Potentiometer
Manufacturer:
Bourns, Inc.
Datasheet: