AD9238BSTRL-20 Analog Devices Inc, AD9238BSTRL-20 Datasheet - Page 21
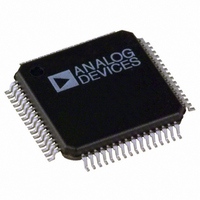
AD9238BSTRL-20
Manufacturer Part Number
AD9238BSTRL-20
Description
IC ADC 12BIT DUAL 20MSPS 64-LQFP
Manufacturer
Analog Devices Inc
Datasheet
1.AD9238BSTZ-40.pdf
(48 pages)
Specifications of AD9238BSTRL-20
Rohs Status
RoHS non-compliant
Number Of Bits
12
Sampling Rate (per Second)
20M
Data Interface
Parallel
Number Of Converters
2
Power Dissipation (max)
180mW
Voltage Supply Source
Single Supply
Operating Temperature
-40°C ~ 85°C
Mounting Type
Surface Mount
Package / Case
64-LQFP
AD9238 LQFP EVALUATION BOARD
The evaluation board supports both the AD9238 and AD9248
and has five main sections: clock circuitry, inputs, reference
circuitry, digital control logic, and outputs. A description of
each section follows. Table 8 shows the jumper settings and
notes assumptions in the comment column.
Four supply connections to TB1 are necessary for the evaluation
board: the analog supply of the DUT, the on-board analog
circuitry supply, the digital driver DUT supply, and the on-
board digital circuitry supply. Separate analog and digital
supplies are recommended, and on each supply 3 V is nominal.
Each supply is decoupled on-board, and each IC, including the
DUT, is decoupled locally. All grounds should be tied together.
CLOCK CIRCUITRY
The clock circuitry is designed for a low jitter sine wave source
to be ac-coupled and level shifted before driving the 74VHC04
hex inverter chips (U8 and U9) whose output provides the clock
to the part. The POT (R32 and R31) on the level shifting
circuitry allows the user to vary the duty cycle if desired. The
amplitude of the sine wave must be large enough for the trip
points of the hex inverter and within the supplies to avoid noise
from clipping. To ensure a 50% duty cycle internal to the part,
the AD9238-65 has an on-chip duty cycle stabilizer circuit that
is enabled by putting in Jumper JP11. The duty cycle stabilizer
circuitry should only be used at clock rates above 40 MSPS.
Each channel has its own clock circuitry, but normally both
clock pins are driven by a single 74VHC04, and the solder
Jumper JP24 is used to tie the clock pins together. When the
clock pins are tied together and only one 74VHC04 is being
used, the series termination resistor for the other channel must
be removed (either R54 or R55, depending on which inverter is
being used).
A data capture clock for each channel is created and sent to the
output buffers in order to be used in the data capture system if
needed. Jumpers JP25 and JP26 are used to invert the data clock
if necessary and can be used to debug data capture timing
problems.
ANALOG INPUTS
The AD9238 achieves the best performance with a differential
input. The evaluation board has two input options for each
channel, a transformer (XFMR) and an AD8138, both of which
perform single-ended-to-differential conversions. The XFMR
allows for the best high frequency performance, and the AD8138 is
ideal for dc evaluation, low frequency inputs, and driving an
ADC differentially without loading the single-ended signal.
Rev. C | Page 21 of 48
The common-mode level for both input options is set to
midsupply by a resistor divider off the AVDD supply but can
also be overdriven with an external supply using the (test
points) TP12, TP13 for the AD8138s and TP14, TP15 for the
XFMRs. For low distortion of full-scale input signals when
using an AD8138, put JP17 and JP22 in Position B and put an
external negative supply on TP10 and TP11.
For best performance, use low jitter input sources and a high
performance band-pass filter after the signal source, before the
evaluation board (see Figure 39). For XFMR inputs, use solder
Jumpers JP13, JP14 for Channel A and JP20, JP21 for Channel B.
For AD8138 inputs, use solder Jumpers JP15, JP16 for Channel
A and JP18, JP19 for Channel B. Remove all solder from the
jumpers not being used.
REFERENCE CIRCUITRY
The evaluation board circuitry allows the user to select a reference
mode through a series of jumpers and provides an external
reference if necessary. Refer to Table 9 to find the jumper settings
for each reference mode. The external reference on the board is
a simple resistor divider/zener diode circuit buffered by an
AD822 (U4). The POT (R4) can be used to change the level of
the external reference to fine adjust the ADC full scale.
DIGITAL CONTROL LOGIC
The digital control logic on the evaluation board is a series of
jumpers and pull-down resistors used as digital inputs for the
following pins on the AD9238: the power-down and output
enable bar for each channel, the duty cycle restore circuitry, the
twos complement output mode, the shared reference mode, and
the MUX_SELECT pin. Refer to Table 8 for normal operating
jumper positions.
OUTPUTS
The outputs of the AD9238 (and the data clock discussed earlier)
are buffered by 74VHC541s (U2, U3, U7, U10) to ensure the
correct load on the outputs of the DUT, as well as the extra drive
capability to the next part of the system. The 74VHC541s are
latches, but on this evaluation board, they are wired and
function as buffers. JP30 can be used to tie the data clocks
together if desired. If the data clocks are tied, R39 or R40 must
be removed, depending on which clock circuitry is being used.
AD9238