LM96194CISQ/NOPB National Semiconductor, LM96194CISQ/NOPB Datasheet - Page 31
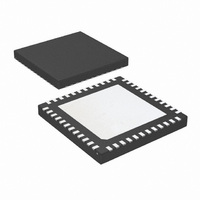
LM96194CISQ/NOPB
Manufacturer Part Number
LM96194CISQ/NOPB
Description
IC TRUTHERM HDWR MONITOR 48-LLP
Manufacturer
National Semiconductor
Series
PowerWise®, TruTherm®r
Datasheet
1.LM96194CISQNOPB.pdf
(106 pages)
Specifications of LM96194CISQ/NOPB
Function
Fan Control, Temp Monitor
Topology
ADC (Sigma Delta), Comparator, Fan Control, Multiplexer, Register Bank
Sensor Type
External & Internal
Sensing Temperature
-40°C ~ 85°C, External Sensor
Output Type
SMBus™
Output Alarm
No
Output Fan
Yes
Voltage - Supply
3 V ~ 3.6 V
Operating Temperature
-40°C ~ 85°C
Mounting Type
Surface Mount
Package / Case
48-LLP
Lead Free Status / RoHS Status
Lead free / RoHS Compliant
Other names
LM96194CISQTR
15.10.3 Fan Control Priorities
The automatic fan control is not the only function that influ-
ences PWM duty cycle. There are several other functions that
influence the PWM duty cycle. All the functions can be clas-
sified into several categories:
The ultimate PWM duty cycle that is chosen can be described
by the following formula:
If (Manual PWM Override is active)
Else
So in general, categories 1, 2 and 3 are always active. In ad-
dition to that, either category 4 or categories 5 and 6 are active
depending on whether manual override is enabled. In this
sense the manual override, when enabled, replaces category
5 and 6.
15.10.4 PWM to 100% Conditions
There are several conditions that cause the duty cycles of all
PWM outputs to immediately get set to 100%. They are:
1.
2.
3.
15.10.5 VRD_HOT Ramp-Up/Ramp-Down
This function causes the duty cycle of the PWM outputs to
gradually increase over time if VRD_HOT is asserted.
When VRD_HOT is asserted, the ramp function is enabled.
The enabling process involves two steps:
Category
PWM = max(1,2,3,4)
PWM = max(1,2,3,5,6)
4-Bit Value
any of the four temperature zones exceed the
programmed Fan Boost Limit setting but has not yet
cooled down enough to drop below the hysteresis point
a tachometer reading exceeds its limit
the OVRID bit is set in the LM96194 Status/Control
#
1
2
3
4
5
6
Ah
Bh
Ch
Dh
Eh
Fh
8h
9h
PWM to 100% conditions
VRD_HOT ramp-up/ramp-down
PROCHOT ramp-up/ramp-down function
Manual PWM Override
Fan Spin-Up Control
Automatic Fan Control Algorithm
LUT Step
10
11
12
13
—
—
8
9
Category Name
Alternate LUT
Duty Cycle
Reserved
Reserved
100.00%
50.00%
53.57%
57.14%
71.43%
85.71%
31
1.
2.
Once the function is enabled, it gradually adds additional duty
cycle steps every X milliseconds whenever VRD_HOT is as-
serted (X is programmable via the PWM Ramp Control reg-
ister). If VRD_HOT remains asserted for a long enough time,
the duty cycle eventually reaches 100%.
Whenever VRD_HOT is de-asserted, the ramp function be-
gins to ramp down by subtracting one PWM duty cycle step
every X milliseconds. If VRD_HOT is currently de-asserted,
and the ramp function is less than to the PWM duty cycle be-
ing requested by other functions, the ramp function is dis-
abled.
As long as the function is enabled, it continues to ramp up or
ramp down depending on the state of VRD_HOT. The ramp
enabling process described above can only re-occur after the
ramp function has been disabled. Rapid assertion/de-asser-
tion of VRD_HOT does not trigger the enabling process un-
less VRD_HOT was de-asserted long enough for the ramp
function to disable itself.
This ramp function only applies to the PWM(s) that are bound
to the VRD_HOT inputs. Depending on the bindings, it is pos-
sible that up to two independent ramp functions are active at
any given moment:
PWM1/VRD
PWM2/VRD
15.10.6 PROCHOT Ramp-Up/Ramp-Down
This function is very similar to the VRD_HOT ramp-up/ramp-
down function. The PWM duty cycle ramps up in the same
fashion whenever the PROCHOT measurement exceeds the
user programmed threshold. Once a new PROCHOT mea-
surement is made that no longer exceeds the user limit, the
PWM will begin to ramp down.
Just as with the VRD_HOT ramp function, the PROCHOT
ramp function uses independent bindings to determine which
PWM outputs should be effected by each PROCHOT input.
15.10.7 Manual PWM Override
When a PWM channel is configured for manual PWM over-
ride, software can manually control the PWM duty cycle.
There are some PWM control functions that could still cause
the duty cycle to be higher than the manual setting. See the
Section 15.10.3 Fan Control Priorities
15.10.8 Fan Spin-Up Control
All of the other PWM control functions are combined to pro-
duce a final duty cycle that is actually used for the PWM
output. If this final value changes from zero to a non-zero val-
ue, the Fan Spin-Up Control function is triggered. Once trig-
gered, the Fan Spin-Up Control requests the programmed
duty cycle for a programmed period of time.
The current duty cycle being requested by other PWM
functions is memorized.
The ramp function immediately adds one PWM duty
cycle step to the memorized value and requests this duty
cycle.
for details.
www.national.com