LTC2410 Linear Technology, LTC2410 Datasheet - Page 33
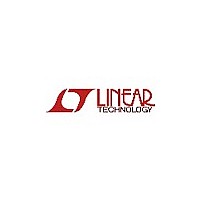
LTC2410
Manufacturer Part Number
LTC2410
Description
24-Bit No Latency ADC with Differential Input and Differential Reference
Manufacturer
Linear Technology
Datasheet
1.LTC2410.pdf
(44 pages)
Available stocks
Company
Part Number
Manufacturer
Quantity
Price
Part Number:
LTC2410CGN
Manufacturer:
LINEAR/凌特
Quantity:
20 000
Part Number:
LTC2410CGN#PBF
Manufacturer:
LINEAR/凌特
Quantity:
20 000
Part Number:
LTC2410CGN-1
Manufacturer:
LINEAR/凌特
Quantity:
20 000
Part Number:
LTC2410IGN
Manufacturer:
LINEAR/凌特
Quantity:
20 000
Part Number:
LTC2410IGN#PBF
Manufacturer:
LINEAR/凌特
Quantity:
20 000
APPLICATIO S I FOR ATIO
techniques is used to produce a precision divide operation
on the reference signal. Another option is the use of a
reference within the 5V input range of the LTC2410 and
developing excitation via fixed gain, or LTC1043 based
voltage multiplication, along with remote feedback in the
excitation amplifiers, as shown in Figures 34 and 35.
Figure 46 shows an example of a simple bridge connec-
tion. Note that it is suitable for any bridge application
where measurement speed is not of the utmost impor-
tance. For many applications where large vessels are
weighed, the average weight over an extended period of
time is of concern and short term weight is not readily
determined due to movement of contents, or mechanical
resonance. Often, large weighing applications involve load
cells located at each load bearing point, the output of
which can be summed passively prior to the signal pro-
cessing circuitry, actively with amplification prior to the
ADC, or can be digitized via multiple ADC channels and
summed mathematically. The mathematical summation
of the output of multiple LTC2410’s provides the benefit of
a root square reduction in noise. The low power consump-
tion of the LTC2410 makes it attractive for multidrop
communication schemes where the ADC is located within
the load-cell housing.
A direct connection to a load cell is perhaps best incorpo-
rated into the load-cell body, as minimizing the distance to
the sensor largely eliminates the need for protection
BRIDGE
R1 AND R2 CAN BE USED TO INCREASE TOLERABLE AC COMPONENT ON REF SIGNALS
350
R1
R2
Figure 46. Simple Bridge Connection
U
3
4
5
6
REF
REF
IN
IN
+
–
LTC2410
+
–
V
GND
U
REF
2
1, 7, 8, 9,
10, 15, 16
SDO
SCK
CS
F
O
12
13
11
14
W
+
LT1019
U
2410 F46
devices, RFI suppression and wiring. The LTC2410 exhib-
its extremely low temperature dependent drift. As a result,
exposure to external ambient temperature ranges does
not compromise performance. The incorporation of any
amplification considerably complicates thermal stability,
as input offset voltages and currents, temperature coeffi-
cient of gain settling resistors all become factors.
The circuit in Figure 47 shows an example of a simple
amplification scheme. This example produces a differen-
tial output with a common mode voltage of 2.5V, as
determined by the bridge. The use of a true three amplifier
instrumentation amplifier is not necessary, as the LTC2410
has common mode rejection far beyond that of most
amplifiers. The LTC1051 is a dual autozero amplifier that
can be used to produce a gain of 15 before its input
referred noise dominates the LTC2410 noise. This ex-
ample shows a gain of 34, that is determined by a feedback
network built using a resistor array containing 8 individual
resistors. The resistors are organized to optimize tem-
perature tracking in the presence of thermal gradients. The
second LTC1051 buffers the low noise input stage from
the transient load steps produced during conversion.
The gain stability and accuracy of this approach is very
good, due to a statistical improvement in resistor match-
ing due to individual error contribution being reduced. A
gain of 34 may seem low, when compared to common
practice in earlier generations of load-cell interfaces, how-
ever the accuracy of the LTC2410 changes the rationale.
Achieving high gain accuracy and linearity at higher gains
may prove difficult, while providing little benefit in terms
of noise reduction.
At a gain of 100, the gain error that could result from
typical open-loop gain of 160dB is –1ppm, however,
worst-case is at the minimum gain of 116dB, giving a gain
error of –158ppm. Worst-case gain error at a gain of 34,
is –54ppm. The use of the LTC1051A reduces the worst-
case gain error to –33ppm. The advantage of gain higher
than 34, then becomes dubious, as the input referred
noise sees little improvement
tially compromised.
Note that this 4-amplifier topology has advantages over
the typical integrated 3-amplifier instrumentation ampli-
fier in that it does not have the high noise level common in
1
and gain accuracy is poten-
LTC2410
33