ES-TN-1H5 BANNER ENGINEERING, ES-TN-1H5 Datasheet - Page 9
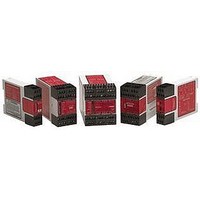
ES-TN-1H5
Manufacturer Part Number
ES-TN-1H5
Description
MODULE; SAFETY; E-STOP GUARD; MONITORING MODULE
Manufacturer
BANNER ENGINEERING
Datasheet
1.ES-TN-1H5.pdf
(16 pages)
Specifications of ES-TN-1H5
Coil Voltage Vdc Nom
24V
Contact Current Max
4A
Contact Voltage Ac Nom
250V
Contact Voltage Dc Nom
250V
Contact Configuration
SPST-NC
No. Of Poles
1
Relay Mounting
DIN Rail
External Height
85.5mm
reset routine be performed after returning
the E-stop switch to its closed-contact
position (arming the E-stop switch). When
Automatic Reset is used, an alternate
means must be established to require a
reset routine, after the E-stop switch is
armed. Allowing the machine to restart
as soon as the E-stop switch is armed
creates an unsafe condition which could
result in serious injury or death.
a momentary loss of power could cause
the outputs to energize, even without a
manual reset, when the power resumes.
Be sure that this Auto Power-Up situation
does not cause the machine to restart, or
an unsafe condition may occur that could
result in serious injury or death.
Banner Engineering Corp.
www.bannerengineering.com • Tel: 763.544.3164
!
!
E-Stop Safety Modules with Adjustable Delay
WARNING . . .
Auto Power-Up and
Momentary Power Loss
If Auto Power-Up is selected,
WARNING . . .
Routine Required
ANSI B11 and NFPA 79
standards require that a
•
Minneapolis, MN U.S.A.
Reset
The E-Stop Safety Module may be configured for Automatic Reset via two independent
DIP switches, located inside the Module housing, under the front cover (see Figures 5
and 6) and by replacing the Reset switch with a jumper wire in the X1-X2 reset input
circuit (see Figure 3).
The E-Stop Safety Module will reset (and the outputs energize) as soon as the E-Stop
switch returns to its closed-contact position (S11-S12 and S21-S22 closed), feedback
inputs are closed (X3-X4 and X5-X6), and no fault exists. Automatic Reset will not
occur if Manual Power-up is selected and the E-stop switch is already closed when
power is applied.
Automatic reset mode is useful for some automated processes. However, if Automatic
Reset is used, it is necessary to provide a means of preventing resumption of
hazardous machine motion, until an alternate reset procedure is performed. The
alternate procedure must include a Reset switch, located outside the area of dangerous
motion, which is positioned so that any area of dangerous motion may be observed by
the switch operator during the reset procedure.
NOTE: The minimum amount of time required for the Module to be in a STOP or
If the Module is programmed for Auto Power-Up (see Figures 6 and 7), K1-K4 relays
will close as soon as power is connected to A1-A2 – if the E-stop inputs S11-S12 and
S21-S22 are closed, the appropriate jumpers are installed and feedback contacts X3-X4
and X5-X6 are closed, whether the Module is programmed for Auto or Manual Reset.
Auto Reset may be used only if the machine being controlled will not initiate dangerous
motion if power is applied to or interrupted from the module. In addition, an alternate
Reset routine must be required (see WARNING at left).
The next time the E-stop is cycled when the Module is set to Manual Reset, the Reset
button at X1-X2 must go from open to closed and back to open in order to reset the
unit and energize the four internal relays.
NOTE: Auto Power-Up in combination with Manual Reset energizes the output contacts
If the DIP switches are set to Manual Power-Up and Manual Reset, the unit will reset
only after power is applied and the Reset button is pushed and released. If Manual
Power-Up and Auto Reset is selected, the E-stop button must be cycled (opened and
closed) if it is closed after power up (but simply closed if it is open after power-up).
Automatic Reset Mode
Auto Power-Up
Manual Power-Up
OFF condition is 100 ms. This “recovery time” (OFF-state) is required for the
internal circuitry of the Safety Module to normalize, allowing a reliable reset
to occur. A lockout will occur if the Module is cycled too quickly. To clear
the lockout, the Module must be re-cycled, meeting the minimum OFF time
requirement.
automatically only one time after applying power to the Module. Cycling the
E-stop button while power is applied will not reset the unit.
Configuration
— Models ES-TN-1H5/-1H6
P/N 58697 rev. A
9